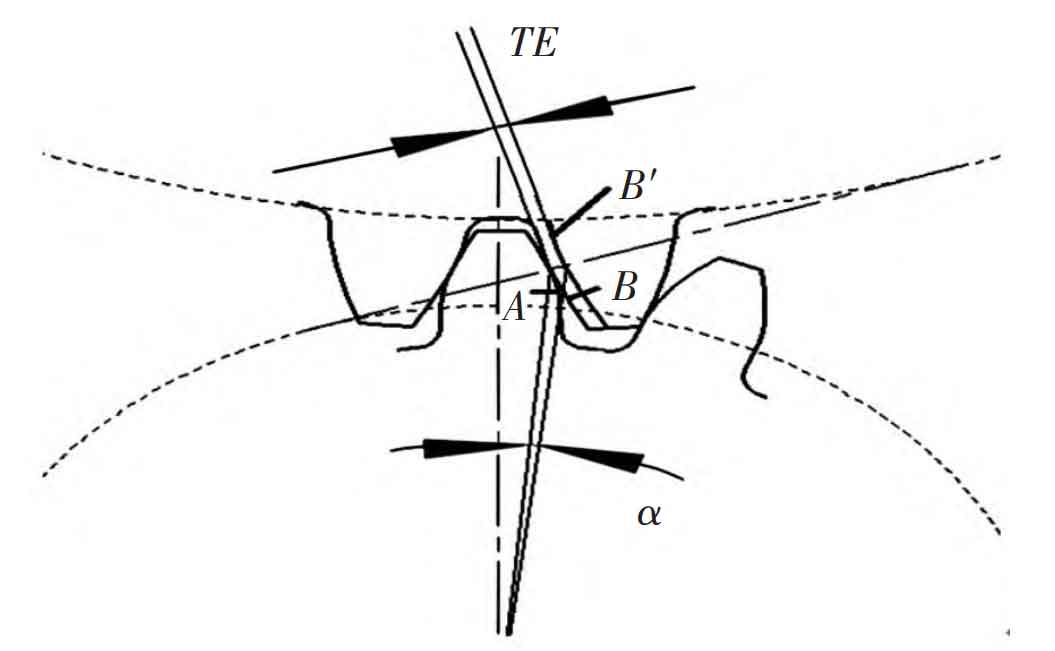
According to the relevant models and parameters of the involute planetary gear reducer, as shown in Table 1. An accurate three-dimensional model is established by using SolidWorks software. As shown in Figure 1, the gear train takes the sun gear as the input, the planet carrier as the output, the rated output torque is 330nm and the rated input speed is 3000rpm.
Parameter name | Sun wheel | Planetary gear | Inner ring gear |
Number of teeth Z | 27 | 39 | 108 |
Modulus m / mm | 0.9 | 0.9 | 0.9 |
Tooth width b / mm | 22.5 | 20 | 22 |
pressure angle α/ ° | 20° | 20° | 20° |
The above conditions are the basic conditions for the design of planetary gear reducer. In order to reduce the vibration and noise of gear train transmission and improve its transmission stability, there should be no common divisor between meshing gear pairs, and the number of teeth of sun gear should not be an integral multiple of the number of planetary gears. Here, kisssoft software is used to study these two requirements, analyze the influence of different forms on the transmission performance of planetary gear train, and get the best gear matching mode.
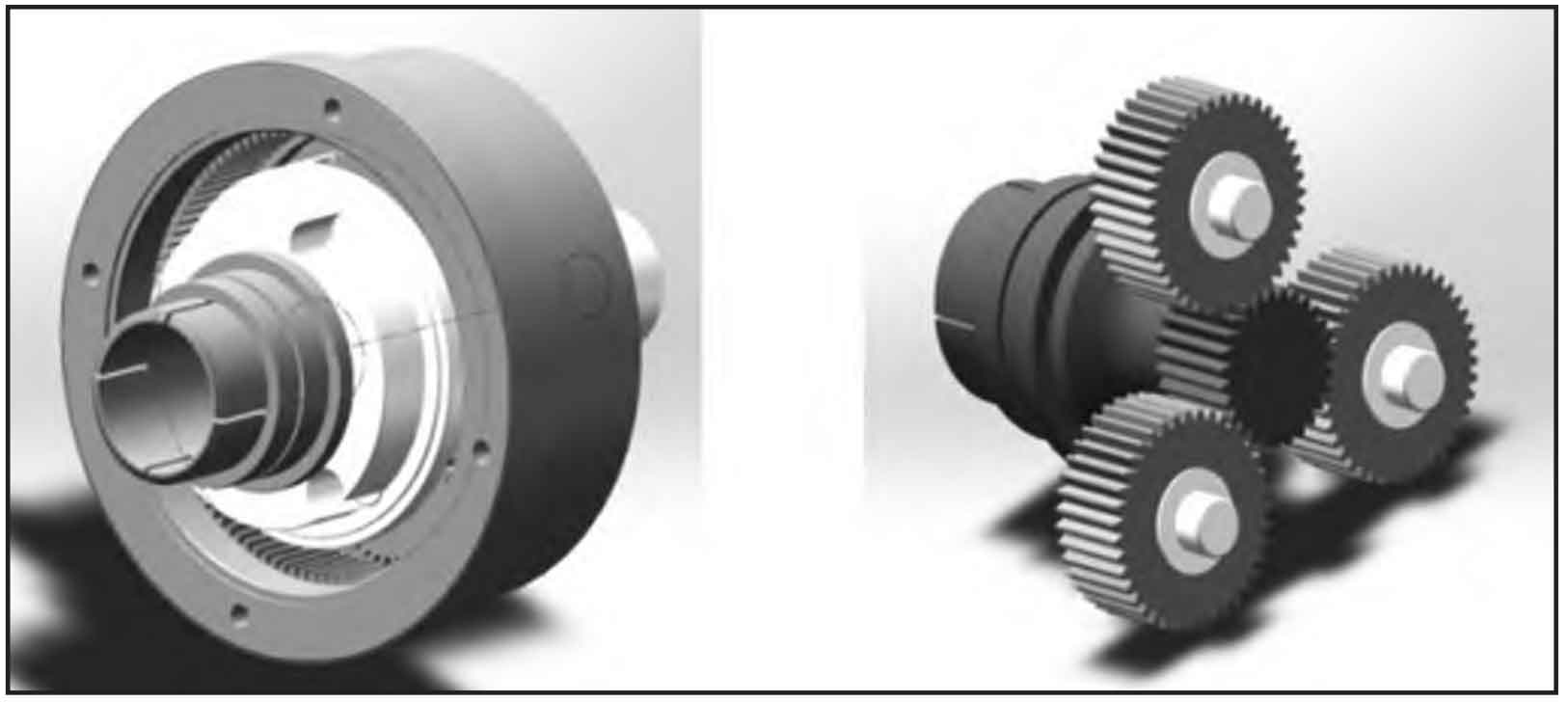
Under the condition that the working conditions and the basic original parameters of the gear such as modulus, tooth width and pressure angle remain unchanged, only the number of teeth is changed. After fine screening in kissoft software, 78 groups of data can be obtained, as shown in Figure 2.
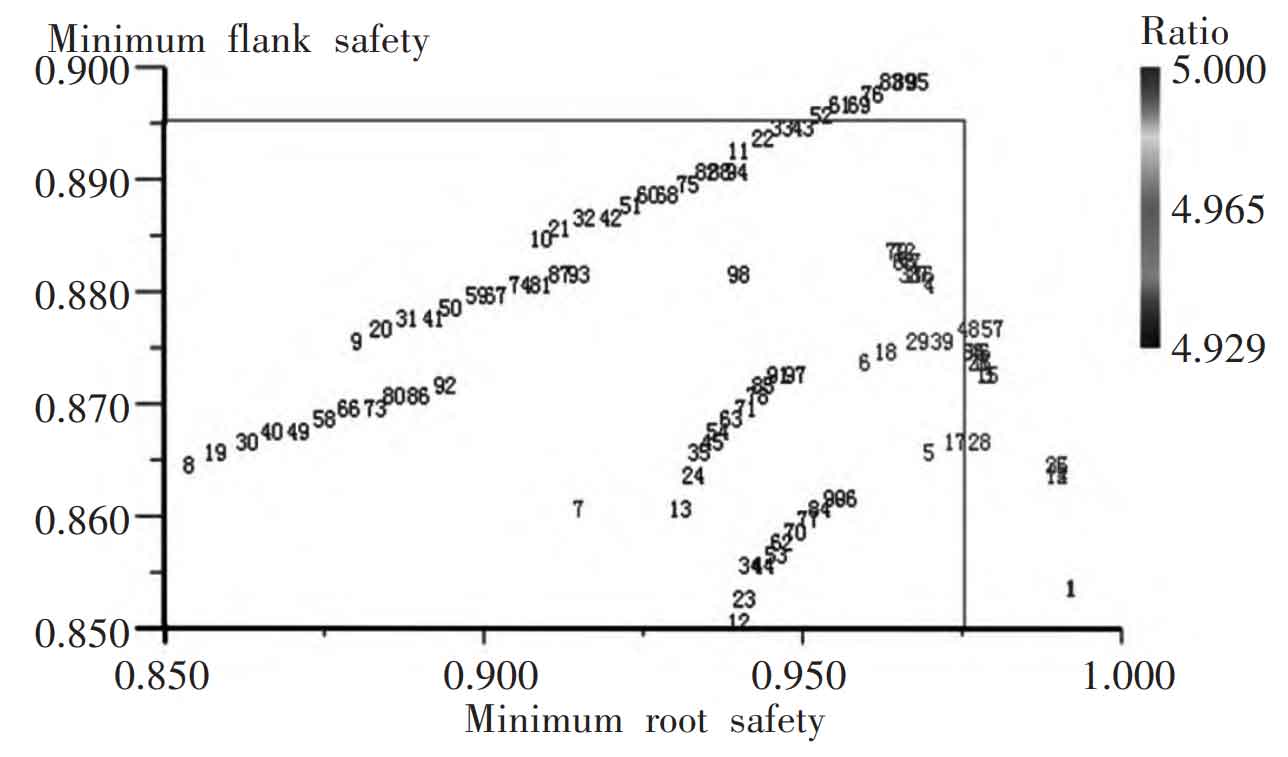
Six groups of data are selected according to the minimum bending fatigue strength and minimum contact fatigue strength of the gear, whether the number of teeth between each meshing gear pair has a common divisor and whether the number of teeth of the sun gear is an integral multiple of the number of planetary gears, as shown in Table 2.
Serial number | Sun wheel | Number of teeth Z planetary gear | Inner ring gear | Number of teeth coprime type | X |
1 | 27 | 39 | 108 | — | yes |
2 | 27 | 40 | 108 | Sun gear and planet gear | yes |
3 | 28 | 39 | 108 | Sun gear and planet gear | no |
4 | 27 | 39 | 107 | Planetary gear and internal gear ring | yes |
5 | 28 | 38 | 107 | Planetary gear and internal gear ring | no |
6 | 27 | 40 | 111 | Sun gear, planet gear and planet | yes |
7 | 29 | 40 | 109 | Wheel and internal gear ring | no |
The number of teeth of the original gear and the six groups of teeth obtained by screening are simulated and analyzed in kissoft software. In order to clearly understand the influence of different tooth number schemes on transmission error, maximum normal stiffness, maximum tangential stiffness and maximum stress, the calculated data are compared graphically, as shown in Fig. 3 ~ Fig. 6.
In Fig. 4 ~ Fig. 8, abscissa (1 ~ 7) respectively represent different tooth number schemes, 1 is the original tooth number scheme, and (2 ~ 7) are the first to sixth tooth number schemes in Table 2.
Through the analysis of the above chart, although the maximum normal stiffness and maximum tangential stiffness of the original scheme are slightly lower than those of the other six groups of schemes, through comprehensive comparison, the indexes of the planetary gear train of the seventh group of gear number scheme are the best, that is, when the number of sun gear teeth in the planetary gear train cannot be divided by the number of planet gears, and the number of sun gear and planet gear, planet gear and inner ring gear are mutually qualitative, the transmission error value and maximum stress value are smaller than those of other gear number schemes.
In order to make the calculation results more intuitive, TCA tooth contact analysis is carried out for the seventh group of gear scheme and original tooth number scheme, as shown in Fig. 9 ~ Fig. 11. Through comparison, it is found that the transmission error is reduced from 1.847 µ m of the original tooth number scheme to 0.292 µ m, a decrease of 84.2%; It can be clearly found that the tooth surface load of the original tooth number scheme is unevenly distributed along the tooth width direction, and there is a certain eccentric load, with the maximum load of 1335.547n/mm2. The tooth surface load of this tooth number scheme is evenly distributed along the tooth width direction, and there is basically no eccentric load, with the maximum load of 998.281n/mm2, which is reduced by 25.3%.