In the automotive industry, the reduction of noise, especially that from the powertrain system, has become a key focus for manufacturers and consumers alike. Gear noise, in particular, is a significant source of noise in the transmission system. This paper aims to explore the optimization of rear axle gear noise in a specific vehicle model, based on the analysis and findings presented in the provided document.
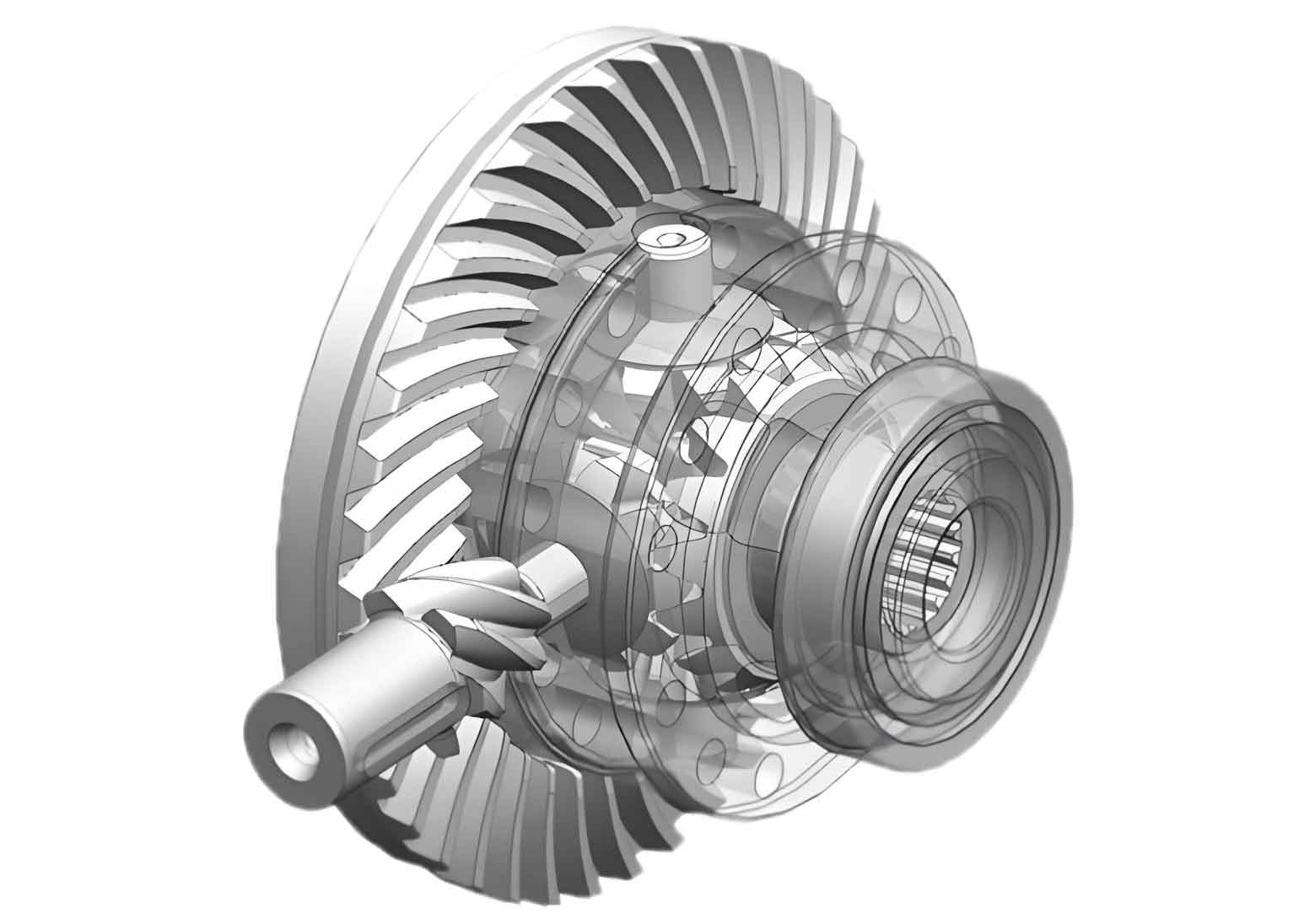
Introduction
The noise generated by the gear pair, particularly its howling, is a major source of noise in the transmission system. Researchers and technicians have conducted in-depth studies to reduce gear howling. For example, Qian Wangtao analyzed the generation mechanism of rear axle noise and established an acoustic simulation analysis model for the rear axle. Luo Wenxin studied the coupled vibration characteristics of the transmission shaft – rear axle assembly system and established a simulation analysis model based on ADAMS. Wang Bingshan successfully reduced the gear howling noise in the third gear of the gearbox by optimizing the gear overlap degree using the MASTA software. Xu Haijun et al. used the MASTA software to establish a dynamic response analysis model for the transmission shaft – rear axle, and optimized the gear parameters based on the simulation analysis results to reduce the gear transmission error and howling noise.
In a rear-wheel-drive vehicle, the power is transmitted from the engine to the rear axle through the clutch, gearbox, and transmission shaft. During the power transmission process, the gears are the most commonly used components. However, due to the vibration excitation from the engine and tires, as well as the deformation of the housing, bearings, and gears themselves, the gears may deviate from the optimal meshing area. This can lead to unstable rotation of the gears, increased vibration amplitude, and the generation of uncomfortable medium and high-frequency howling noise.
Analysis of Rear Axle Noise Transmission Path
The rear axle noise is transmitted through a complex path. As shown in Figure 1, the power from the engine is transmitted to the rear axle through the clutch, gearbox, transmission shaft, and intermediate support. The gear vibration in the rear axle is amplified during the meshing process under load. This vibration is then transmitted to the vehicle body through the various connecting components, eventually reaching the interior of the vehicle, resulting in audible howling noise.
Power Transmission System Response Analysis
A complete power transmission system dynamic response analysis model was established in MASTA, including the engine assembly, clutch, transmission, transmission shaft, rear axle, suspension system, and wheels, as shown in Figure 2. The input parameters for the MASTA analysis model are listed in Table 1. When the vehicle is driving at 90 – 100 km/h, the corresponding engine speed is 2850 – 3200 rpm. During the acceleration process, the main tooth bearing exhibits a vibration displacement response peak in the frequency range of 540 Hz – 640 Hz, as shown in Figure 3. This frequency coincides with the gear noise frequency of the vehicle at 90 – 100 km/h. The amplitude of the vibration acceleration of the main tooth bearing can be used to characterize the gear noise level, as the vibration displacement response frequency of the main tooth bearing is consistent in the MASTA model with different gear parameters, but the amplitude slightly varies.
Through different optimization scheme combinations, it is concluded that the main factors affecting the amplitude of the vibration acceleration of the main tooth bearing include insufficient support stiffness of the main reducer housing, differential housing, and bearings, excessive design of the gear transmission error, and the presence of resonance phenomena in the transmission path.
Design Optimization
To address the identified issues, several design optimizations were carried out:
- Shell Stiffness Optimization: The reinforcing ribs on the main reducer housing were re-optimized. The thickness of the reinforcing ribs was increased from 5 mm to 6 mm, and the direction of the ribs was rearranged from horizontal transverse to radial around the center of the main gear. Additionally, a horizontal reinforcing rib was added. The stiffness of the housing before and after the optimization was analyzed using the ABAQUS software, and the results are shown in Table 2 and Figure 5. The stiffness of the reduction housing increased by 36%, and that of the differential housing increased by 21%.
- Bearing Stiffness Optimization: The structure of the bearing rollers, raceways, and flanges was optimized to enhance the axial and radial stiffness of the bearings. The radial stiffness before and after the optimization is compared in Figure 6. By increasing the axial preload of the bearings, the movement of the gears during operation was reduced.
- Gear Parameter Optimization: The gear contact area was optimized by adjusting the relevant gear parameters, reducing the gear transmission error. After optimization, the contact area of the gears increased by 40% compared to before, as shown in Figure 7. The designed transmission error of the gears decreased by 50%, as shown in Figure 8.
- Cross Tie Rod Structure Optimization: The modal analysis of the cross tie rod was conducted using the ABAQUS software. It was found that the bending mode in the Z direction of the rear axle cross tie rod was close to the bending mode in the X direction of the rear axle, which could lead to resonance and amplify the rear axle gear noise transmitted to the vehicle body. To avoid this, the cross-section of the cross tie rod was optimized from U-shaped to O-shaped, so that the modes of the cross tie rod and the rear axle were staggered. The modal distributions before and after the optimization are shown in Table 3.
Analysis Results Before and After Optimization
Using the established MASTA power transmission system analysis model, the vibration acceleration amplitude of the main tooth bearing and the gear transmission error were simulated and analyzed before and after the optimization. The peak vibration acceleration decreased from 168 m/s² to 24 m/s², a reduction of 85.7%, as shown in Figure 9. The gear transmission error decreased from 126 μRad to 74 μRad, a reduction of 41.3%, as shown in Figure 10.
Real Vehicle Testing
Based on the optimization results, samples were made and real vehicle tests were conducted. Acoustic microphones were arranged in the rear row of the vehicle, and the LMS equipment was used to collect the interior noise of the vehicle under the full throttle acceleration condition with the engine speed ranging from 1500 to 4000 r/min. The rear axle gear order noise was extracted using the Test.Lab software.
The test results showed that before the optimization, the vehicle had a noise peak at the engine speed of 3120 r/min, with a maximum decibel value of 67.64 dB(A), exceeding the target line. After the optimization, no noise peak appeared in the entire speed range, and the overall noise was below the target line, achieving the optimization effect, as shown in Figure 11.
Conclusion
Based on the analysis of the rear axle noise transmission path, a complete MASTA simulation analysis model of the power transmission system was established. Through a large number of simulation analysis results, several key factors affecting the rear axle noise were identified. By optimizing the structure of key components, the rear axle noise problem was significantly improved, providing a reference for the solution of related NVH issues.
In the future, further research could focus on exploring more advanced materials and manufacturing processes to further enhance the stiffness and durability of the rear axle components. Additionally, the development of more precise simulation models and testing methods could help in more accurately predicting and addressing noise issues. Continual innovation and optimization in this area will contribute to improving the overall driving experience and comfort of vehicles.
Here is a summary of the key points in a table format:
Optimization Aspect | Details |
---|---|
Shell Stiffness Optimization | Increased reinforcing rib thickness from 5 mm to 6 mm, changed rib direction, and added a horizontal rib. Stiffness of the reduction housing increased by 36%, and that of the differential housing increased by 21%. |
Bearing Stiffness Optimization | Optimized the structure of bearing rollers, raceways, and flanges to enhance axial and radial stiffness. Increased axial preload to reduce gear movement. |
Gear Parameter Optimization | Adjusted gear parameters to increase the contact area by 40% and reduce the transmission error by 50%. |
Cross Tie Rod Structure Optimization | Changed the cross-section of the cross tie rod from U-shaped to O-shaped to avoid resonance with the rear axle. |
Overall, the optimization of the rear axle gear noise in this vehicle model demonstrates the importance of a systematic approach in addressing NVH issues in automotive design. By identifying the key factors contributing to noise and implementing targeted optimizations, significant improvements can be achieved in vehicle performance and comfort.