For the set optimization objective, that is, the minimum peak peak te optimization of transmission error, it is not known which modification parameters have a great influence on this objective before, nor is it sure about the selection trend of modification parameters. Therefore, first set the approximate value range of the optimization parameters, and then narrow the range to find the optimal value and the most important influence parameters after the first optimization.
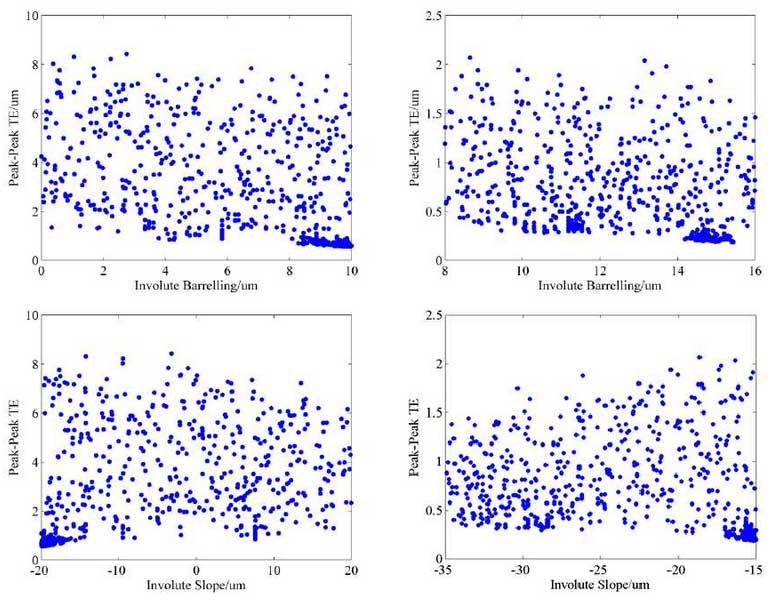
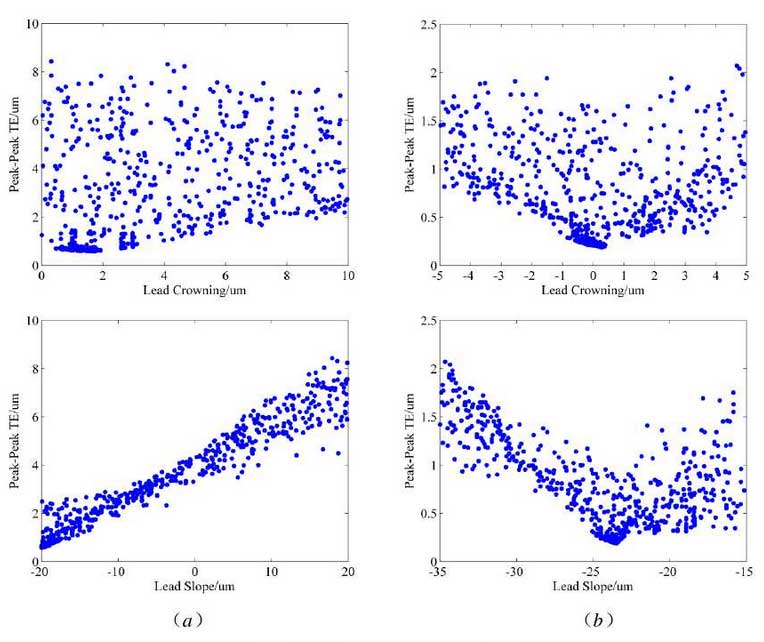
Figure 1 (a) shows the first optimization result. It can be seen that the tooth deflection modification has the greatest influence on the transmission error, and its optimal value tends to be – 20um. Because the tooth deflection modification is large, the influence of the tooth deflection modification on the middle drum is very small, so the tooth deflection modification is almost unnecessary, and its value tends to be close to 0; the modification of tooth height direction can be seen from its population is relatively scattered, which shows that compared with the modification of tooth direction, its effect is not significant, but the optimal values of – 20um (deflection) and 10um (middle drum) are still given in the optimization results.
Figure 1 (b) shows the second optimization result. It can be seen that the optimal value of tooth deflection is – 23um, and the tooth middle drum can not be modified. The tooth height deflection is – 15um, and the tooth high and middle drums are 14.5um. In fact, the effect of tooth height modification is not significant.
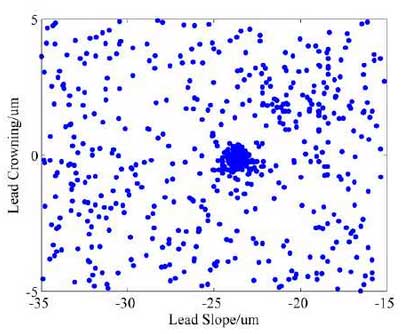
Figure 2 compares the two modification parameters, and it can be seen that the population distribution in the optimization process of genetic algorithm, and then the selection basically covers the sample space, while the final winning population is concentrated in the middle dense place, which shows that the optimization effect is obvious.
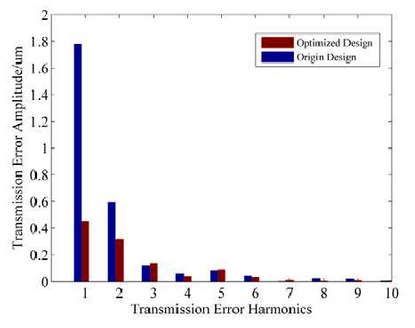
Fig. 3 shows the first 10 harmonic amplitudes of the transmission errors of the front and rear gears under a given load, which are usually the most concerned with the first three orders. It can be seen from the figure that after the first two steps of amplitude optimization, the amplitude is greatly reduced, especially the first step is reduced from 1.8 to about 0.4.
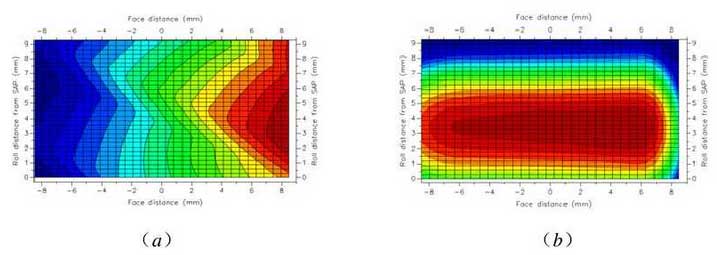
Figure 4 compares the contact spots of the gears before and after optimization, and it can be seen clearly that the gears are severely biased due to the meshing deflection before optimization, resulting in large transmission error. After the modification, especially after the correction of the tooth deviation, the contact is good and the transmission error is reduced. This also explains why the results are most sensitive to tooth deflection in the optimization process.
It should be specially pointed out that the shape modification usually requires the simultaneous modification of the active and passive teeth. Here, as an example, only the modification of the active teeth is considered, so the value is relatively large.
Through the above methods, all gears are optimized to find the best modification way and amount. Because the working condition of gearbox is changing, that is to say, the gear load is not a fixed value. In the optimization process, according to the load spectrum time of each working condition, different weight is given to evaluate the results, then a compromise optimization value can be obtained. Limited in space, only the first harmonic amplitude comparison of transmission error before and after the second gear optimization is given here, as shown in Figure 5. The optimized transmission error is smaller than that of the original design from the reverse driving condition to the driving condition. It shows that the optimization method is effective.
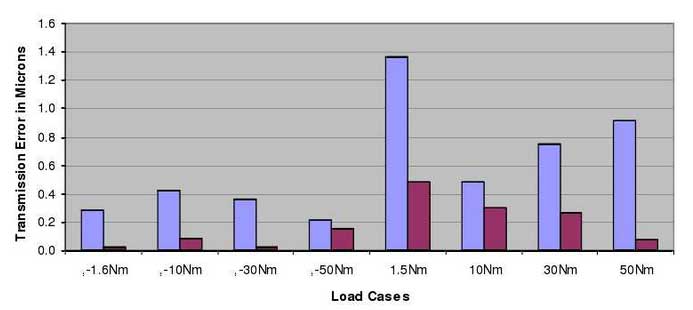