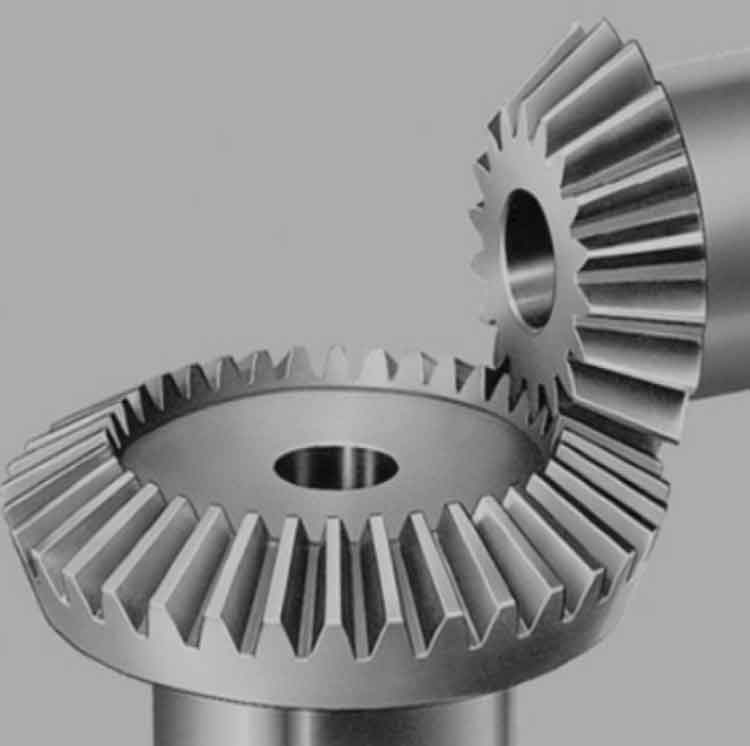
Advancements in gear design have led to significant improvements in the performance, efficiency, and reliability of straight bevel gears. As technology and engineering practices evolve, engineers have implemented various optimizations and innovations to enhance the design and manufacturing of these gears. Here are some notable advancements in straight bevel gear design:
1. Computer-Aided Design (CAD) and Simulation:
- CAD software allows engineers to create detailed 3D models of gears, enabling precise and accurate gear design.
- Simulation tools help predict gear performance, tooth contact patterns, and stress distribution, facilitating optimization before physical prototyping.
2. Finite Element Analysis (FEA):
- FEA is used to simulate the behavior of gears under various loads and conditions, providing insights into stress concentrations, deformation, and potential failure points.
- FEA aids in identifying weak areas and allows for material and design adjustments to enhance gear strength.
3. Tooth Profile Optimization:
- Advanced tooth profile optimization techniques are employed to achieve smoother tooth engagement and reduce noise and vibration during operation.
- Profile modifications such as crowning and tip relief are used to improve gear meshing characteristics.
4. Material Selection and Heat Treatment:
- Advancements in metallurgy have led to the development of high-strength, wear-resistant materials for gears.
- Precise heat treatment processes ensure uniform hardness distribution, enhancing gear strength and wear resistance.
5. Gear Manufacturing Technology:
- Modern CNC machining and gear cutting processes have improved the accuracy and consistency of straight bevel gears.
- Advanced gear grinding and honing techniques enhance gear surface finish and reduce friction.
6. Surface Coatings and Lubrication:
- Advanced surface coatings, such as DLC (diamond-like carbon) coatings, improve gear surface hardness and reduce friction, enhancing gear durability.
- Lubrication advancements help reduce wear and increase efficiency by providing optimal lubrication under varying operating conditions.
7. Noise Reduction:
- Engineers have developed sophisticated noise analysis and reduction methods to design quieter gear systems.
- Noise-minimizing features, such as modified tooth profiles and gear tooth phasing, help reduce gear noise during operation.
8. Gear Testing and Quality Control:
- Advanced gear testing methods, including noise testing, contact pattern analysis, and dynamic testing, ensure gear compliance with stringent quality standards.
- Quality control measures at each stage of the manufacturing process ensure consistent gear performance.
9. Integration with Digital Twins and Industry 4.0:
- Straight bevel gear design is integrated with digital twin technology, allowing for real-time monitoring and predictive maintenance of gear systems.
- Industry 4.0 principles enable data-driven optimization of gear design, production processes, and performance analysis.
These advancements in straight bevel gear design have led to gears with higher efficiency, reduced noise levels, improved durability, and greater reliability. As engineering techniques continue to evolve, further optimizations will likely continue to refine the design and performance of straight bevel gears for a wide range of applications in various industries.