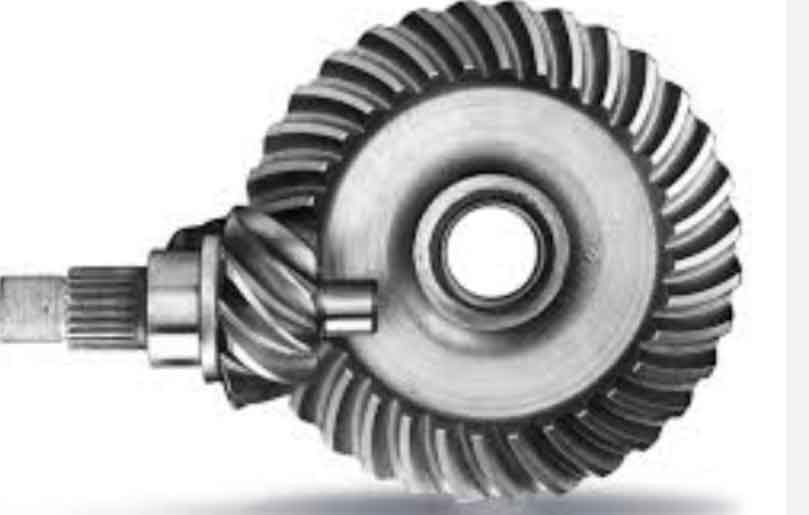
Optimizing gear geometry is essential for perfecting hypoid gear meshing, ensuring efficient power transmission, reducing noise, and increasing the overall performance and longevity of the gear system. Here are some tips to help optimize gear geometry and achieve optimal hypoid gear meshing:
- Proper Selection of Hypoid Gear Parameters: The first step in optimizing gear geometry is selecting appropriate gear parameters, including the number of teeth, pressure angle, pitch, and module, based on the specific application requirements and load conditions.
- Gear Profile Modification: Implement profile modifications, such as crowning and tip relief, to improve contact patterns and reduce edge contact stresses. These modifications help distribute the load more evenly across the gear teeth and minimize gear meshing noise.
- Contact Ratio Enhancement: Aim for a higher contact ratio in gear design to achieve smoother and quieter gear meshing. Increasing the contact ratio allows multiple gear teeth to be engaged simultaneously, reducing localized stress and wear.
- Mesh Alignment and Preload Optimization: Precise alignment and appropriate preload between the mating gears are critical for achieving optimal gear meshing. Proper alignment minimizes misalignment-induced losses and ensures uniform load distribution.
- Gear Tooth Profile Optimization: Utilize advanced gear design software and simulation tools to optimize the tooth profile. This includes adjusting parameters such as profile shift and lead angle to achieve the desired gear performance.
- Crowned Gear Tooth: Designing crowned gear tooth profiles can enhance contact conditions and load sharing, leading to improved gear meshing efficiency and noise reduction.
- Gear Pair Microgeometry Analysis: Conduct microgeometry analysis of the gear pair, such as tooth flank modifications and bearing contact pattern adjustments, to improve gear meshing and minimize transmission errors.
- Tooth Contact Analysis: Perform tooth contact analysis to ensure proper tooth contact during gear meshing. This analysis helps identify any potential interference and guide modifications to achieve desired contact patterns.
- Optimized Gear Tolerance and Manufacturing Process: Set appropriate gear tolerances and consider the manufacturing process capabilities to ensure the designed gear geometry is manufacturable and aligns with the desired performance.
- Material Selection and Heat Treatment: Choose high-quality gear materials with suitable hardness and wear resistance to withstand the anticipated loads and stresses. Heat treatment can further enhance the material properties for improved gear performance.
- Lubrication and Cooling: Optimize the gear lubrication system to ensure proper lubricant flow and cooling during operation, reducing friction and preventing overheating.
- Noise and Vibration Analysis: Conduct noise and vibration analysis of the gear system to identify potential noise sources and vibration issues. This analysis will help refine the gear geometry and design to reduce noise and vibrations.
- Testing and Validation: Perform thorough testing and validation of the gear system under real-world conditions to verify the gear meshing performance and durability.
By following these tips and leveraging advanced design and simulation tools, engineers can optimize hypoid gear geometry to achieve smooth, efficient, and reliable gear meshing, resulting in improved overall gear system performance and durability.