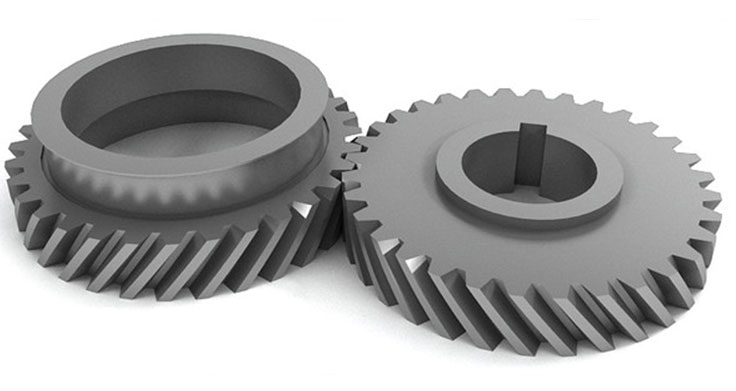
Optimizing gear meshing is crucial for achieving maximum efficiency with helical gears. Proper gear meshing ensures smooth operation, reduces energy losses, and minimizes wear, resulting in improved overall gear system efficiency. Here are some strategies to optimize gear meshing and maximize efficiency with helical gears:
1. Accurate Gear Design:
- Start with accurate gear design using advanced software tools to ensure precise tooth profiles, helix angles, and gear parameters. Optimize the gear design based on the specific application requirements and load conditions.
2. Tooth Profile Modification:
- Implement tooth profile modifications such as crowning, tip relief, and lead correction to improve tooth contact patterns and load distribution. These modifications reduce localized stresses and minimize noise during gear meshing.
3. Proper Helix Angle Selection:
- Select an appropriate helix angle for the helical gears based on the application requirements. The helix angle affects the degree of engagement during gear meshing and influences the gear system’s efficiency.
4. Gear Material and Heat Treatment:
- Choose high-quality gear materials with suitable hardness and wear resistance. Apply the right heat treatment processes to enhance material properties, ensuring durability and minimizing friction during meshing.
5. Lubrication and Lubricant Selection:
- Proper lubrication is essential for minimizing friction and wear during gear meshing. Use high-quality lubricants suitable for the application and operating conditions to reduce energy losses and increase efficiency.
6. Gear Tooth Surface Finishing:
- Ensure smooth and precise tooth surface finishing to minimize friction and improve meshing efficiency. Gear grinding or honing can achieve high-quality tooth surfaces.
7. Gear Alignment and Preload:
- Properly align the gears and apply the appropriate preload to optimize gear meshing. Precise alignment and preload help distribute loads evenly, reducing wear and enhancing efficiency.
8. Minimize Backlash:
- Minimize backlash between gear teeth to prevent wasted motion and improve positional accuracy in the gear system.
9. Gear Manufacturing Tolerances:
- Tight manufacturing tolerances help ensure accurate gear dimensions and meshing characteristics. Minimize deviations to optimize gear performance.
10. Noise Reduction Techniques:
- Employ noise reduction techniques such as vibration dampening or adding noise-absorbing materials to reduce gear meshing noise. Quieter gear operation can indicate more efficient power transmission.
11. Gearbox Design Optimization:
- Optimize the entire gearbox design to minimize energy losses in bearings, seals, and other components that can affect overall efficiency.
12. Gear Simulation and Testing:
- Use gear simulation and testing to validate the gear design and optimize its performance before implementation. Real-world testing can identify areas for improvement and ensure maximum efficiency.
By implementing these strategies, engineers can optimize gear meshing and maximize the efficiency of helical gear systems. Improving gear meshing efficiency leads to reduced power losses, longer gear life, and enhanced performance, making helical gears an excellent choice for a wide range of applications where efficiency is critical.