Optimizing the performance of helical gear through advanced material science involves selecting and processing materials in a way that enhances the gear’s operational efficiency, durability, and lifespan. This optimization is crucial for applications that demand high performance under extreme conditions, such as in aerospace, automotive, and industrial machinery. Advances in material science have led to the development of materials and treatments that significantly improve the properties of helical gear. Here’s an overview of key considerations and innovations:
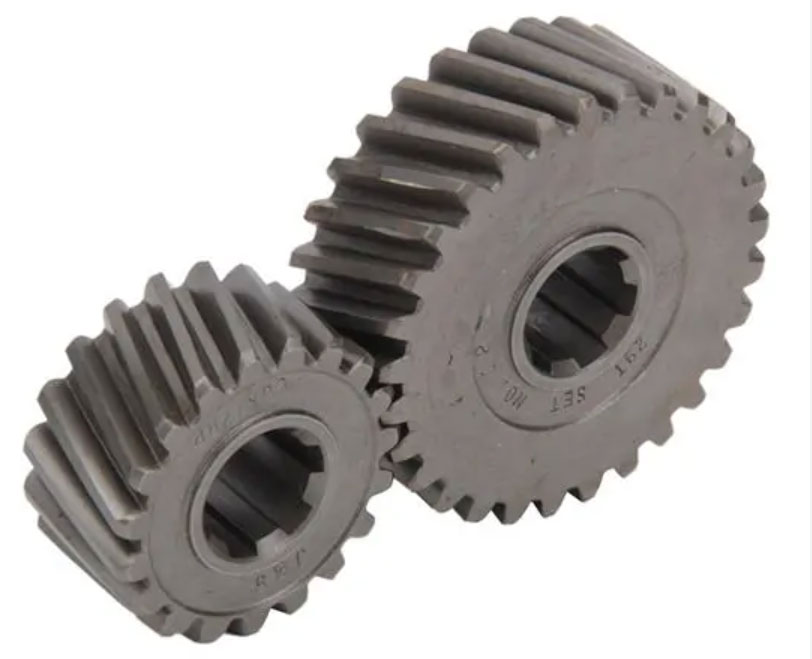
Advanced Materials for Helical Gear
- High-Performance Steels: Alloy steels containing elements like nickel, chromium, molybdenum, and vanadium offer superior strength, toughness, and resistance to wear and fatigue. These materials are ideal for high-load and high-speed applications.
- Case-Hardened Steels: Through case hardening processes such as carburizing and nitriding, the surface hardness of the helical gear is significantly increased while maintaining a tough and ductile core. This enhances the helical gear’s resistance to surface wear and pitting.
- Stainless Steels: For applications requiring corrosion resistance, such as in marine or chemical environments, stainless steels are preferred. They provide excellent durability and maintain performance over time in harsh conditions.
- Non-Metallic Materials: Polymers and composite materials are increasingly used for lightweight and low-noise helical gear applications. Materials like nylon, acetal, and carbon fiber-reinforced polymers offer good wear resistance and can be used in applications where weight and noise reduction are critical.
- Powder Metallurgy Gears: Helical gear manufactured using powder metallurgy can be made from materials that are difficult to process by conventional means. This method allows for the creation of helical gear with unique material properties, such as gradient hardness or tailored porosity for lubrication.
Material Treatments and Coatings
- Surface Coatings: Thin film coatings, such as diamond-like carbon (DLC) and titanium nitride (TiN), can significantly reduce friction and wear, leading to longer helical gear life and higher efficiency. These coatings are especially useful in applications where lubrication is limited or where extreme conditions prevail.
- Thermal Treatments: Heat treatments, including induction hardening and cryogenic treatments, can refine the microstructure of helical gear materials, improving their hardness and resistance to wear. Cryogenic treatments, in particular, enhance the dimensional stability and stress resistance of the helical gear.
- Chemical Treatments: Techniques such as phosphating and boronizing can improve the surface properties of helical gear, enhancing their resistance to corrosion and wear.
Considerations for Material Selection and Treatment
- Application Requirements: The operating environment, load conditions, and performance expectations dictate the selection of materials and treatments. High-speed or high-load applications may require different materials or treatments than those needed for corrosion resistance or noise reduction.
- Manufacturability: The chosen material and its treatment must be compatible with the manufacturing process. Some treatments may require specific equipment or may introduce constraints on the design or fabrication of the helical gear.
- Cost-Effectiveness: While advanced materials and treatments can significantly improve performance, they often come at a higher cost. A balance must be struck between the performance benefits and the overall cost impact on the project.
- Sustainability: Environmental considerations are increasingly important in material selection. Materials that are recyclable or that have a lower environmental impact over their lifecycle are preferred when possible.
Optimizing helical gear performance through advanced material science not only enhances the operational capabilities of the helical gear but also contributes to the overall efficiency and reliability of the machinery in which they are used. Continuous advancements in material science offer new opportunities for innovation in helical gear design and application.