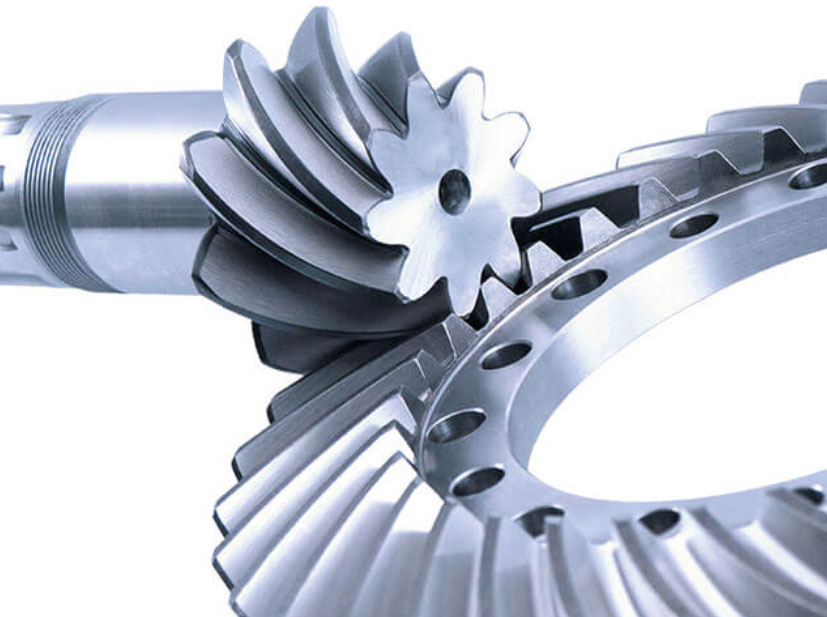
Optimizing spiral bevel gear pairings is essential to achieve smooth operation, minimize noise and vibration, and ensure the longevity of the gears. Several factors need to be considered to achieve the desired level of smoothness in gear operation. Here are some key strategies for optimizing spiral bevel gear pairings for smooth operation:
1. Precision Manufacturing:
- Ensure that both the pinion and gear are manufactured with high precision to maintain accurate tooth profiles and minimize tooth deviations.
- Precise gear manufacturing reduces the chances of misalignment and ensures smooth meshing.
2. Proper Tooth Profile Design:
- Optimize the tooth profile design of both the pinion and gear to achieve favorable contact patterns and reduce edge loading.
- A well-designed tooth profile promotes even distribution of contact stresses and improves gear engagement.
3. Gear Geometry and Tooth Alignment:
- Achieve proper gear geometry and alignment by controlling the gear’s backlash, face contact, and tooth alignment.
- Proper gear mesh alignment reduces the risk of localized high stresses and improves load distribution.
4. Lubrication and Surface Finish:
- Use high-quality lubricants and ensure adequate lubrication of the gear pair to reduce friction and wear.
- Optimal surface finish on gear teeth helps improve lubricant retention and enhances smooth operation.
5. Bearing Selection and Preload:
- Properly select bearings that can handle the applied loads and ensure they are preloaded to minimize gear deflections and misalignments.
6. Gear Hardening and Heat Treatment:
- Apply appropriate gear hardening and heat treatment techniques to enhance gear surface hardness and wear resistance.
- Proper heat treatment helps prevent premature wear and tooth damage, contributing to smoother operation.
7. Load Distribution:
- Optimize the gear pairing’s load distribution to ensure uniform distribution of forces along the gear teeth during operation.
- Balanced loading reduces the risk of localized wear and ensures smooth transmission of power.
8. Noise Reduction Measures:
- Implement noise reduction measures, such as helix angle optimization and flank modifications, to reduce gear noise during meshing.
- Proper gear design can significantly contribute to reducing gear noise and improving smoothness.
9. Elimination of Vibrations:
- Identify and eliminate sources of vibrations in the gear system that may lead to gear noise and uneven operation.
- Proper dampening and isolation techniques can be employed to mitigate vibrations.
10. Continuous Improvement and Testing:
- Regularly monitor gear performance and conduct thorough testing to identify areas for improvement.
- Continuous refinement of gear design and manufacturing processes leads to smoother gear operation over time.
By implementing these optimization strategies and paying close attention to gear design, manufacturing, and operating conditions, engineers can achieve smooth and efficient operation in spiral bevel gear pairings, making them suitable for various applications in automotive, aerospace, industrial machinery, and other industries.