Optimizing spur gears design for maximum load capacity and lifespan involves a comprehensive approach that addresses material selection, geometric design, surface treatment, and maintenance practices. Spur gears, characterized by their straight teeth and parallel axes, are critical components in various machinery for transmitting power and motion efficiently. Enhancing their load capacity and lifespan not only improves the performance of the machinery but also reduces the need for frequent replacements and maintenance, thereby lowering operational costs. Here’s how to optimize spur gears design for these objectives.
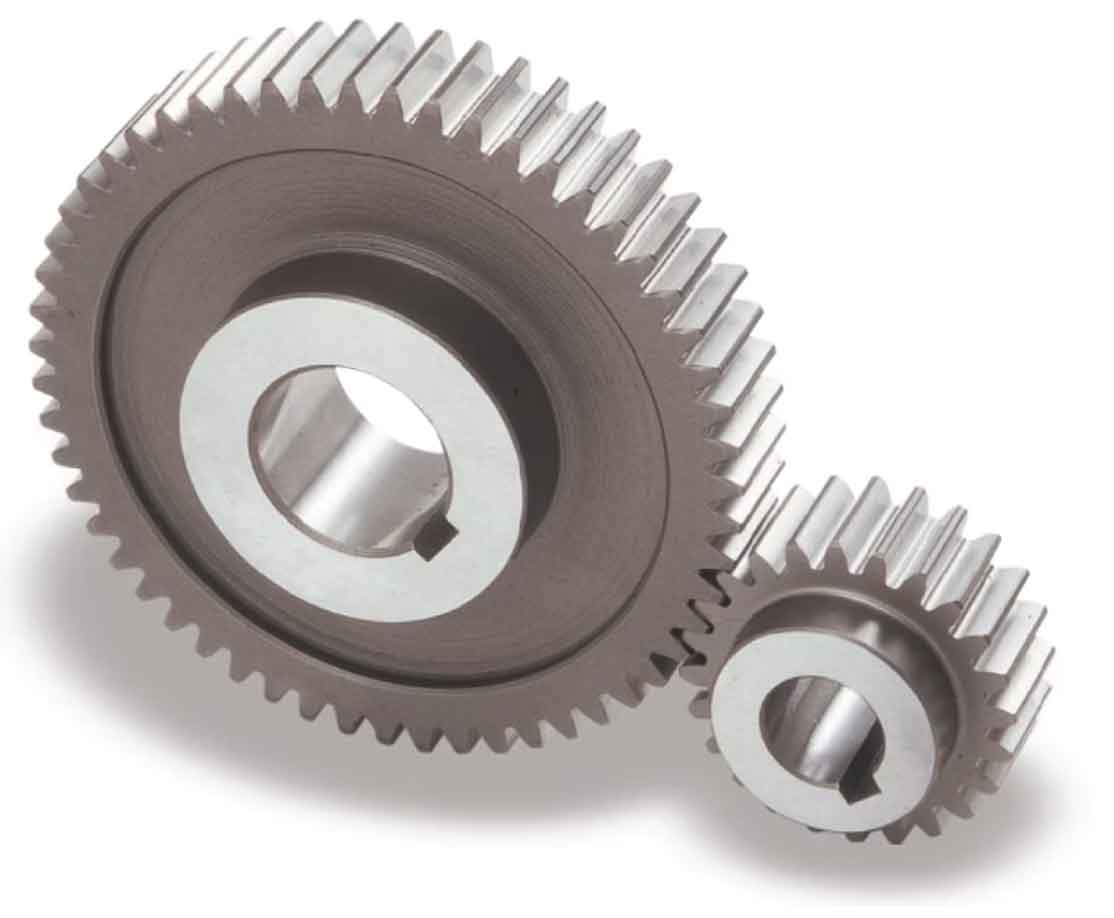
Material Selection
High-Quality Materials: The choice of material significantly impacts the strength, durability, and wear resistance of spur gears. High-quality materials like steel alloys, which offer superior hardness and toughness, are often preferred. For applications requiring lightweight spur gears, advanced composites or aluminum alloys can provide an excellent strength-to-weight ratio.
Heat Treatment: Processes like case hardening, nitriding, or carburizing can significantly improve the surface hardness and fatigue strength of spur gears, enhancing their load capacity and resistance to wear.
Geometric Design
Tooth Profile Optimization: Modifying the tooth profile, such as using involute profiles, can improve the distribution of stress across the tooth surface, reducing the likelihood of failure under heavy loads.
Gear Ratios and Size: Carefully selecting spur gears ratios and dimensions based on the application’s specific load requirements can optimize performance. Larger spur gears can distribute the load over a larger surface area, but space constraints must be considered.
Addendum and Dedendum Modifications: Adjusting the height of the tooth (addendum) and the depth of the space between teeth (dedendum) can affect spur gears strength and durability. A larger dedendum can provide more room for stress distribution.
Surface Treatment and Finishing
Surface Finishing Techniques: Smooth surface finishes reduce friction and wear, extending spur gears lifespan. Techniques such as grinding, polishing, or honing can achieve high-quality finishes.
Coatings: Applying coatings like DLC (diamond-like carbon) or TiN (titanium nitride) can significantly increase surface hardness and reduce friction, further enhancing spur gears load capacity and durability.
Maintenance Practices
Lubrication: Proper lubrication minimizes friction and wear, crucial for maintaining spur gears integrity over time. Using the right type and grade of lubricant based on the operating environment and load conditions is essential.
Regular Inspections: Scheduled inspections and maintenance can detect and address issues before they lead to spur gears failure. This includes checking for wear, misalignment, and lubricant degradation.
Advanced Design and Manufacturing Techniques
Finite Element Analysis (FEA): Using FEA tools during the design phase can predict stress distribution and potential failure points under various load conditions, allowing for design optimization before manufacturing.
Additive Manufacturing: 3D printing technologies enable the production of spur gears with complex geometries that were previously difficult or impossible to achieve. This can include internal cooling channels or lightweight structures without compromising strength.
Conclusion
Optimizing the design of spur gears for maximum load capacity and lifespan is a multifaceted process that involves careful consideration of materials, geometry, surface treatments, and maintenance. By employing a holistic approach that integrates advanced materials science, precision engineering, and regular upkeep, it’s possible to significantly enhance the performance and reliability of spur gears in any application. This not only ensures the efficient operation of machinery but also contributes to sustainability by reducing waste and energy consumption.