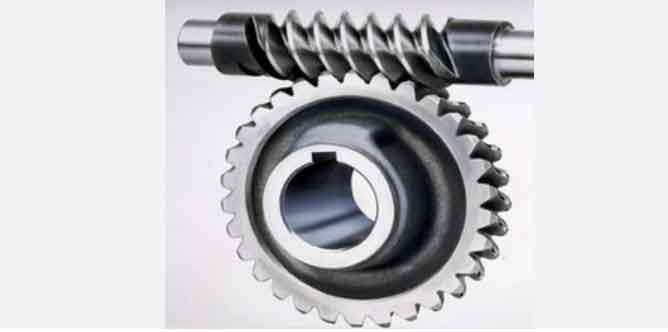
Optimizing worm gear systems for energy conservation is crucial to improve overall efficiency and reduce power losses. Here are some key considerations and strategies to enhance the energy efficiency of worm gear systems:
1. Gear Pair Selection:
Choose the gear pair with appropriate lead angles, materials, and tooth profiles to optimize efficiency. Select materials with low friction coefficients and high wear resistance to reduce power losses due to friction. The gear pair should also be properly matched in terms of size, load capacity, and speed requirements to maximize efficiency.
2. Lubrication and Lubricant Selection:
Proper lubrication is essential to minimize friction, wear, and power losses in worm gear systems. Select high-quality lubricants with suitable viscosity and additives to reduce friction and provide effective lubrication. Regularly monitor lubricant levels and maintain proper lubrication intervals to ensure optimal performance and minimize energy losses.
3. Gear Design Optimization:
Design the worm and worm wheel with optimized tooth profiles, gear geometry, and load distribution to minimize power losses. Utilize advanced design software and simulation tools to optimize the gear geometry and tooth engagement characteristics. This includes optimizing gear ratios, tooth profiles, and tooth surface contact to reduce friction and increase efficiency.
4. Reducing Backlash:
Minimize backlash in the worm gear system to enhance energy efficiency. Backlash leads to power losses and decreased system responsiveness. Implement techniques such as gear preloading, appropriate gear meshing clearances, and anti-backlash devices to minimize backlash and improve power transmission efficiency.
5. Material Selection and Surface Treatment:
Choose high-quality gear materials with low friction coefficients, high hardness, and excellent wear resistance. Proper heat treatment processes, such as carburizing and hardening, can enhance the surface hardness and reduce friction. Consider utilizing surface treatments like coatings or plating to further reduce friction and improve wear resistance.
6. Maintenance and Inspection:
Regular maintenance and inspection are crucial for maintaining optimal efficiency in worm gear systems. Implement a maintenance schedule to check for proper lubrication, inspect gear condition, and monitor any signs of wear or damage. Addressing any issues promptly can prevent energy losses due to inefficient operation or increased friction.
7. System Optimization:
Consider the overall system design and operation to maximize energy efficiency. Evaluate the power requirements, load distribution, and operating conditions to ensure the system is properly sized and optimized. This includes minimizing unnecessary speed reductions, optimizing motor sizing, and implementing energy-efficient control systems.
8. Continuous Monitoring and Improvement:
Implement a monitoring system to continuously assess the performance and energy consumption of the worm gear system. Monitor parameters such as temperature, power consumption, and efficiency to identify any deviations or opportunities for improvement. Regularly review and update the system based on the monitoring data to further enhance energy conservation.
By implementing these strategies, designers and operators can optimize the energy efficiency of worm gear systems, minimizing power losses, reducing energy consumption, and promoting sustainability in various industrial applications.