Worm gear production, a crucial aspect of mechanical engineering, involves the manufacturing of gears that exhibit a screw-like appearance. Worm gears are widely used for their ability to provide high reduction ratios and to transmit motion between non-parallel, non-intersecting shafts. Despite their advantages, the production of worm gears faces several challenges, including precision manufacturing, material selection, and wear resistance. Overcoming these challenges requires advanced techniques and technologies:
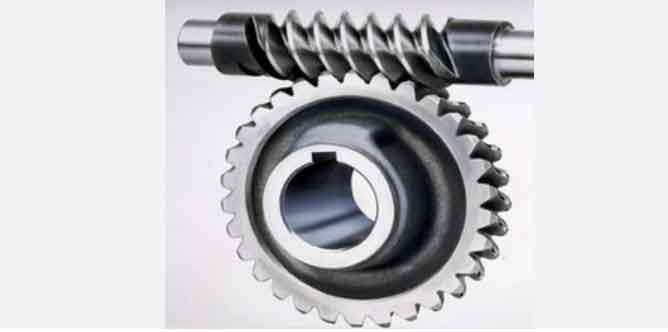
- Precision Manufacturing: The accuracy of worm gears is paramount for efficient operation and longevity. Advanced CNC (Computer Numerical Control) machining and gear hobbing techniques are employed to achieve high precision in the manufacturing process. CNC machines can be programmed to produce gears with tight tolerances, ensuring that each gear fits perfectly with its mate.
- Material Selection: The choice of material significantly impacts the performance and durability of worm gears. Materials like bronze, aluminum, and stainless steel are commonly used for the worm wheel, while the worm itself is often made of hardened steel to resist wear. Recent advancements have seen the introduction of composite materials and polymers for lighter applications, offering comparable strength with reduced weight.
- Surface Treatment and Hardening Processes: To enhance the wear resistance of worm gears, surface treatment techniques such as carburizing, nitriding, and induction hardening are applied. These processes increase the hardness of worm gear surfaces, making them more resistant to wear and extending their service life.
- Lubrication Systems: Proper lubrication is critical for reducing friction and wear in worm gears. Advanced lubrication systems and high-performance lubricants have been developed to provide consistent lubrication under varying conditions. These include synthetic oils and greases that offer better performance and longer life spans than conventional lubricants.
- 3D Printing and Additive Manufacturing: 3D printing technologies are revolutionizing the production of worm gears by allowing for complex geometries that are difficult or impossible to achieve with traditional manufacturing methods. Additive manufacturing enables the production of worm gears with integrated cooling channels or lightweight structures without compromising strength.
- Gear Design Software: Advanced software tools are available for the design and simulation of worm gears. These tools allow engineers to optimize gear geometry, material selection, and loading conditions before manufacturing begins. This reduces the risk of failure and ensures that worm gears perform as expected under real-world conditions.
- Quality Control and Inspection Technologies: Ensuring the quality of worm gears is critical for their performance. State-of-the-art inspection technologies, including coordinate measuring machines (CMMs) and gear metrology systems, are used to perform detailed inspections of gear geometry, surface finish, and alignment. These technologies enable manufacturers to detect and correct defects early in the production process.
By leveraging these advanced techniques and technologies, manufacturers can overcome the challenges associated with worm gear production, resulting in worm gears that offer high performance, reliability, and longevity. Continuous research and development in this field are essential for further advancements and for meeting the increasingly stringent demands of various industries, including automotive, aerospace, and robotics.