Hypoid gear has the advantages of large coincidence, strong tolerance, high meshing stability, and is suitable for large intersection angle, offset installation and so on. It is widely used in aviation, automobile, ship and other transmission systems. Compared with Gleason gears, Oricon gears have the advantages of high processing efficiency, strong bearing capacity and low noise. Because the machining of Oricon gear is a continuous indexing cutting process, the requirements of the coordinated movement among the structure of the cutter head, the direction of the installation position and the machining gear of the cutter head shaking table are very strict; At the same time, based on different reference datum, the cutter head and cutting parameters are different, which makes the tooth surface forming theory of Oricon hypoid gear more complex. In the existing research, the chip direction datum is usually used for tooth surface modeling, but there is almost no tooth surface modeling based on NS (neutral surface) normal datum. Therefore, it is necessary to study the derivation of tooth surface mathematical model under this datum.
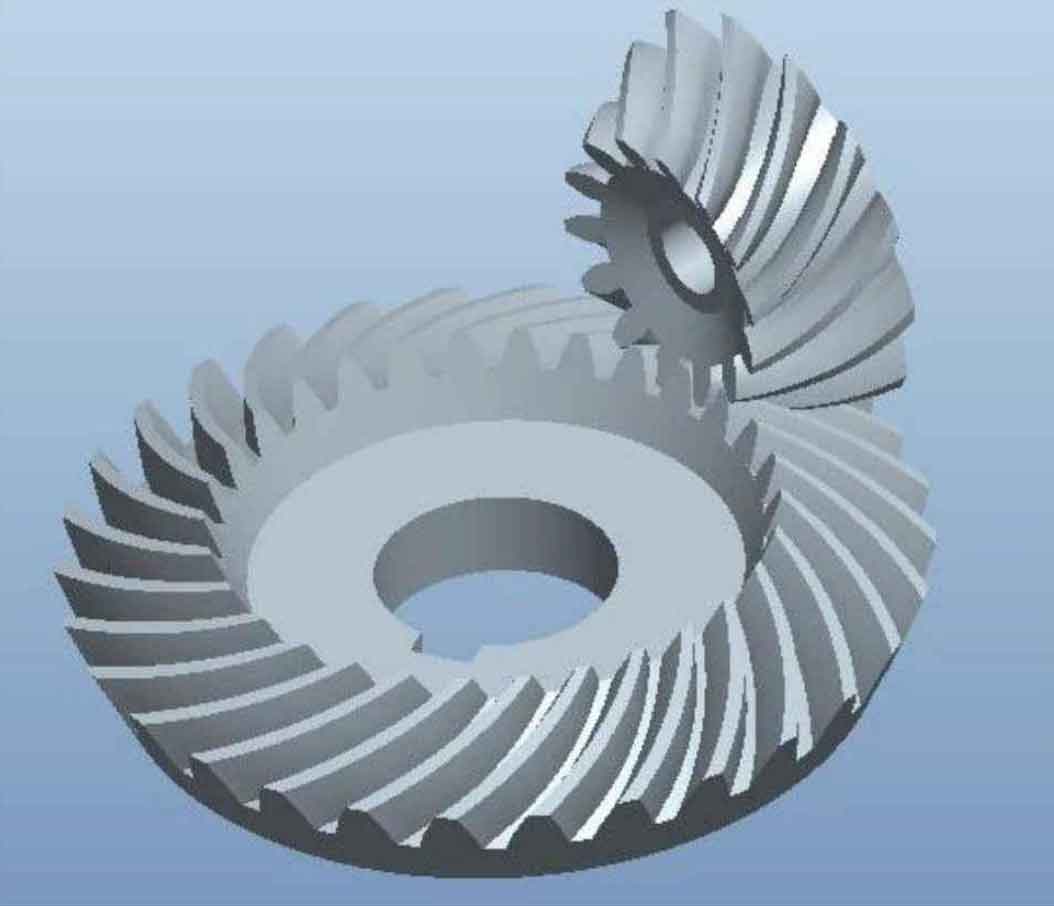
Relevant scholars at home and abroad have done some research on the tooth surface forming theory of hypoid gears. Litvin put forward the theory of local synthesis method, which laid the foundation for the related research of hypoid gears. Based on the traditional rocking table machine tool, fan systematically decomposes the Gleason spiroflex surface rolling method. Shih et al. Proposed a general modeling method for face milling and face hobbing of general hypoid gears. Fang Zongde et al. Used the conventional Gleason cutter head to deduce the mathematical equation of the spiral tooth surface. Guo Xiaodong et al. Obtained the tooth surface point set through the tooth surface measuring machine and established the inverse adjustment optimization gear model. Linxi carried out cutting simulation through CATIA and established the model of Gleason hypoid gear pair. Wang Xingxing and others built the wheel blank and cutter head entity based on the secondary development of AutoCAD, and modeled the cycloid hypoid gear by simulating the tool processing system.
On the basis of mathematical derivation, Jiang Yugang and Uranus established the mathematical equations of theoretical working tooth surface and tool tip arc segment surface of Gleason hypoid gear. Zhang Weiqing and Du Jinfu studied the discrete modeling of cycloid hypoid gear tooth surface based on the cutting direction benchmark. In these studies, the modeling of hypoid gears is mainly through simulation and mathematical derivation. Most studies focus on Gleason hypoid gears and use simplified tools for tooth surface modeling, while for the accurate modeling of Oricon hypoid gears, chip direction datum is used, and the definition of tool datum is rarely introduced. Therefore, based on the tool ns normal datum, starting from the geometric section and structure of the machining tool, the author analyzes the structure and installation position of the Oricon trihedral tool, and establishes the mathematical model of the cutter head including the arc segment of the tool tip; The machining coordinate system of the forming method big wheel and the generating method small wheel is established by the tool inclination half generating method, and the cutting path surface of the tool cutting edge in the blank coordinate system is obtained; According to the machining method of large and small wheels, the mathematical model of the tooth surface of large and small wheels is derived.
By comparing the tooth surface error with the theoretical 45 point tooth surface and comparing the actual contact mark calculated by the finite element method with the contact mark calculated by the kimos theoretical tooth contact analysis (TCA) and the tooth load contact analysis (LTCA), the correctness of the modeling of Oricon hypoid gear based on the tool NS normal datum is verified.
Starting from the actual machining of ollicon hypoid gear, the structure and position of the machining cutter head are studied, and the mathematical model of the cutter head based on the NS normal datum of the tool and the solid model of ollicon hypoid gear are established. The relevant verification is carried out, and a set of modeling process based on the NS datum is proposed. This method provides a new idea for the accurate modeling of hypoid gears, and provides a basis for the subsequent design and optimization of related gear surfaces, which has strong practical value.