The manufacturing process of helical gears involves several steps to ensure precision and durability. Let’s take a closer look at the key stages of helical gear manufacturing:
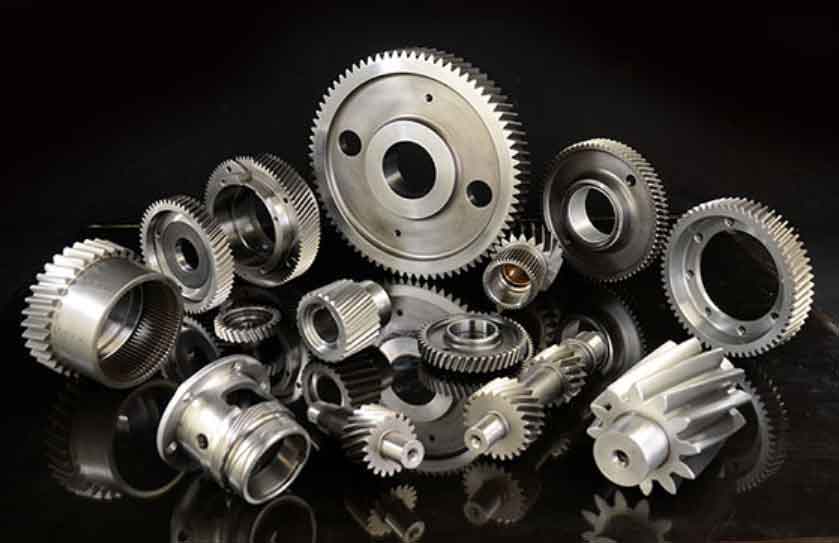
- Gear Design: The process begins with gear design, where engineers determine the gear specifications based on the application requirements. This involves calculating gear ratios, helix angles, tooth profiles, and other dimensions.
- Material Selection: The choice of material is crucial for the performance and durability of helical gears. Common materials used include alloy steels, carbon steels, and stainless steels. The selected material should have the necessary strength, wear resistance, and toughness to withstand the application’s demands.
- Blank Preparation: The gear blank, which is the initial piece of material before gear cutting, is prepared through processes like forging, casting, or machining. Forging and casting are often preferred for mass production due to their cost-effectiveness, while machining is used for smaller batches or custom gears.
- Gear Cutting: The primary method for cutting helical gears is gear hobbing. In this process, a gear hob, a cylindrical cutting tool with helical teeth, progressively cuts the teeth into the gear blank. The gear blank is rotated while the hob is fed axially to create the helical teeth.
- Heat Treatment: After gear cutting, the helical gear is heat-treated to enhance its hardness and improve its mechanical properties. Heat treatment processes such as carburizing, quenching, and tempering are commonly used to achieve the desired material characteristics.
- Finishing Operations: Additional finishing operations may be performed to improve gear surface smoothness and reduce tooth profile errors. These operations include grinding, lapping, and honing.
- Quality Inspection: Throughout the manufacturing process, quality inspection is conducted to ensure that the gear meets the required specifications and standards. Various inspection methods, including coordinate measuring machines (CMM), gear testers, and visual inspections, are used to verify the gear’s dimensional accuracy and surface quality.
- Surface Treatment and Coating: Depending on the application and material used, surface treatment or coating may be applied to further enhance wear resistance, corrosion resistance, or reduce friction.
- Assembly: Once the helical gears are manufactured, they are assembled into gearboxes or other gear systems, where they work in tandem with other components to transmit power and motion.
It’s worth noting that helical gears’ manufacturing process requires skilled technicians and advanced machinery to achieve the necessary precision and durability. Each step is carefully executed to ensure that the final product meets the required standards and delivers reliable performance in the intended application.