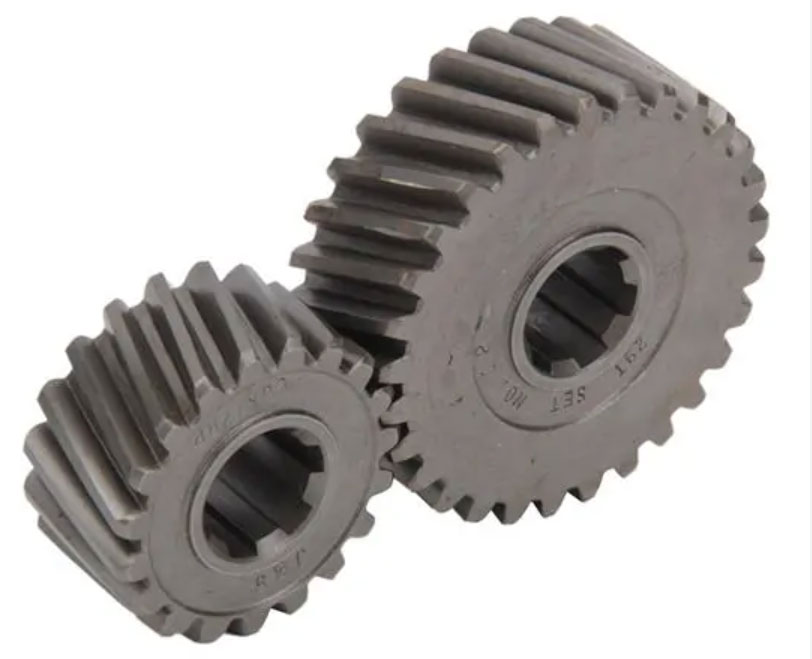
Precision engineering plays a crucial role in achieving optimal gear meshing with helical gears. Proper gear meshing is essential for ensuring smooth operation, minimizing noise, reducing wear, and maximizing the overall efficiency of the gear system. Here are some key aspects of precision engineering that help achieve optimal gear meshing with helical gears:
1. Gear Tooth Profile:
- Designing helical gears with accurate tooth profiles is critical. The tooth profile is typically an involute curve, but variations like trochoidal profiles may be used for specific applications.
- Ensuring precise tooth dimensions and involute shape helps achieve smooth and consistent meshing between mating gears.
2. Helix Angle and Lead:
- The helix angle determines the angle of the helical teeth with respect to the gear axis. It influences the smoothness of the gear engagement and noise levels.
- Achieving the correct helix angle and lead ensures that the gears mesh correctly, maintaining constant contact along the tooth surface during rotation.
3. Tooth Alignment and Center Distance:
- The accurate alignment of the gear teeth is vital for proper meshing. Any misalignment can lead to noise, vibration, and premature wear.
- The center distance between the mating gears must also be precisely controlled to achieve the desired gear meshing characteristics.
4. Surface Finish and Hardness:
- High-quality surface finish on the gear teeth is essential to reduce friction and wear during meshing.
- Proper heat treatment and hardness control of the gear materials ensure optimal tooth strength and wear resistance.
5. Tolerance Control:
- Tight tolerance control during gear manufacturing helps ensure uniformity and consistency in tooth dimensions and gear geometry.
- Careful inspection and measurement at critical stages of production help maintain the required precision.
6. Lubrication and Cooling:
- Proper lubrication and cooling of the gear system are crucial for achieving smooth gear meshing and reducing friction and heat generation.
- Adequate lubrication helps extend the life of the gears and ensures efficient power transmission.
7. Backlash Control:
- Controlling the amount of backlash (clearance between gear teeth) is essential for precise gear meshing and smooth operation.
- Properly adjusted backlash ensures proper tooth engagement without excessive play or interference.
8. Computer-Aided Design (CAD) and Simulation:
- Utilizing CAD software and gear simulation tools allows engineers to model and analyze the gear meshing behavior before manufacturing.
- Simulation helps optimize gear design parameters for smooth and efficient gear meshing.
9. Inspection and Quality Assurance:
- Thorough inspection and quality assurance procedures during and after gear production help ensure that each gear meets the required specifications.
- Non-destructive testing methods, such as gear profile checking and gear noise analysis, can be employed to assess gear meshing performance.
Precision engineering with helical gears is essential to achieve the desired level of gear meshing accuracy and performance. By paying attention to these factors, engineers can ensure that helical gears operate smoothly, efficiently, and reliably in a wide range of applications.