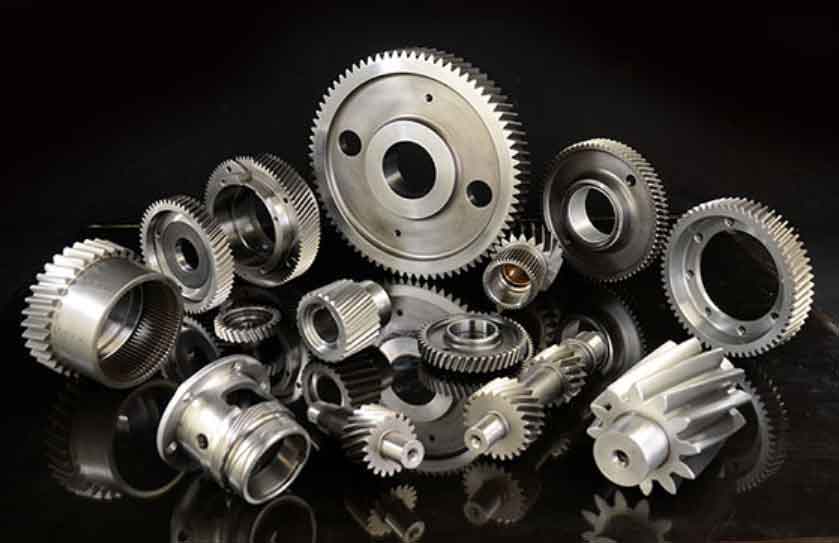
Precision engineering with helical gears involves careful consideration of various design and manufacturing aspects to ensure optimal performance and reliability. Here are key considerations for designing and manufacturing helical gears with precision:
1. Gear Geometry and Tooth Profile:
The first step in precision engineering is to determine the correct gear geometry and tooth profile. Helical gears have a helix angle, which defines the angle between the gear teeth and the gear axis. The helix angle affects the gear’s load-carrying capacity, efficiency, and smoothness of operation. Precise calculation of the helix angle is essential to ensure the gears mesh correctly and transmit power efficiently.
2. Module and Pitch Diameter:
The module, also known as the pitch, is an important parameter that defines the size and spacing of gear teeth. It is crucial to select the appropriate module based on the application requirements, as it directly affects the gear’s load-carrying capacity and meshing characteristics. The pitch diameter determines the gear’s physical size, and precise measurement and control during manufacturing are essential to achieve proper gear meshing.
3. Manufacturing Tolerances:
Precision gears require tight manufacturing tolerances to ensure accurate tooth dimensions and alignment. High-precision machining techniques, such as CNC milling and grinding, are commonly used to achieve tight tolerances and surface finishes. Maintaining consistency in manufacturing processes is critical to producing gears with uniform quality.
4. Material Selection:
Choosing the right material is crucial for precision helical gears. Factors such as load, speed, and environmental conditions influence material selection. High-quality materials with excellent mechanical properties and wear resistance, such as alloy steels or specialty materials like carburizing steel, are often used for precision gears.
5. Heat Treatment:
Proper heat treatment is essential to achieve the desired hardness and strength in the gear teeth. Processes like carburizing, quenching, and tempering are commonly employed to ensure uniform hardness and case depth. Precise control of the heat treatment process is vital to avoid distortion and achieve the desired material properties.
6. Surface Finish and Gear Accuracy:
The surface finish of gear teeth directly impacts their performance, especially in terms of noise reduction and efficiency. Precision machining and grinding techniques are used to achieve a smooth and precise tooth surface. Gear accuracy, including tooth profile, runout, and backlash, should be tightly controlled to ensure smooth and reliable gear meshing.
7. Lubrication and Gear System Optimization:
Proper lubrication is critical for the longevity and efficiency of helical gears. Adequate lubrication minimizes friction and wear, reducing the risk of premature failure. Additionally, the overall gear system design should be optimized to ensure that the helical gears work in harmony with other components, such as bearings and shafts.
8. Quality Control and Inspection:
Implementing rigorous quality control measures throughout the manufacturing process is crucial to ensure the precision of helical gears. Inspection techniques, such as coordinate measuring machines (CMM) and gear analyzers, are used to verify gear accuracy, tooth profile, and dimensional tolerances.
9. Noise and Vibration Analysis:
Precision engineering aims to minimize noise and vibration in gear systems. Advanced analysis techniques, such as finite element analysis (FEA) and vibration testing, can help identify potential noise sources and allow for design optimization.
10. Application-Specific Considerations:
Finally, the design and manufacturing of helical gears should be tailored to meet the specific requirements of the application. Factors such as load, speed, operating environment, and service life should be carefully considered during the design phase.
By taking these key considerations into account during the design and manufacturing processes, engineers can ensure that helical gears are precision-engineered to deliver optimal performance, efficiency, and reliability in a wide range of applications.