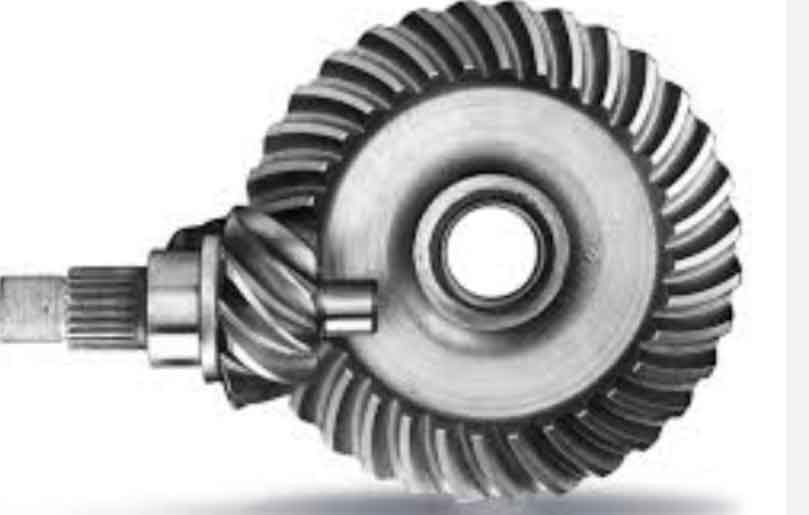
Precision engineering is crucial in the design and manufacturing of hypoid gears to ensure optimal performance, smooth operation, and durability. Several key considerations are involved in achieving precision in the production of hypoid gears:
- Gear Geometry and Tooth Design: The geometry of hypoid gears must be carefully designed to ensure proper tooth profiles, contact patterns, and meshing characteristics. Precise gear tooth design helps distribute loads evenly and minimize noise and vibration during operation.
- CAD/CAM and Simulation Tools: Computer-Aided Design (CAD) and Computer-Aided Manufacturing (CAM) software are essential tools in the precision engineering of hypoid gears. These tools facilitate the creation of accurate 3D models, virtual simulations, and analysis of gear behavior under various loads and conditions.
- Gear Material Selection: Choosing the right material for hypoid gears is critical to ensure strength, wear resistance, and durability. Common materials used for hypoid gears include alloy steels, case-hardened steels, and other specialty materials suitable for high-load applications.
- Heat Treatment and Hardening: Proper heat treatment and hardening processes are essential to achieve the desired material properties, such as hardness and toughness. Heat treatment ensures the gears can withstand the stresses and loads encountered during operation.
- Tooling and Machining Techniques: Precision machining processes, such as CNC gear cutting and grinding, are used to fabricate hypoid gears with tight tolerances and excellent surface finish. Specialized gear-cutting tools and techniques are employed to create the unique gear tooth profiles.
- Alignment and Assembly: During the assembly of hypoid gears, accurate alignment is critical to ensure smooth and efficient gear meshing. Proper alignment minimizes tooth contact errors and reduces the risk of premature wear.
- Quality Control and Inspection: Rigorous quality control measures are necessary to verify that each hypoid gear meets specified tolerances and requirements. Non-destructive testing methods, such as gear inspection with coordinate measuring machines (CMM) and gear analyzers, help ensure the gears’ precision and performance.
- Lubrication and Maintenance: Proper lubrication is essential for the smooth operation and longevity of hypoid gears. Lubricant selection and maintenance protocols are designed to minimize friction and wear, ensuring reliable performance over the gear’s lifespan.
- Specialized Manufacturing Facilities: Hypoid gears often require specialized manufacturing facilities and equipment to achieve the necessary precision and accuracy. Experienced gear manufacturers invest in modern machinery and technologies to produce high-quality hypoid gears.
Precision engineering practices in the design and manufacturing of hypoid gears result in superior performance, reduced noise levels, and increased gear life. These gears find applications in various industries, such as automotive, aerospace, robotics, and heavy machinery, where high-efficiency and reliable power transmission are critical requirements.