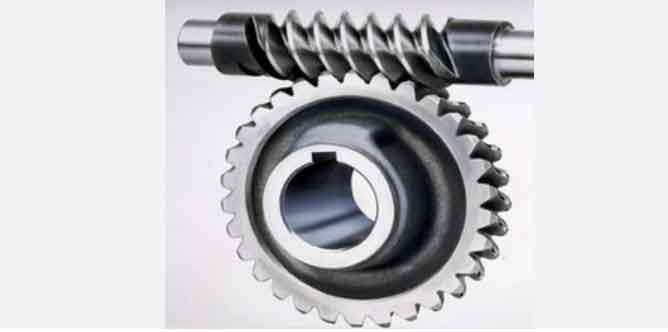
Precision engineering is crucial in worm gear systems to achieve smooth and accurate motion control. Here are key factors to consider for precision engineering in worm gear applications:
1. Gear Tooth Profile and Geometry:
Design the worm gear tooth profile and geometry to ensure precise engagement and smooth motion. Optimize parameters such as pressure angle, lead angle, and tooth profile modifications to minimize backlash, improve contact quality, and reduce noise and vibration. Proper tooth geometry ensures accurate motion transmission and minimizes positioning errors.
2. Gear Manufacturing Tolerances:
Maintain tight manufacturing tolerances for worm gears to achieve high precision. Ensure accurate tooth spacing, tooth thickness, and concentricity between the worm and worm wheel. Utilize precision machining techniques, such as grinding or honing, to achieve the required tooth profile accuracy and surface finish.
3. Proper Gear Meshing:
Achieve proper gear meshing for smooth and accurate motion. Ensure precise alignment and positioning of the worm and worm wheel during assembly. Verify the tooth contact pattern to ensure optimal meshing, load distribution, and minimal tooth surface contact misalignment. This helps reduce wear, improve efficiency, and enhance the overall performance of the worm gear system.
4. Lubrication and Friction Reduction:
Optimize lubrication to minimize friction and ensure smooth operation. Select lubricants with suitable viscosity and additives for the operating conditions. Proper lubrication reduces wear, heat generation, and power losses due to friction. Implement efficient lubrication systems to ensure consistent and sufficient lubrication to the gear teeth.
5. Backlash Control:
Minimize backlash for precise motion control and positioning accuracy. Implement techniques such as gear preloading, profile modifications, or anti-backlash devices to reduce backlash to acceptable levels. This helps eliminate lost motion and ensures accurate and repeatable positioning of the worm gear system.
6. Load Distribution and Rigidity:
Ensure proper load distribution and rigidity in the worm gear system. Design the gear housing and supporting structure to minimize deflection and ensure accurate alignment of the worm and worm wheel. Adequate rigidity prevents excessive tooth deflection, minimizes positioning errors, and improves the system’s ability to handle varying loads.
7. Control System Integration:
Integrate the worm gear system with a precision control system for accurate and synchronized motion. Utilize advanced control algorithms and feedback mechanisms, such as encoders or sensors, to monitor and adjust the position and speed of the system. This ensures precise positioning, speed control, and coordinated motion, particularly in robotics and automation applications.
8. Quality Control and Inspection:
Implement stringent quality control measures throughout the manufacturing process. Conduct thorough inspections using gear measurement tools, coordinate measuring machines (CMMs), or gear inspection machines to verify gear accuracy and adherence to design specifications. Regularly monitor and measure critical parameters to ensure precision and quality in the worm gear system.
By considering these factors and incorporating precision engineering practices, worm gear systems can achieve smooth and accurate motion control. Precise tooth profiles, tight manufacturing tolerances, proper gear meshing, effective lubrication, backlash control, load distribution optimization, control system integration, and rigorous quality control contribute to achieving the desired precision and performance in worm gear applications.