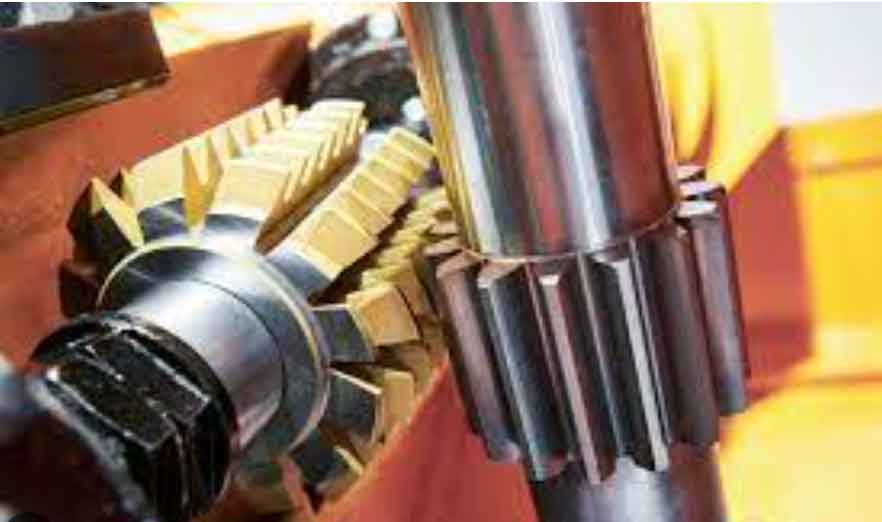
Precision gear hobbing is a critical manufacturing process that allows for the production of gears with tight tolerances and high accuracy. It involves the use of specialized gear hobbing machines and cutting tools to achieve precise tooth profiles and dimensions. Here are some key factors that contribute to achieving tight tolerances and accuracy in precision gear hobbing:
1. High-Quality Gear Hobbing Machines:
Precision gear hobbing requires modern, well-maintained gear hobbing machines with high rigidity and precision. These machines are designed to minimize vibrations and deflections during the cutting process, ensuring accurate and consistent gear tooth profiles.
2. CNC Control:
Computer Numerical Control (CNC) technology is commonly used in precision gear hobbing machines. CNC control enables precise and automated positioning of the cutting tool, allowing for tight control over the gear’s tooth profile and dimensions.
3. High-Quality Cutting Tools (Hobs):
Using high-quality hobs made from premium materials such as high-speed steel (HSS) or carbide is crucial for precision gear hobbing. These cutting tools maintain their sharpness and shape, contributing to accurate gear cutting and prolonged tool life.
4. Proper Tool Design and Setup:
The design and setup of the hob play a significant role in achieving tight tolerances. The hob’s tooth profile must precisely match the gear’s intended tooth profile, and the hob’s position and alignment must be carefully adjusted to ensure proper contact with the workpiece.
5. Gear Blank Quality:
High-quality gear blanks with precise dimensions and material properties are essential for achieving accurate gear profiles. Proper material selection is crucial, especially for high-precision gears that may require heat treatment or special surface treatments.
6. Cutting Parameters Optimization:
Optimizing the cutting parameters, such as cutting speed, feed rate, and depth of cut, is essential for achieving tight tolerances. Finding the right balance between productivity and precision is crucial for high-quality gear hobbing.
7. In-Process Inspection and Feedback:
Implementing in-process inspection and feedback systems allows real-time monitoring of the gear hobbing process. Any deviations from the desired tolerances can be detected and corrected promptly, ensuring consistent accuracy throughout production.
8. Quality Control and Post-Process Inspection:
After the gear hobbing process, gears undergo thorough post-process inspection to verify their accuracy and adherence to tight tolerances. This may involve measuring gear tooth dimensions, tooth profiles, surface finish, and hardness.
9. Process Expertise and Skilled Operators:
Precision gear hobbing requires experienced operators with expertise in gear manufacturing processes. Skilled operators can make adjustments and fine-tune the process to achieve the desired precision and accuracy.
10. Advanced Simulation and Modeling:
Computer simulations and modeling tools allow gear manufacturers to predict and optimize the gear hobbing process before actual machining. This helps in selecting the right cutting parameters and making design improvements.
By integrating these factors into the gear hobbing process, manufacturers can achieve tight tolerances and high accuracy, meeting the stringent requirements of industries that rely on precision gears for optimal performance and reliability.