The author uses the dexel based solid modeling system (module works) to realize the kinematic model of strong tooth scraping. The workpiece is represented by an array of parallel line segments whose starting and ending points describe the outer surface of the material.
The tool shape is described by triangular mesh. The triangular mesh representation of scraper and its cutting shape are shown in Figure 1.
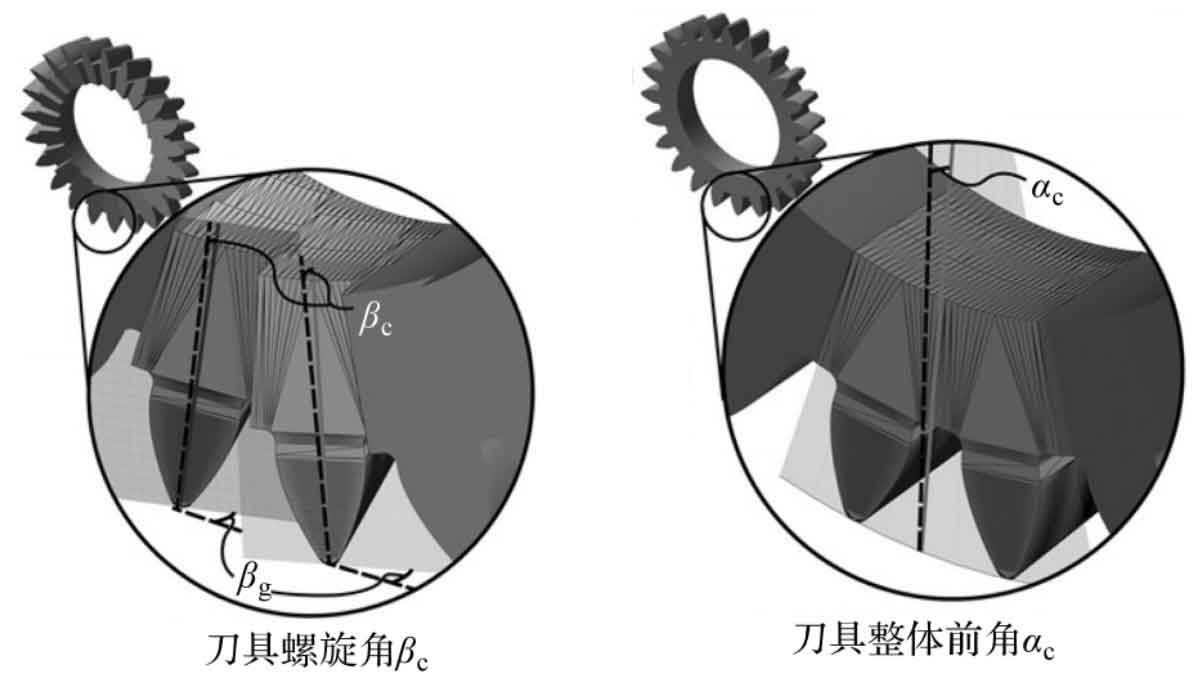
By defining the position and orientation (pose) of the tool relative to the workpiece, the author performs cutting in discrete time steps; In each time step of the current workpiece, Boolean subtraction is performed on the scanned cutting volume to generate an updated workpiece geometry.
The simulation of dexel strong tooth scraping based on WCS is shown in Figure 2.
The method of extracting two-dimensional chip shape of cylindrical gear scraping motion from CWE represented by dexel is shown in Fig. 3.
In Fig. 3, the dexel representation of the three-dimensional undeformed chip shape of the cylindrical gear scraping motion is used to construct the two-dimensional chip cross section; The three-dimensional chip boundary is estimated by connecting the endpoints of parallel dexel, and the contour is effectively created around each XY, XZ and YZ plane of dexel data; Then, the contour intersects the plane or conical rake face of the scraper to produce a two-dimensional point cloud of the chip cross section. The author uses diloni triangulation and alpha shape algorithm to obtain the final two-dimensional undeformed chip shape. The threshold of alpha shape algorithm is the root 3D, where: d-dexel resolution.
The tool edge is discretized into multiple points (called nodes), which are defined at the tool pose at the half time step. Then, the ZHY gear senior engineer team associates the triangle of the chip shape of the cylindrical gear scraping motion with the nearest node, and the geometry of each triangle is used to calculate the local chip area a of its associated node; Finally, the oblique cutting force model is applied to each node to obtain the cutting force prediction of each time step.