Spiral bevel gears have indeed sparked a “quiet revolution” in gearbox technology due to their unique design and advantages over other gear types. Here are some key ways in which spiral bevel gears are transforming gearbox technology:
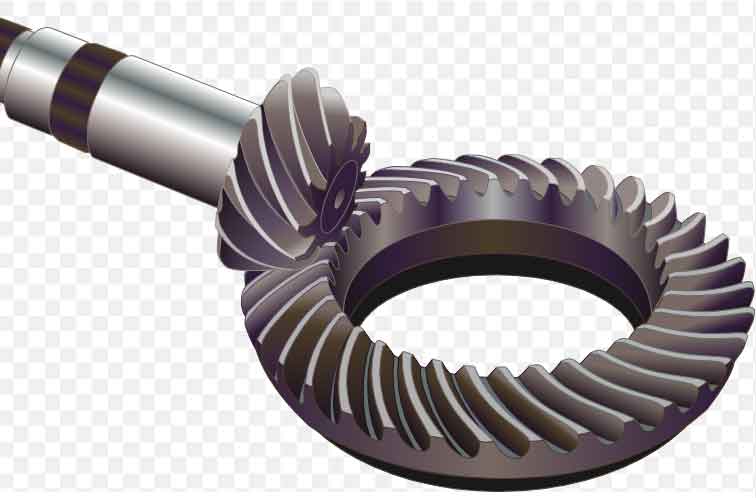
1. Noise Reduction:
One of the most significant advantages of spiral bevel gears is their ability to operate with significantly reduced noise and vibration compared to straight bevel gears. The helical tooth design of spiral bevel gears results in gradual tooth engagement, leading to smoother meshing and lower impact forces. This characteristic helps in minimizing gear noise and vibration, making them ideal for applications where quiet operation is crucial, such as in automotive differentials, industrial gearboxes, and aerospace systems.
2. High Efficiency:
Spiral bevel gears offer higher efficiency compared to worm gears, especially in applications where power transmission occurs at right angles. The smooth, continuous meshing of the helical teeth results in reduced friction, leading to less energy loss and improved power transmission efficiency. As a result, spiral bevel gears are widely used in high-speed and high-torque applications, such as in heavy machinery and automotive drivetrains.
3. Torque Transmission:
Spiral bevel gears excel in transmitting torque between intersecting shafts. Their design allows for better load distribution and increased surface contact area, enabling them to handle high torque loads efficiently. This feature is particularly valuable in heavy-duty applications, where the gearbox needs to withstand significant forces.
4. Compact Design:
Spiral bevel gears can achieve high gear ratios in a relatively compact design, making them suitable for space-constrained applications. Their ability to transmit power at right angles allows for efficient gearbox configurations, especially in situations where space is limited, such as in automotive transmissions and small gearboxes for industrial machinery.
5. Precision and Customization:
Advancements in gear manufacturing technology, such as CNC machining and 3D printing, have enabled the production of highly precise and customized spiral bevel gears. This level of precision allows engineers to tailor the gears to specific application requirements, ensuring optimal performance and reliability.
6. Robustness and Durability:
Spiral bevel gears are known for their robustness and durability, making them suitable for demanding and heavy-duty applications. With the use of high-quality materials and advanced heat treatment techniques, spiral bevel gears can withstand harsh operating conditions and provide long service life.
7. Advancements in Manufacturing Techniques:
Innovations in gear manufacturing techniques, such as multi-axis CNC machining and high-precision grinding, have further improved the accuracy and quality of spiral bevel gears. These advancements enable the production of gears with tighter tolerances and better surface finishes, resulting in enhanced performance and reduced wear.
8. Versatility and Adaptability:
Spiral bevel gears can be adapted to various applications and industries, from automotive and aerospace to industrial machinery and robotics. Their versatility, combined with their numerous advantages, makes them a preferred choice for many gear-driven systems.
The unique characteristics of spiral bevel gears, such as reduced noise, high efficiency, torque transmission capability, and adaptability, have contributed to a “quiet revolution” in gearbox technology. As technology continues to evolve, we can expect further improvements in spiral bevel gear design and manufacturing, leading to even more transformative impacts on gearboxes and power transmission systems.