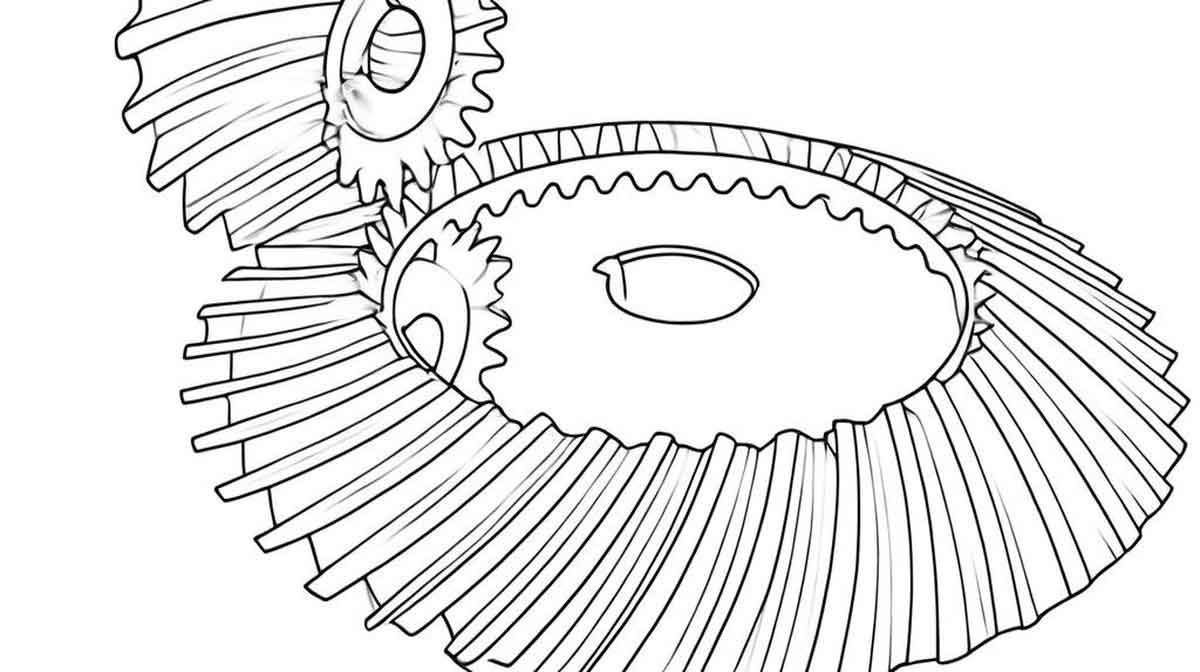
1. Introduction
Spiral bevel gear plays crucial role in many mechanical systems, especially in automotive applications. They are used in the rear axle of automobiles to transmit power between the driveshaft and the wheels. The proper functioning of spiral bevel gear is essential for the smooth operation and safety of the vehicle. However, these gears are prone to distortion, which can lead to various problems such as noise, vibration, and reduced efficiency.
1.1 Importance of Spiral Bevel Gear in Automotive Applications
In an automotive rear axle, spiral bevel gear is responsible for changing the direction of the rotational force from the driveshaft to the wheels at a right angle. This allows the wheels to turn while the driveshaft rotates in a different direction. The design and performance of spiral bevel gear directly impact the vehicle’s handling, acceleration, and overall driving experience.
1.2 Challenges Associated with Spiral Bevel Gear Distortion
Distortion in spiral bevel gear can occur due to various factors such as manufacturing errors, improper heat treatment, high loads, and incorrect assembly. This distortion can cause misalignment between the gear teeth, resulting in increased friction, wear, and noise. It can also lead to a reduction in the gear’s load-carrying capacity and efficiency.
2. Existing Methods for Spiral Bevel Gear Distortion Control
Several methods have been proposed in the literature to control the distortion of spiral bevel gear. These methods can be broadly classified into two categories: traditional methods and advanced methods.
2.1 Traditional Methods
Traditional methods for spiral bevel gear distortion control include heat treatment, machining, and assembly techniques.
Traditional Method | Description | Advantages | Disadvantages |
---|---|---|---|
Heat Treatment | Adjusting the microstructure of the gear material through processes like quenching and tempering to reduce internal stresses and improve dimensional stability. | Can improve the mechanical properties of the gear material. | Requires precise control of temperature and time, and may not completely eliminate distortion. |
Machining | Using precision machining techniques such as grinding and milling to achieve accurate gear tooth profiles and dimensions. | Can produce gears with high dimensional accuracy. | Time-consuming and expensive, especially for complex gear geometries. |
Assembly | Ensuring proper alignment and fit of the gears during assembly to minimize distortion caused by misalignment. | Simple and cost-effective if done correctly. | Requires skilled labor and careful inspection to ensure proper assembly. |
2.2 Advanced Methods
Advanced methods for spiral bevel gear distortion control involve the use of modern technologies such as finite element analysis (FEA), computer-aided design (CAD), and non-destructive testing (NDT).
Advanced Method | Description | Advantages | Disadvantages |
---|---|---|---|
FEA | Using numerical simulation to analyze the stress and deformation of the gear during operation, and optimizing the design accordingly. | Can predict and prevent distortion before manufacturing. | Requires accurate material properties and boundary conditions, and may be computationally expensive. |
CAD | Designing the gear using computer software to ensure accurate geometry and dimensional control. | Allows for easy modification and optimization of the design. | Depends on the operator’s skill and knowledge of the software. |
NDT | Using techniques such as ultrasonic testing, magnetic particle inspection, and X-ray diffraction to detect and evaluate the presence of distortion in the gear. | Can detect internal defects and distortion without damaging the gear. | May require specialized equipment and trained personnel, and may not provide detailed information about the cause of distortion. |
3. Proposed Method: Spiral Bevel Gear Distortion Control Based on Phased Array Ultrasound
In this section, we will discuss the proposed method for spiral bevel gear distortion control based on phased array ultrasound. This method combines the advantages of ultrasound technology with advanced signal processing algorithms to achieve accurate and efficient distortion control.
3.1 Principles of Phased Array Ultrasound
Phased array ultrasound is a technique that uses an array of ultrasonic transducers to generate and receive ultrasonic waves. By controlling the phase and amplitude of the waves emitted by each transducer, it is possible to focus the ultrasound beam at a specific location and direction. This allows for detailed inspection and measurement of the internal structure of the gear.
3.2 Gear Vibration Signal Acquisition and Preprocessing
The first step in the proposed method is to acquire the vibration signal of the spiral bevel gear using phased array ultrasound technology. The acquired signal is then preprocessed to remove noise and other artifacts.
3.2.1 Signal Acquisition
The phased array ultrasound sensor used in this method has a specific structure and configuration. It consists of a wafer array plane, an absorbing device, a matching layer, and electrode leads. The array plane contains multiple independent elements, which are arranged in a specific pattern to achieve the desired beamforming effect.
3.2.2 Noise Reduction
The acquired vibration signal is often contaminated with noise due to various factors such as environmental interference and the presence of other mechanical components. To improve the signal quality, a noise reduction algorithm based on anisotropic diffusion is employed. This algorithm uses a partial differential equation to diffuse the local dispersion operator of the gear vibration signal, effectively reducing the noise while preserving the important features of the signal.
3.3 Gear Distortion Signal Feature Extraction
After preprocessing the vibration signal, the next step is to extract the features of the distortion signal. This is achieved using a combination of distortion scattering algorithms and curve matrix echo algorithms.
3.3.1 Distortion Scattering Algorithm
When the gear surface is distorted, it generates scattering waves. The distortion scattering algorithm calculates the scattering amplitude of these waves, which provides information about the echo characteristics of the distortion signal.
3.3.2 Curve Matrix Echo Algorithm
The curve matrix echo algorithm is used to locate the distortion signal accurately. It calculates the distance between the transducer elements and the distortion location, and determines the coordinates of the distortion signal position point. Based on these coordinates, the features of the distortion signal can be extracted.
3.4 Gear Distortion Control
Finally, based on the extracted distortion signal features, a resampling distortion control technique is used to control the gear distortion. This technique takes into account the Doppler effect and uses different frequency offset reference points to resample the signal and adjust the gear geometry.
3.4.1 Doppler Effect Consideration
When using phased array ultrasound to measure the gear vibration signal, the Doppler effect can occur due to the relative motion between the sensor and the gear. This effect causes a shift in the frequency of the received signal, which needs to be considered in the distortion control process.
3.4.2 Resampling Technique
The resampling technique uses the frequency offset curvature of the distortion signal features to determine the appropriate resampling points. By resampling the signal at these points, the gear geometry can be adjusted to correct for the distortion.
4. Experimental Results and Analysis
To evaluate the performance of the proposed method, a series of experiments were conducted on automotive rear axle spiral bevel gear. The results of these experiments were compared with those of existing methods to demonstrate the superiority of the proposed method.
4.1 Experimental Setup
The experimental setup consisted of a phased array ultrasound sensor, a signal acquisition system, and a computer for data processing and analysis. The spiral bevel gear were mounted on a test rig and subjected to various loading conditions to simulate real-world operating scenarios.
4.2 Evaluation Metrics
The performance of the distortion control methods was evaluated using two main metrics: distortion control effect and distortion control precision.
Metric | Description |
---|---|
Distortion Control Effect | The degree to which the distortion of the gear is reduced after applying the control method. This is measured by observing the shape and smoothness of the gear tooth profile. |
Distortion Control Precision | The accuracy with which the control method can correct the distortion. This is measured by comparing the actual distortion before and after control with the desired distortion level. |
4.3 Results Comparison
The experimental results showed that the proposed method based on phased array ultrasound had a significantly better performance compared to existing methods.
4.3.1 Distortion Control Effect
In terms of distortion control effect, the proposed method was able to reduce the distortion of the spiral bevel gear to a much greater extent than the existing methods. The gear tooth profile after control using the proposed method was much smoother and closer to the ideal shape.
4.3.2 Distortion Control Precision
Regarding distortion control precision, the proposed method also demonstrated a higher level of accuracy. The error between the actual distortion and the desired distortion level was much smaller for the proposed method compared to the existing methods.
5. Conclusion
In this article, we have presented a comprehensive study on the distortion control of spiral bevel gear, with a particular focus on the proposed method based on phased array ultrasound. The following are the main conclusions:
5.1 Summary of the Proposed Method
The proposed method combines phased array ultrasound technology with advanced signal processing algorithms to achieve accurate and efficient distortion control of spiral bevel gear. It involves the acquisition and preprocessing of gear vibration signals, extraction of distortion signal features, and application of a resampling distortion control technique.
5.2 Advantages over Existing Methods
Compared to existing methods, the proposed method has several advantages. It provides a more accurate and detailed inspection of the gear internal structure, can effectively reduce noise in the signal, and achieves higher distortion control precision and effect.
5.3 Future Research Directions
Despite the promising results of the proposed method, there are still some areas that require further research. For example, the optimization of the signal processing algorithms, the development of more efficient phased array ultrasound sensors, and the investigation of the long-term performance of the controlled gears under different operating conditions.
In conclusion, the proposed method based on phased array ultrasound shows great potential for the distortion control of spiral bevel gear in automotive applications. Further research and development in this area will likely lead to improved gear performance and reliability, contributing to the overall safety and efficiency of vehicles.