Abstract
The herringbone gear transmission system serves as the core subsystem in modern high-speed and heavy-load mechanical equipment. Scuffing, caused by the continuous increase of tooth surface temperature during transmission contact, has emerged as one of the primary failure modes of this system. This failure often occurs instantaneously and unpredictably, limiting the service life and reliability of the equipment. The contact characteristics of gear tooth surfaces determine the anti-scuffing capacity of herringbone gears. This paper addresses the unclear contact characteristics during the meshing process of herringbone gears and the scarcity of research on their scuffing load capacity.
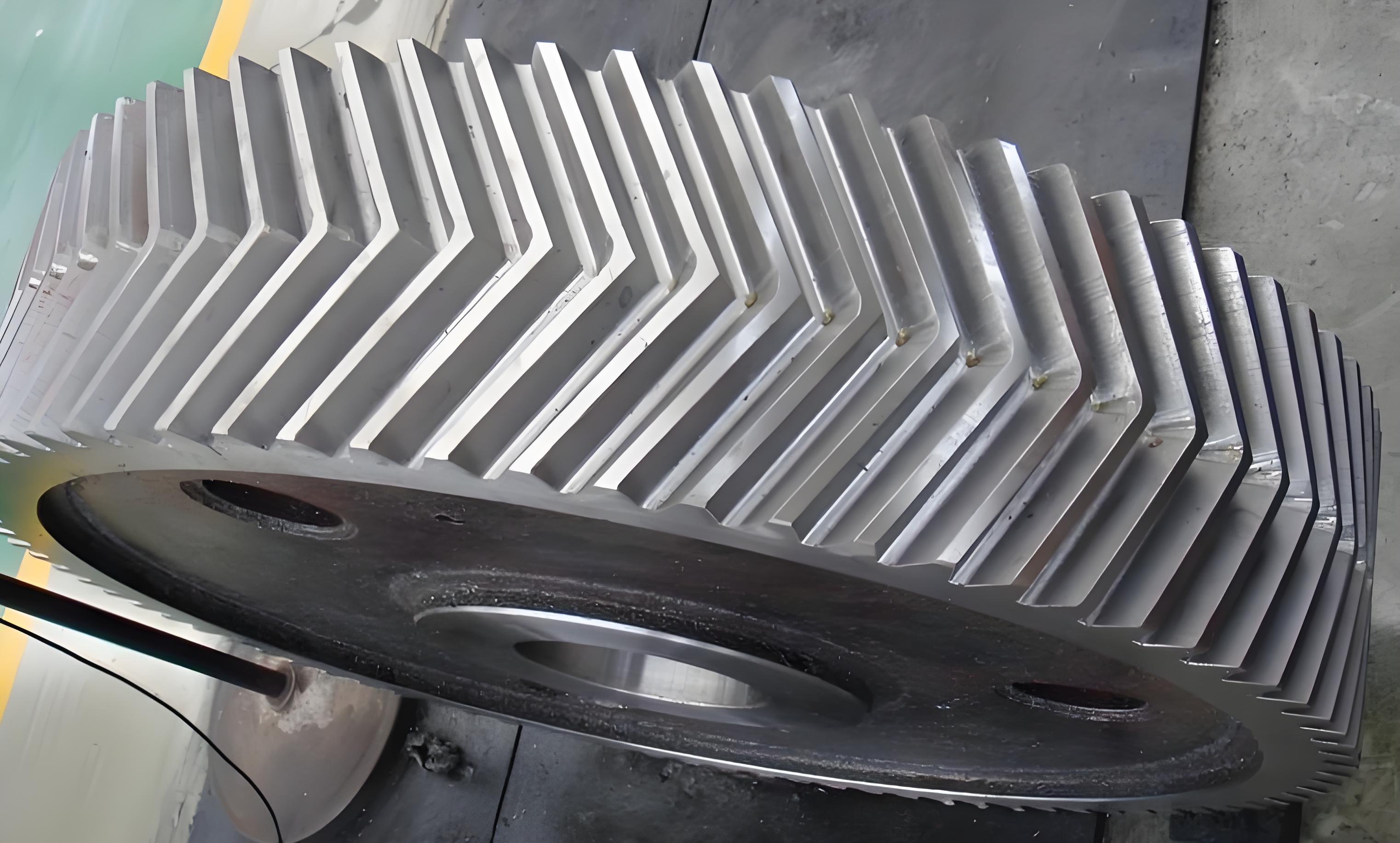
1. Introduction
1.1 Background and Significance
The machinery industry is a fundamental strategic industry for national economic development, providing core technical equipment for various industries and national defense construction. Herringbone gears, as crucial basic components in modern mechanical equipment, are widely used in the power transmission systems of core defense equipment such as new surface ships, nuclear submarines, and aerospace engines. The technical level of herringbone gears determines the power performance of the entire mechanical device. With the evolving market demands, gear transmission systems are rapidly developing towards smaller volumes, stronger carrying capacities, longer service lives, and higher reliability. Under these circumstances, higher requirements are placed on the carrying capacity of herringbone gears, particularly their contact characteristics under high-speed and heavy-load conditions, which directly affect the stable operation and reliable service of the transmission system.
1.2 Research Status
Table 1: Summary of Research on Gear Anti-Scuffing Performance
Researcher | Year | Focus | Key Findings |
---|---|---|---|
D. Popgoshev | 1980s | Material and lubricant combination | 3Ni-4.5Mo alloy with MIL-L-23699 lubricant enhances gear load capacity |
M. J. Patching | – | Hertz contact theory and surface finish | Pre-scuffing friction reduction on ultra-finished surfaces |
B. R. Höhn | – | FZG gear test rig and lubricant performance | Evaluation of API GL-4 and GL-5 lubricants |
Powrie | – | Electrostatic charge signal detection | Early detection of scuffing failure |
M.P. Alanou | – | Surface treatment and coatings | Ultra-finishing and Me-DLC coatings improve scuffing resistance |
2. Mixed Thermal Elastohydrodynamic Lubrication (TEHL) Analysis of Herringbone Gears
The main reason for scuffing failure in high-speed and heavy-load herringbone gear transmission systems is the gradual destruction of the ideal full-film lubrication state due to many complex and coupled factors, transitioning from full-film elastohydrodynamic lubrication (EHL) to boundary lubrication, and remaining in mixed TEHL for an extended period.
3. Instantaneous Thermal Characteristics and Flash Temperature Calculation
3.1 Factors Influencing Flash Temperature
- Sliding and Rolling Friction
- Thermal Deformation
- Operational Speed and Load
3.2 Calculation Method
The contact temperature of herringbone gears during meshing gradually increases until it reaches a steady state. The contact temperature T can be expressed as:
T = Tbulk + Tflash
Where Tbulk is the bulk temperature of the gear, and Tflash is the flash temperature.
Table 2: Factors Affecting Gear Contact Temperature
Factor | Description | Impact |
---|---|---|
Load | Increases friction and heat generation | Increases contact temperature |
Rotational Speed | Affects sliding velocity and heat dissipation | Influences temperature distribution |
Lubricant Viscosity | Affects heat transfer and film thickness | Influences lubrication state and temperature |
Surface Roughness | Influences contact area and friction coefficient | Affects heat generation and temperature |
4. Anti-Scuffing Load Capacity Calculation Method
4.1 Existing Methods
- Oil Film Thickness Method (AGMA)
- Maximum Contact Flash Temperature Method (ISO)
- Integral Temperature Method
4.2 Proposed Method
Based on the ISO 14635-1 and GB/Z 13672 gear scuffing load capacity test standards, a numerical calculation method is proposed to analyze the scuffing load capacity of herringbone gears, considering tooth surface friction and wear.
5. Experimental Verification
5.1 FZG Scuffing Test Procedure
The FZG scuffing test procedure was used to investigate the scuffing load capacity of herringbone gears. A numerical simulation model was established to predict the scuffing failure stage.
5.2 Results and Analysis
- Contact Temperature and Friction Heat Flux Increase with input torque, peaking at mesh-in and mesh-out points.
- Lubricant Viscosity Decreases with temperature, leading to reduced film thickness and increased scuffing risk.
- Scuffing Failure Stage Predicted to be between the 10th and 11th test stages, with boundary lubrication and significant temperature rise.
Table 3: Summary of Experimental Results
Test Stage | Contact Temperature (°C) | Lubricant Film Thickness (μm) | Scuffing Status |
---|---|---|---|
1-9 | Increasing | Stable | No scuffing |
10-11 | Peak (122°C) | Minimum, film rupture | Scuffing |
6. Conclusion
This paper focuses on herringbone gears in high-speed and heavy-load mechanical equipment, analyzing their lubrication state and tooth surface contact temperature based on mixed TEHL theory. By comparing calculations using ISO standards with an improved method, the impacts of various parameters on contact temperature were studied. Considering continuous friction and wear on tooth surface contact states, a numerical calculation model for herringbone gear scuffing load capacity was established. Experimental verification was conducted using the FZG scuffing test, analyzing the influence of tooth surface contact state changes on scuffing failure stages. This research provides theoretical guidance for designing herringbone gear anti-scuffing capacity and improving prediction accuracy.