With the rapid development of the automobile industry, automobile users have higher and higher requirements for the comfort of automobile ride, and the quality of NVH (noise, vibration and harshness) has been paid more and more attention. The performance of NVH has become an important index to measure the quality of automobile manufacturing. As the heart of automobile, powertrain system not only affects the dynamic performance of automobile, As an important part of automobile power transmission system, transmission is one of the main sources of vibration and noise of powertrain
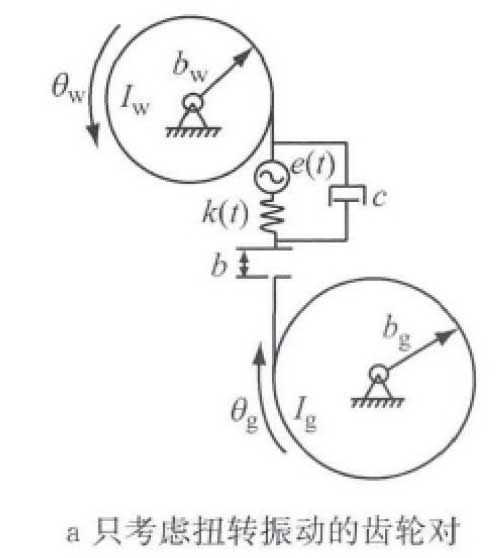
Automobile transmission noise is divided into five categories, including transmission squeal noise, transmission gear knock noise, gear shift noise, bearing noise and close noise. For gear system, according to different vibration states, the vibration noise is mainly divided into gear knock and squeal noise. Among them, gear knock noise occurs in the constant meshing non bearing gear pair, When the transmission is put into a certain gear, the non load-bearing gear which is not put into gear is sleeved on the transmission shaft. Because there is backlash between the gear pairs, if the amplitude of the circumferential movement displacement difference of the non load-bearing gear pair exceeds the magnitude of backlash between the teeth, there will be knocking phenomenon. The strong knocking vibration between the non load-bearing gear pairs is mainly transmitted to the transmission housing through the transmission shaft and bearings, The transmission case radiates noise when it is excited. The knocking phenomenon of transmission gear has obvious wide-band noise characteristics and noise level jumping phenomenon [2], which makes it different from other transmission system noises, easily makes the passengers fidgety and uneasy, and seriously affects the ride comfort of the vehicle. Therefore, it is very important to study the knocking phenomenon of transmission gear.
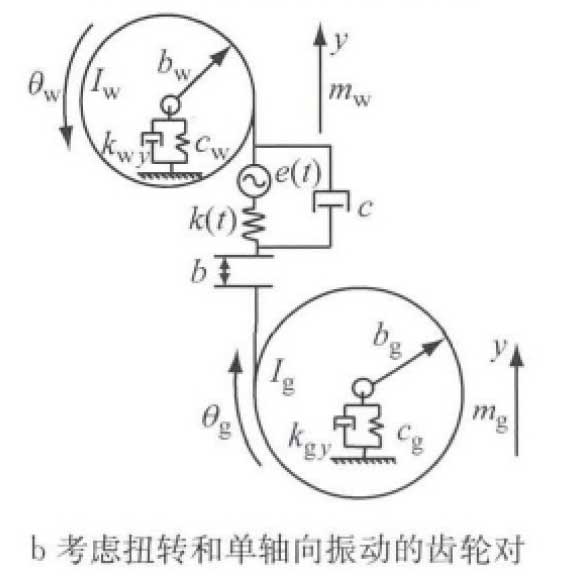
The research on gear knocking first appeared in the 1970s, when it was aimed at the research on the classical model of “vibration impact”. The research focuses on the solution method and dynamic characteristic analysis. With the deepening of research, the research focus is no longer a single “vibration impact” model, Li Runfang and Wang Jianjun [3] discussed the theoretical system, research trends and development trends of gear system dynamics as a whole earlier, with emphasis on the research content and methods of parameter vibration of gear system, However, the problem of gear knocking (slapping) in automobile transmission system is only discussed preliminarily [4], Domestic and foreign researchers and institutions have made a lot of achievements in the study of this problem
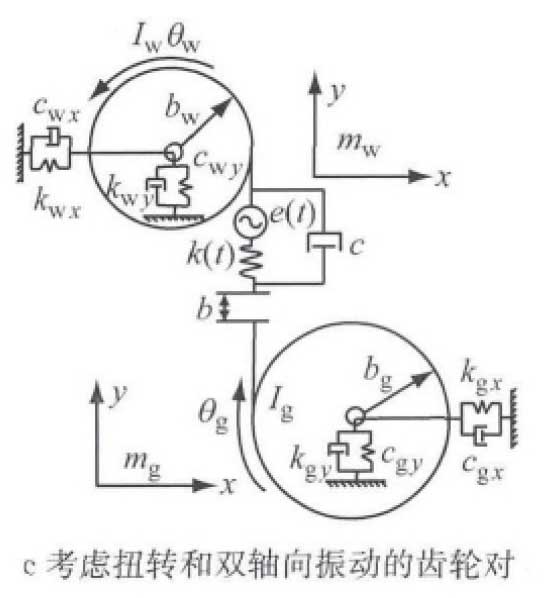
This paper discusses the present situation and development trend of the research on the knock dynamics of automobile transmission gears at home and abroad, focusing on the mechanism of knock noise of automobile transmission gears, the solution method of theoretical analysis model, the objective evaluation method of knock of transmission gears, the knock test of gears and the solutions to knock problems, This paper analyzes the research results and shortcomings of the current research on the problem of gear knock in transmission. Finally, it makes a summary and prospect from the perspectives of refinement and accuracy of the simulation model of gear knock, effectiveness of the test scheme, objective evaluation index and rationalization of the knock method, so as to clarify the direction of the research on the dynamic problem of gear knock in transmission.
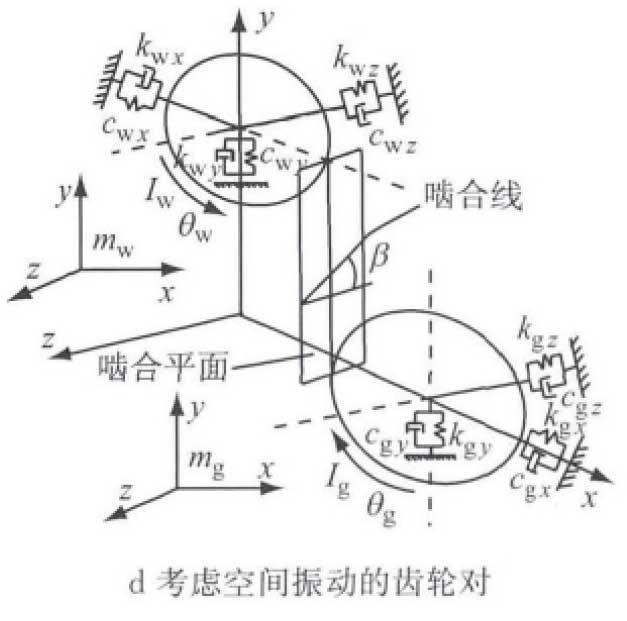
Singh firstly applied the single pair of gear pair knock model in Figure 1a to study the knock problem of the neutral gear in the automobile transmission, and proved the feasibility. The knock model of the neutral gear in the transmission is shown in Figure 2, in which the nonlinear stiffness characteristics of the clutch and the speed fluctuation of the flywheel are considered. In the figure, I (I = 1,2,3, 4) It is the moment of inertia of flywheel, clutch, driving gear and passive gear, kg · m2; θ I (I = 1,2,3,4) is the angular displacement of flywheel, clutch, driving gear and passive gear respectively, RAD; TC is the transmission torque of clutch, n · m; TB is the transmission torque of main passive gear, n · m; CI (I = 1,2) is the damping of active and passive gear respectively, N · m · s · rad-1. The influence of the nonlinear characteristic parameters of the clutch on the knocking strength of the neutral gear is analyzed and discussed, which lays a theoretical foundation for restraining the knocking of the neutral gear through the adjustment of the clutch parameters.
When considering the influence of stiffness and damping of bearing or transmission shaft support, the model in Fig. 1a is expanded. The analysis model of single pair spur gear to multi degree of freedom is shown in Fig. 1b. The variable description in the figure can be analyzed by reference [11]. Kahraman et al. [11], The numerical simulation method is used to compare the influence of gear static transmission and external torque fluctuation on the amplitude frequency characteristics of the system.
When considering the friction of tooth surface, the translational freedom of gear in the direction perpendicular to the meshing line must also be considered. The corresponding analysis model of single-stage spur gear pair is shown in Fig. 1C. The variable description in the figure can be referred to reference. Siyu C et al. through the study of the model, the frequency response characteristics of gear to relative displacement when considering friction and without considering friction are analyzed and compared. The results show that, Friction has an effect on the frequency response amplitude of relative displacement of gears. For example, in the low frequency range, the frequency response amplitude of gears considering friction is smaller than that of gears not considering friction. It can be seen that the friction between gears is an important factor to be considered in the study of the knock model of gears.
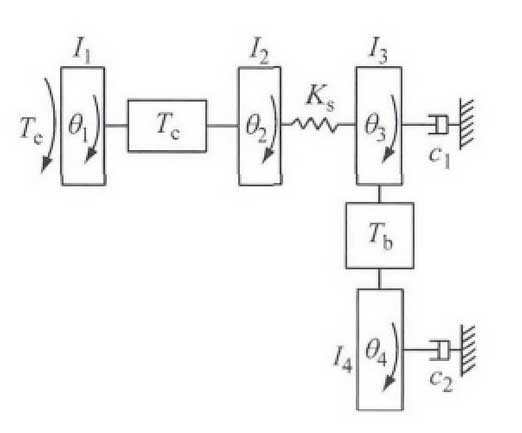
The single pair of gear pairs shown in Fig. 1a, B and C are all straight gear pairs, and the gears used in the automobile transmission are all helical gear pairs. The helical gear mesh will generate axial dynamic meshing component, forming the bending torsion shaft coupling vibration of the gear system. The dynamic model of the helical gear pair at this time is shown in Fig. 1D, which is a three-dimensional vibration system, At this time, the gear backlash in the model is defined as normal backlash, and the variables in the figure can be explained in reference [13]. Wei Jing et al. [13] comprehensively consider the nonlinear factors such as time-varying meshing stiffness and backlash for the single pair of helical teeth model, This paper studies the influence of excitation frequency, meshing damping, backlash and other parameters on the vibration response of the system as well as the bifurcation and chaos characteristics of the system caused by each parameter. The single pair helical gear pair model is the basis of the complex transmission model. When establishing the vibration analysis model of the automobile transmission gear system, it should be based on the specific situation of the gear system and the analysis purpose and requirements, Different types of single pair of gears are used to knock the foundation model.