Shu Qifu once put forward the concept of “equivalent blank” to study the influence of taper on the forming process of bevel gear by die forging, but the blank of bevel gear he discussed does not contain tooth shape. Therefore, it is necessary to study the influence of gear blank taper on the closed hot die forging process of spiral bevel gear.
In the previous research on the influence of tooth shape on the hot die forging process of driven spiral bevel gear, it was found that the tooth shape of gear blank was not formed at the same time: after the tooth height direction was formed to a certain extent, the material first flowed to the outer diameter direction to form the tooth shape at the outer diameter of the gear, and then reversed the direction to form the tooth shape at the inner diameter of the gear. This leads to the metal accumulation in the local area of the big end when the small end tooth at the inner diameter is formed. In order to eliminate this part of influence as much as possible, the small end of the gear blank should contact the die first so that the filling process of the big and small end of the tooth profile can be completed synchronously, that is, the taper β of the gear blank should be smaller than the root taper α of the tooth profile die.
Taper design of preform for closed hot die forging
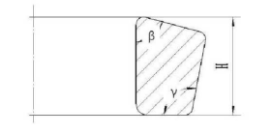
The diagram of gear blank taper is as shown in the figure, in which β is the tooth surface angle (taper) of spiral bevel gear blank, γ is the base angle of spiral bevel gear blank, and H is the height of gear blank. In order to keep the volume constant before and after deformation, the height h should decrease with the increase of the gear blank taper.
Establishment of finite element model and setting of relevant parameters
In CATIA, the 3D modeling of preforms with different taper is completed. The mold model is based on the digital model used in the previous section. The gear blank and die data to analog conversion format are imported into DEFORM-3D.