Abstract: This article reviews the major heat treatment processes employed in the manufacturing of automotive gears, emphasizing advancements in pre-heat treatment, carburizing, carbonitriding, nitriding, and induction hardening. Emerging heat treatment technologies such as laser quenching, low-pressure vacuum carburizing, and rare earth co-infiltration are also briefly discussed along with their application statuses. Finally, the development direction of automotive gears heat treatment processes towards high quality, low energy consumption, environmental protection, and intelligence is outlined.
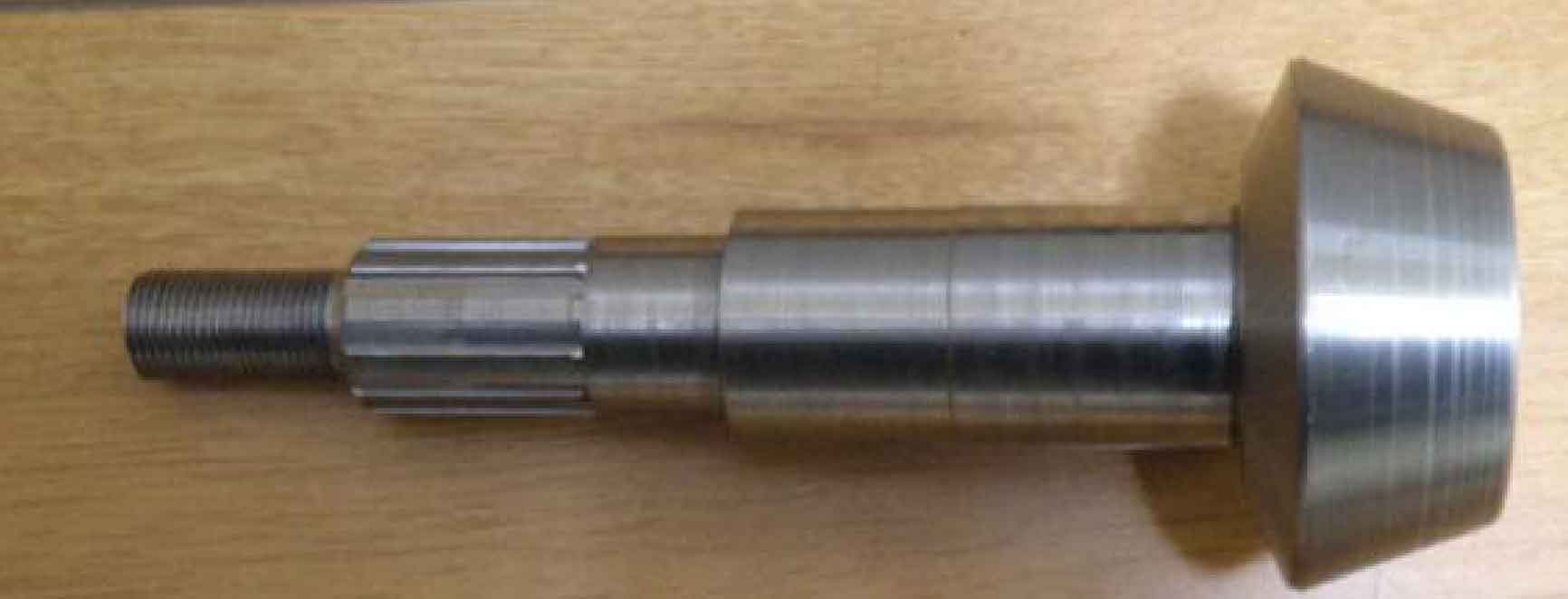
1. Overview of Automotive Gear Heat Treatment Processes
Automotive gears, serving as crucial components in the transmission system, transmit power and alter speed and direction. Due to the complex operating conditions of automotive gears, the automotive industry demands gears with superior wear resistance, high contact fatigue resistance, and bending fatigue resistance. The quality of automotive gears in China still lags behind similar products in developed countries, mainly manifested in shorter average service life, higher energy consumption per unit product, and lower productivity. To enhance gear quality, besides selecting suitable materials, optimizing heat treatment processes is essential.
Heat Treatment Processes | Description |
---|---|
Pre-heat Treatment | Obtains suitable surface hardness and prepares the microstructure for subsequent heat treatment. |
Carburizing | Enhances the comprehensive mechanical properties of gears. |
Carbonitriding | Effectively increases the case depth, improves hardness, and reduces deformation. |
Nitriding | Improves wear resistance and corrosion resistance at low temperatures. |
Induction Hardening | Provides high efficiency, low deformation, and environmental friendliness. |
2. Major Heat Treatment Processes
2.1 Pre-heat Treatment Processes
Pre-heat treatment of automotive gears forgings is primarily to obtain suitable surface hardness and prepare the microstructure for subsequent heat treatment. Conventionally, normalizing is widely used due to its simple equipment, low energy consumption, and low process requirements. However, as the quality requirements for automotive gears increase, particularly with the diversification of steel materials used in imported vehicle models, isothermal annealing is gradually replacing normalizing.
Pre-heat Treatment Method | Advantages | Disadvantages |
---|---|---|
Normalizing | Simple equipment, low energy consumption | Uneven microstructure, large hardness fluctuations |
Isothermal Annealing | Uniform microstructure and hardness, reduced deformation | High energy consumption |
2.2 Carburizing Process
Carburizing is the most widely used surface hardening process for low-carbon steel in automotive gears production. While conventional carburizing often forms a thin layer of non-martensitic structure on the gear surface, significantly affecting fatigue performance, vacuum carburizing offers advantages such as energy saving, fast carburizing speed, and ease of control.
Carburizing Method | Advantages | Challenges |
---|---|---|
Gas Carburizing | Widely used, controllable carburizing depth and surface hardness | Formation of non-martensitic structure, high temperature, long cycle, large deformation |
Vacuum Carburizing | Energy-saving, fast carburizing speed, safe and environmentally friendly | Carbon black insulation issues, uniformity problems |
2.3 Carbonitriding Process
Carbonitriding is frequently used due to its ability to effectively increase case depth within a given time, achieve high hardness, ensure fine austenitic grain size, reduce part deformation, and improve gear strength and wear resistance.
Carbonitriding Method | Advantages | Limitations |
---|---|---|
Gas Carbonitriding | High hardness, fine austenitic grains | Difficult to control microstructure stability, long time required for deep case depth |
Vacuum Carbonitriding | Expands material range, reduces deformation, improves wear and corrosion resistance | High initial investment |
2.4 Nitriding Process
Nitriding is a traditional heat treatment process, but its application in automotive gears has been dispute due to concerns about load-bearing capacity. However, the advantages of low temperature, low distortion, and reduced processing steps have led to wider application in recent years.
Nitriding Method | Advantages | Limitations |
---|---|---|
Gas Nitriding | Low cost, simple process | Thin nitrided layer, limited application under heavy loads |
Ion Nitriding | Shorter treatment time, reduced distortion, uniform nitrided layer | High investment, technical complexity |
2.5 Induction Hardening
Induction hardening is widely used due to its high efficiency, low distortion, environmental friendliness, and ease of automation. However, as requirements for gear strength and reliability increase, issues related to gear strength, load-bearing capacity, and service life have not been fully resolved.
Induction Hardening Features | Advantages | Challenges |
---|---|---|
High Efficiency | Fast heating speed | Gear strength, load-bearing capacity, and service life issues |
Low Distortion | Minimal deformation | Limited gear modulus range |
3. Emerging Heat Treatment Technologies for Automotive Gears
To further improve the quality of gear heat treatment and meet the needs of the automotive gear industry, China has introduced and developed a number of emerging heat treatment technologies.
Emerging Technology | Description | Application Status |
---|---|---|
Laser Quenching | Small deformation, fine and uniform grains in the quenched area | Widely used in automotive, metallurgical, and heavy machinery industries |
Low-pressure Vacuum Carburizing | Surface not oxidized, environmentally friendly, improved deformation control | Gradually adopted in the automotive industry in developed countries |
BH Accelerated Carburizing | Enhances carbon absorption at lower temperatures | Issues with pipeline clogging and carbide morphology control |
Rare Earth Co-infiltration | Micro-alloying effect, refines microstructure, improves performance | Improves uniformity of composition, extends mold life |
Liquid Oxy-nitriding Surface Strengthening | Significantly improves surface hardness, wear resistance, corrosion resistance, and fatigue resistance | Widely used in automotive, locomotive gear, and other industries |
4. Trends in Automotive Gear Heat Treatment Processes
The development of automotive gear heat treatment processes not only emphasizes stricter quality control but also emphasizes energy saving and environmental protection. The overall trend is towards high quality, low energy consumption, environmental protection, and intelligence.
Trend | Description |
---|---|
High Quality | Research on deformation and control technologies, development of new steel materials and precision gears |
Low Energy Consumption | Development of advanced heat treatment equipment, energy-saving materials, and net-shape forming technology |
Environmental Protection | Development of new heat treatment processes such as low-pressure vacuum carburizing, dual-frequency induction quenching, and ion nitriding |
Intelligence | Computer-sensor-intelligent database to form the core of intelligent heat treatment, including automatic process generation, closed-loop control, quality prediction, fault diagnosis, and adaptive respons |
In summary, significant progress has been made in the heat treatment processes for automotive gears, with a focus on improving quality, reducing energy consumption, protecting the environment, and achieving intelligent control. With the continuous development of gear manufacturing technology, the heat treatment processes for automotive gears in China are expected to further advance, gradually narrowing the gap with international advanced levels.