In terms of spiral bevel gear theory, in the 1940s and 1950s, scientists such as e.wildhaber and m.l.baxter made a lot of basic research on spiral bevel gears. As an old gear manufacturer, Gleason company of the United States finally launched a complete set of technical system applied to actual production and use in 1960 by using these theoretical achievements and through continuous test and verification. Later, Oerlikon of Switzerland and Klingelnberg of Germany also successively formed their own technical standards. The difference is that the three companies adopt different tooth systems in their respective technical systems. Gleason adopts circular arc tooth system for spiral bevel gears, which requires multiple tool withdrawal and tool surrender in the tooth cutting process, while Oerlikon and Klingelnberg adopt cycloid tooth system, which can realize continuous cutting. The technical systems of the three gears are independent of each other.
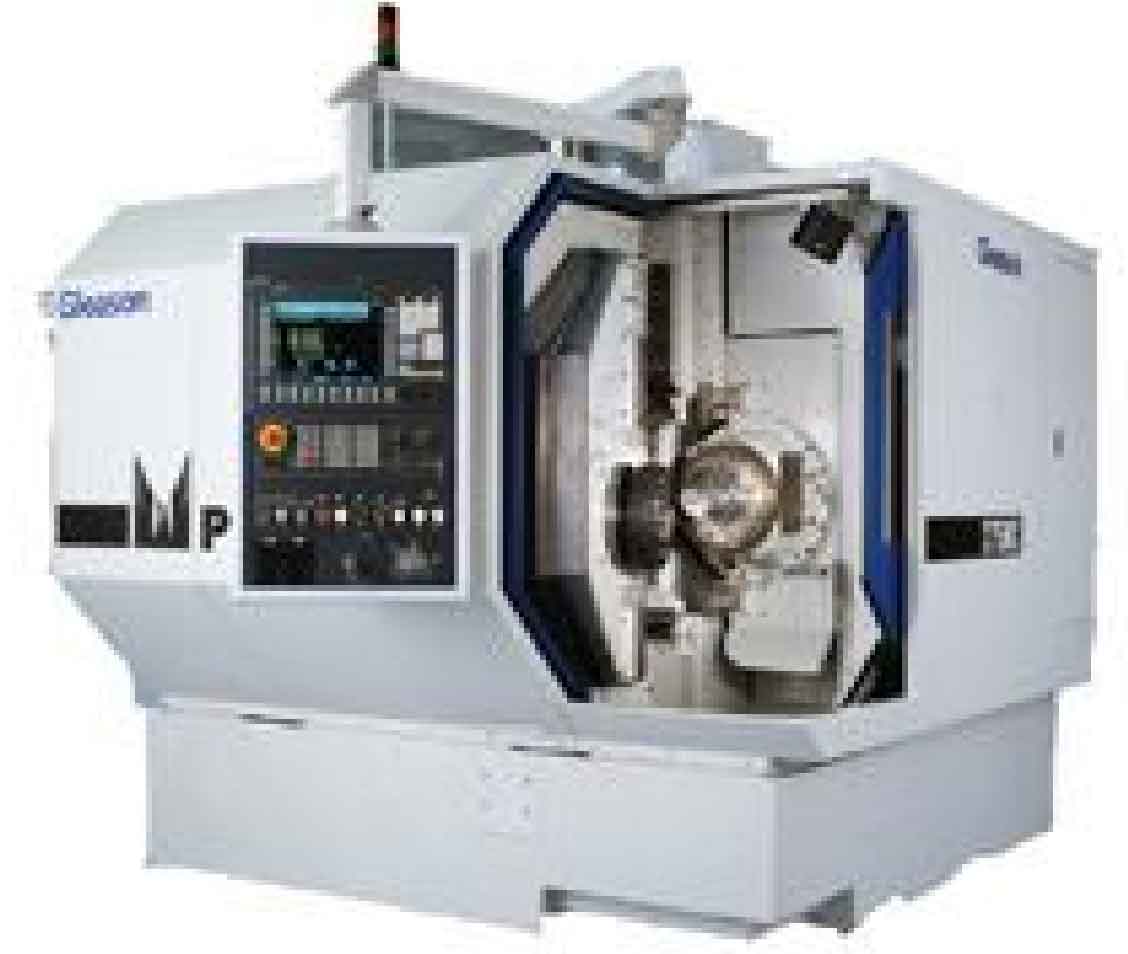
The meshing theory of Gleason spiral bevel gear is the local conjugate principle, that is to say, the surface contact of large and small gear teeth is not line contact or surface contact, but a point contact. In practical use, due to the existence of material deformation, the gear tooth surface contact is an ellipse. The idea is to first cut out the gear tooth surface, select a point on the gear surface, and calculate the tooth surface curvature parameters of the big wheel at this point, then use the gear meshing principle to calculate the position of the small wheel tooth surface point conjugate with the big wheel at this point, combined with the relationship between the big tooth surface curvature and the point contact tooth surface curvature, to obtain the theoretical value of the tooth surface curvature of the small wheel at the contact point, and on this basis, calculate the tooth cutting processing parameters of the small wheel.
In 1978, Gleason published the principle and method of tooth contact analysis (TCA). TCA can simulate the gear meshing process on the computer without considering the deformation of the tooth surface after bearing and various errors. The locus and position of the tooth surface contact spots and the tooth surface contact area can be obtained. This method effectively shortens the processing and adjustment cycle of spiral bevel gears and greatly improves the production efficiency. When higher requirements are put forward for spiral bevel gears, such as controlling the noise and vibration in the process of gear pair transmission, the general TCA method has been difficult to meet the requirements.
In 1981, krezer published the principle and method of loaded tooth contact analysis (LTCA) of spiral bevel gears. This method considers the tooth surface deformation after the load. According to the shape and position of the contact spots and the motion curve, the magnitude of the gear vibration can be qualitatively determined. In recent years, the finite element method has been applied to load contact analysis, and soon became the focus of research. The local synthesis method proposed by Litvin adjusts the processing parameters according to the gear loading contact analysis results, which has a good effect on the noise reduction and vibration reduction of the gear pair.