At first, China did not have its own spiral bevel gear technology system, and the spiral bevel gear technology applied after the founding of new China was mainly Gleason spiral bevel gear technology of the United States. However, due to the technical blockade of Gleason company, China can only get Gleason’s standard calculation card, and the theoretical basis behind the calculation card is not understood at all. In the 1970s, the former Ministry of machinery industry organized experts, scholars and enterprises to tackle key technical problems in order to break the technical blockade of spiral bevel gears abroad, studied the design and processing principle of spiral bevel gears, and listed Gleason spiral bevel gear technology as a key scientific research project to realize the localization of spiral bevel gear processing and manufacturing technology. Through unremitting efforts, they discovered the compilation principle of the Gleason calculation card and deduced the theoretical calculation formula behind it, which made the Gleason calculation adjustment card less mysterious. In addition, they pointed out the theoretical errors and defects in the original Gleason calculation card and improved them. On this basis, they established a theoretical and technical system for the design and processing of spiral bevel gears in China.
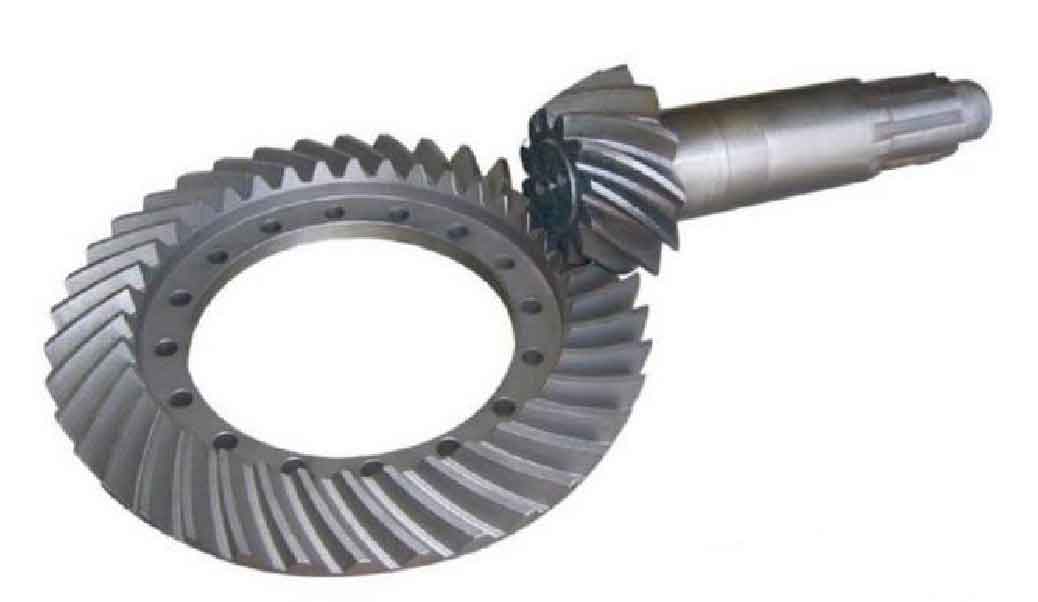
The initial study of spiral bevel gears was carried out from a mathematical point of view. The relative differential method is the basic method for the study of complex surfaces. The famous mathematician Mr. yanzhida used this method to study the conjugate surfaces and derived the calculation formula of induced normal curvature, which provides a strong theoretical basis for solving the processing parameter calculation method and the processing parameter adjustment principle of Gleason spiral bevel gear.
Local conjugation is the tooth surface contact form of Gleason spiral bevel gear, and it is also the theoretical basis for tooth surface contact analysis (TCA) calculation. Professor zhengchangqi deeply studied Gleason’s local conjugate principle and derived the relevant calculation formulas for TCA analysis.
Professor Zeng Tao gave the structure of spiral bevel gear processing machine tool suitable for production by studying the principle of equidistant conjugate surface. He found that the formula shown in the processing adjustment card of Gleason machine tool was obtained after various deformation decomposition. After re combination and simplification, a complete calculation adjustment card can be obtained. He also sorted out the calculation process of TCA, The complete design and machining process of spiral bevel gear is obtained.
Professor wuxutang has made a comprehensive exploration on the relevant processing technology principle of hypoid gear, deduced the calculation adjustment card of machine tool, and obtained fruitful theoretical research results.
Professor dongxuezhu studied the tooth surface processed by various processing methods of spiral bevel gears, improved the processing parameter adjustment algorithm to make it simpler and more suitable for the processing parameter adjustment calculation in actual production, and successfully applied the algorithm to the machine tool processing adjustment calculation of spiral bevel gears, providing theoretical guidance for the processing parameter adjustment of spiral bevel gears in actual production.
The local synthesis method proposed by Professor Litvin may have defects in the contact characteristics far away from the reference point. Wuxutang and Wang Xiaochun analyzed the gear meshing process and proposed a method to improve the defects of the local synthesis method by controlling the third-order contact performance of the tooth surface. However, this method can only be limited to the meshing characteristics near the studied point, and the meshing characteristics of the entire tooth surface contact cannot be effectively controlled.
In view of the deficiency of this theory, tianxingbin et al. Extended the local synthesis method by selecting not only one point but multiple reference points on the tooth surface. If the control area of these reference points can be spread over the whole tooth surface, the deficiency of the local synthesis method can be effectively improved. Practice has proved that this is a feasible method.
Professor zhengchangqi, based on TCA method, combined with transmission angle displacement coordination principle and load equivalent installation adjustment value theory, studied and deduced the calculation principle and related formulas of gear load contact analysis (LTCA).
Professor liangguiming and others put forward a theoretical method to select the modification coefficient according to the meshing performance of spiral bevel gears, which broke the traditional gear modification design idea for the first time at home and abroad.
Wuxutang, wuxuncheng, etc. put forward an active design method based on the meshing characteristics of spiral bevel gear tooth surface, but the tooth surface designed by this method has many limitations. The biggest limitation is that this kind of tooth surface processing can not be processed by ordinary spiral bevel gear processing machine tools, and can only be realized on spiral bevel gear NC machine tools that can realize free form motion control.
Sundianzhu, dongxuezhu, etc. used the techniques of three coordinate measurement and surface reconstruction to obtain the real tooth surface and establish the real wheel blank model, and analyzed the meshing characteristics of the real tooth surface, providing a method guidance for the real tooth contact analysis (RTCA) of spiral bevel gears.
Professor fangzongde and others combined the characteristics of the finite method and the flexibility matrix method to improve the analysis principle and method of LTCA, which greatly reduced the calculation amount of LTCA and significantly improved the calculation efficiency. This algorithm has also become an effective tool for load-bearing contact analysis of spiral bevel gears.
Professor dengxiaozhong and others used the Hertz stress calculation principle of spatial curved surface to obtain the position of the maximum contact stress on the tooth surface, and improved the calculation accuracy by using various methods. In gear strength calculation, the root stress is usually calculated by equivalent gear, and the accuracy of calculation results is not high. Chen Liangyu and others obtained the accurate root stress of spiral bevel gear by using the finite element analysis software ANSYS. Lirunfang combined the tooth contact analysis with computer graphics, and compiled the contact finite element analysis software of spiral bevel gear for strength calculation.
Professor wangsanmin and others have considered the machining error and load-bearing deformation of spiral bevel gear, combined with the flexible multi-body theory, established the mathematical model of spiral bevel gear tooth surface with machining error, and studied the influence of various deformations and errors on the tooth surface accuracy and its laws, which is also the prerequisite for active gear design. On the dynamics of spiral bevel gears, many scholars, such as Gao Jianping, have made constructive research.