In the process of the above planetary gear mechanism simulation and analysis, the gear ring needs to be generated into a flexible body first because the vibration acceleration signal above the gear ring needs to be collected.
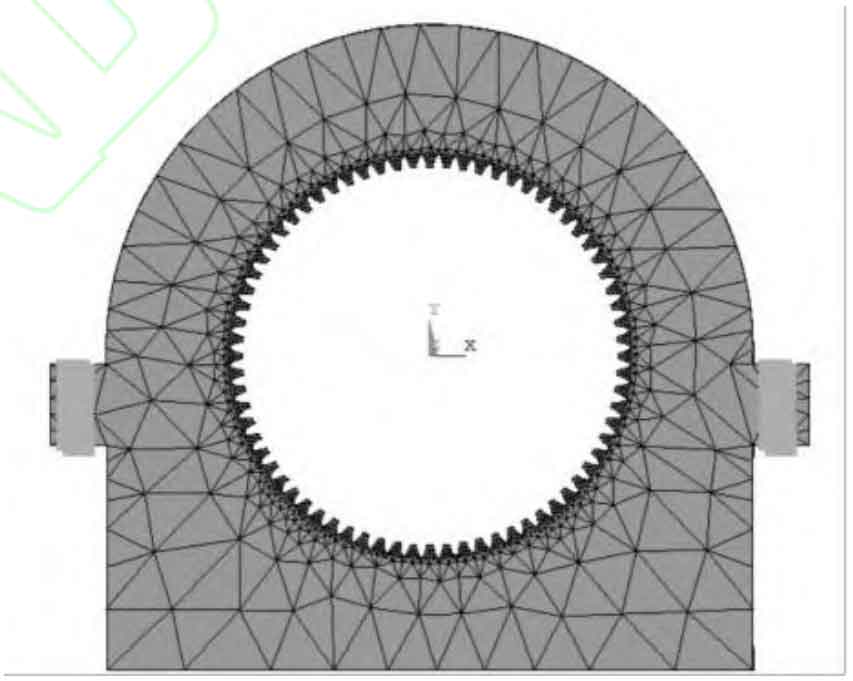
Import the established 3D model of the gear ring into the ANSYS APDL software, and generate the flexible body of the gear ring through the steps of creating elements and materials, meshing elements, etc., as shown in Figure 1.
1. Model import
The author imports the established three-dimensional model of planetary gear mechanism into ADAMS software as a whole, and replaces the ring gear model with the ring gear flexible body to obtain the rigid flexible coupling model of planetary gear mechanism, as shown in Figure 2.
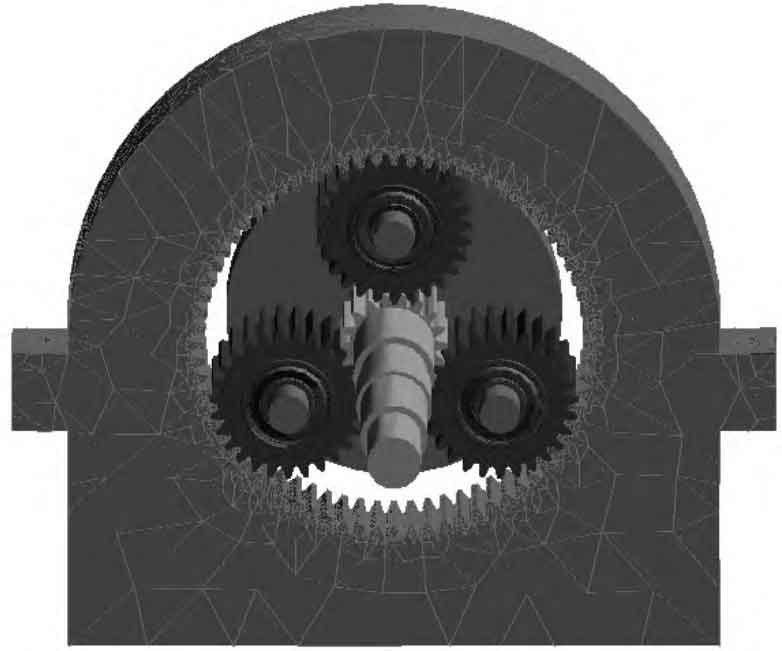
2. Simulation parameter setting
Next, the author sets the simulation parameters of the rigid flexible coupling model of the planetary gear mechanism.
Firstly, the material of the planetary gear mechanism is set as steel, which is consistent with the solid model;
Secondly, set connections between each model. The specific connection settings are as follows:
(1) The sun gear and planet carrier are respectively provided with rotation pairs with the earth;
(2) The 3 planet gears are respectively provided with rotating pairs with the planet carrier;
(3) A fixed pair is set between the gear ring and the earth.
Thirdly, the shock function method is used to add contact, and the specific settings are as follows:
(1) The 3 planet gears are respectively in contact with the ring gear and the sun gear;
(2) Add contact between the inner ring and outer ring of the bearing and the planet carrier and planet gear respectively.
Finally, a rotary drive is added to the sun gear of the gear unit.
3. Layout of measuring points
Taking the fault diagnosis experimental platform of automobile planetary gearbox in the laboratory as the research carrier, and the vibration acceleration signal above the gear ring as the research object, the layout of measuring points is carried out.
Therefore, the author chooses to add a Mark point at the flexible node above the gear ring here, and completes the signal acquisition by reading the Mark point information.
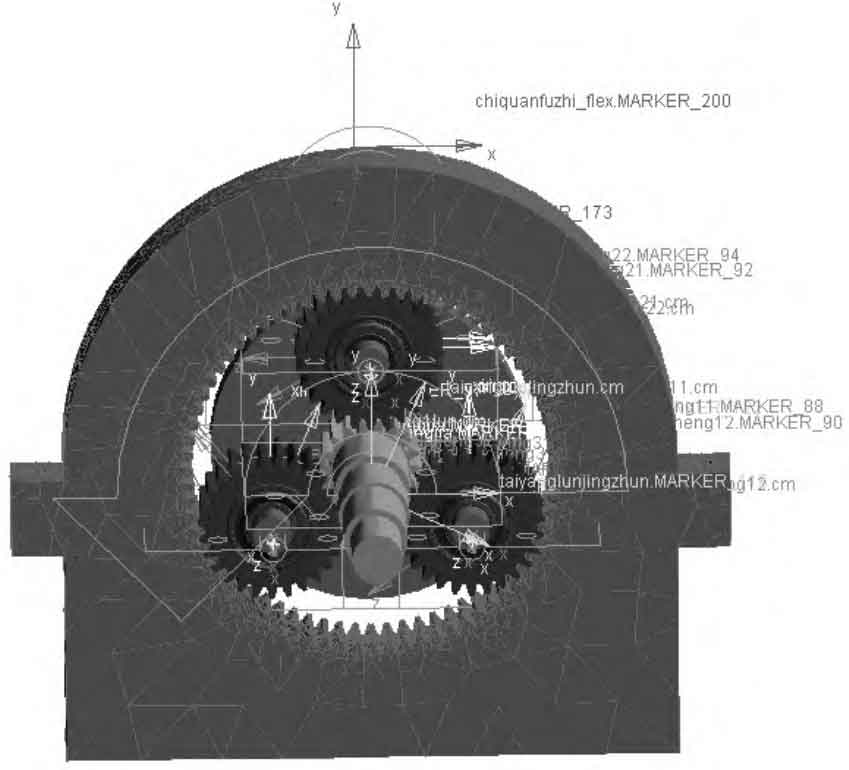
Mark point position of gear ring is shown in Figure 3.
4. Model validation
The author sets the planetary gear speed at the rotary drive as 3600 °/s, the load as 100 N · m2, the number of steps as 30720, and the setting time as 3s to conduct rigid flexible coupling dynamics simulation.
The speed curve of the planet carrier of the planetary gearbox is obtained through simulation, as shown in Figure 4.
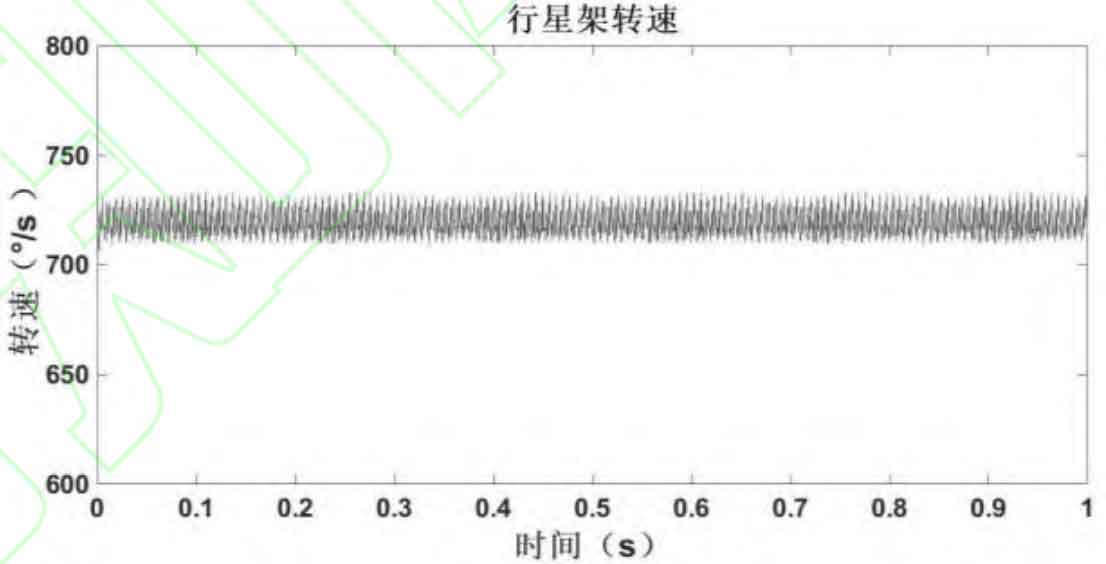
It can be seen from Figure 4 that the average value of the planet carrier of the planetary gearbox is 720 °/s, which meets the requirements of the transmission ratio, thus verifying the accuracy of the rigid flexible coupling dynamic model of the planetary gearbox.