The hot precision forging lubricant shall have the following advantages:
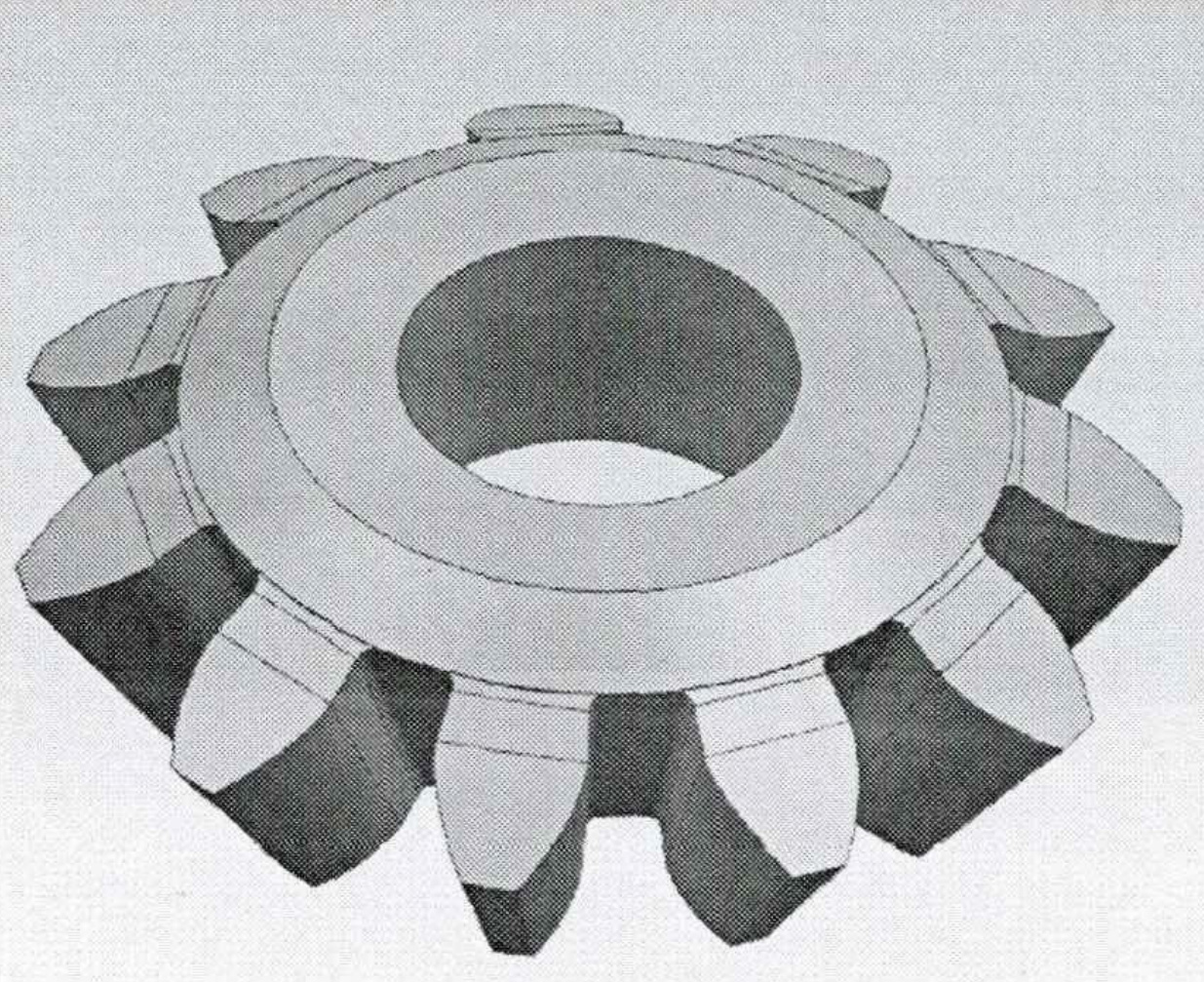
(1) It has good lubricity in the forging temperature range. The forging temperature of bevel gear forgings is generally 800-1200 ℃, and the die temperature is generally 200-500 ℃. The lubricant should isolate the bevel gear forging from the die, avoid direct contact with the die when the metal is deformed, reduce the friction when the metal flows, reduce the die wear, reduce the forging force, and improve the metal filling performance.
(2) Good demoulding performance. That is, at the end of forging, the bevel gear forging can be separated from the die in time, and the heat of the bevel gear forging can be reduced to the die, so as to prolong the service life of the die and improve the production efficiency.
(3) It has good cooling and thermal insulation performance. During forging, the surface temperature of the cavity rises sharply due to the contact between the bevel gear forging blank and the cavity and the friction heat caused by metal deformation and rapid flow. In order to reduce the heat transfer to the die, the lubricant is required to have good thermal insulation performance for bevel gear forgings.
(4) Good high temperature lubricity and molding ability. In the hot die forging process of bevel gear, the die temperature can reach more than 500 ℃. In order to prevent die sticking caused by lubrication failure, the lubricant is required to have a good role in wetting the die at high temperature, so that a uniform lubrication film can be formed on the surface of the hot die. Film forming and high-temperature wettability are not easy to meet at the same time, because the lubricant generates a layer of air cushion between the blank and the die in the forging process of bevel gear, so it is easy to demould after forging. At high temperature, there are many substances that produce gas, and the generated pressure is large, so the corresponding wettability is poor.
(5) It has good suspension dispersion and sprayability. For the convenience of use, the solid particles in the lubricant shall not be easy to settle and agglomerate, and the thin layer of lubricant shall be evenly distributed in the mold cavity.
(6) After the forging of bevel gear, the lubricant should not leave residue in the mold cavity, or the residue left is very small and easy to remove. Water soluble graphite was selected as lubricant for forming spur bevel gear by “one fire two forging” process.