Currently, the only mechanical transmission gear milling machine available is the No. 102 small module gear milling machine from Gleason Company in the United States. When machining large wheels, the 1:1 roll ratio method is used to achieve large wheel cutting processing, but the large wheel rotates during processing. The processing of the small wheel adopts a 30 ° spindle inclination method. Other domestic mechanical transmission type small module spiral bevel gear milling machines cannot perform semi hobbing processing. Only the rolling cutting method can be used, that is, the double double sided method. All large and small wheels are processed using the rolling cutting method, regardless of the transmission ratio or pitch cone angle. All the rolling cutting methods are used.
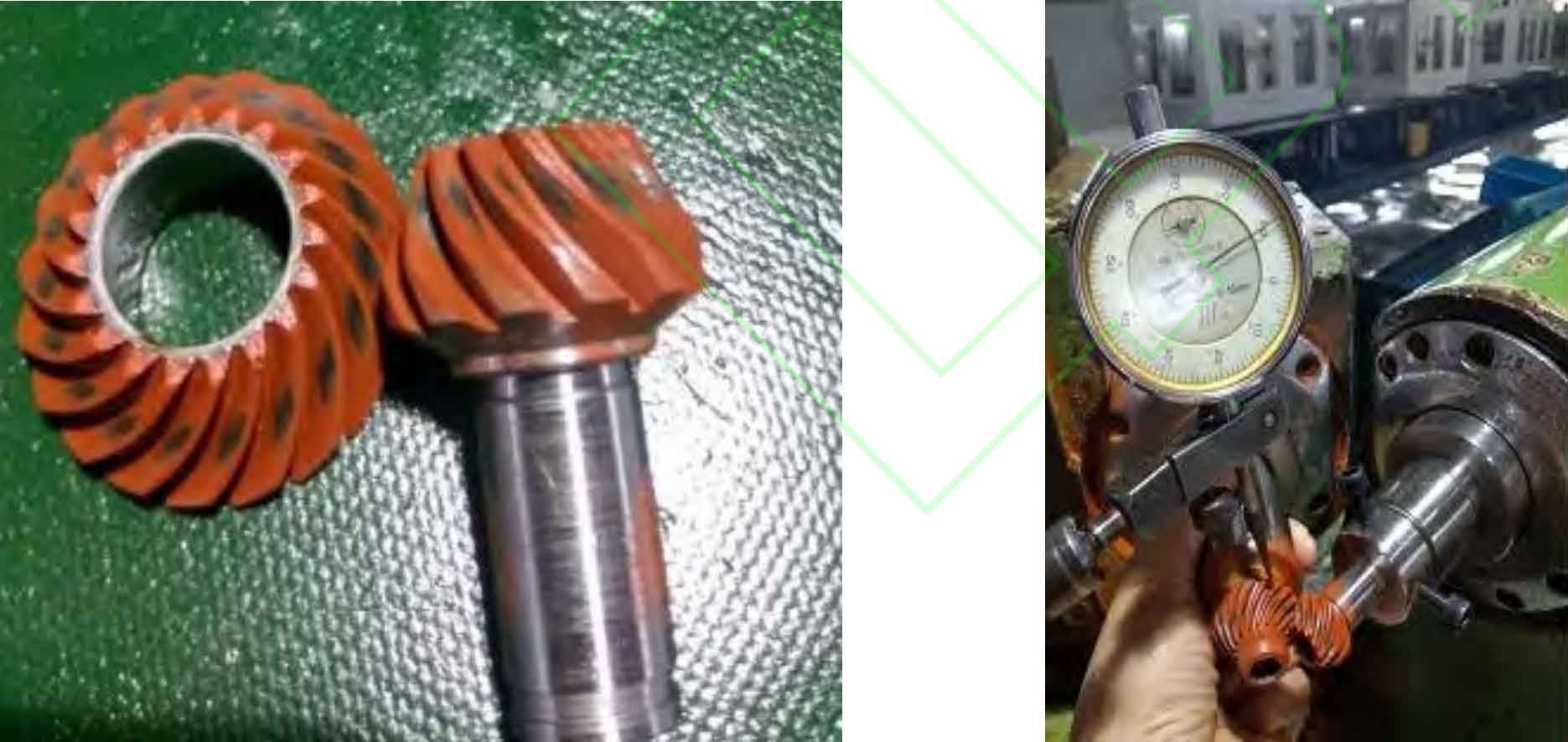
The domestically manufactured CNC gear milling machine with good rigidity has been able to meet the requirements of semi hobbing. The big wheel cutting method is used for machining. During machining, the big wheel is fixed and does not move. After the cutter gradually cuts into the full tooth, it quickly retracts and indexes, and then continues to process the next tooth slot until all the teeth slots have been cut. The cut is performed from the Z axis. Reducing the cutting speed of the big wheel instead of uniform cutting speed can greatly improve production efficiency and tool life. Therefore, Gleason’s No.102 small module gear milling machine was used in this test.