Semi digital control of spiral gear shaping
The so-called semi digital control refers to the use of digital differential chain to replace the traditional spiral guide rail in the processing of spiral gears, and to keep the mechanical structure of other parts unchanged. Therefore, in the basic principle of spiral gear forming, it is the same as the ordinary spiral gear shaper.
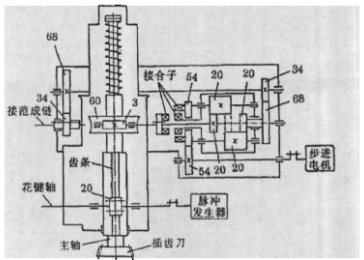
The figure is the transmission system diagram of numerical control differential chain. The main motion transmission chain (not shown in the figure) makes the spline shaft rotate clockwise and anticlockwise, and drives the main shaft of the gear shaper to move up and down through the spline shaft gear and rack. The pulse generator connected with the spline shaft can accurately detect the up and down moving distance of the main shaft of the gear shaper. The pulse signal sent by the pulse generator is input into the numerical control device. After the numerical control device isolates and amplifies the pulse signal, it drives the stepping motor. The differential mechanism makes the normal rotation and additional rotation of the main shaft of the gear shaper superposed together, and then it is transmitted to the main shaft of the gear shaper through the worm and worm gear, So as to realize the additional rotation of the main shaft of the gear shaper.
The main features of the scheme are low cost, simple control mode, and the control principle is completely consistent with the common spiral gear shaper. When machining the helical gear, it is not necessary to attach the spiral guide rail, but only to set the parameters. If machining the gears with different helical angles, the parameters can be changed. When processing the common spur gear, cut off the power supply of the stepping motor, and then the spur gear can be processed. At present, the vast majority of gear machine tools in China are of traditional mechanical type, so the method is simple in principle, low in transformation cost and convenient in machine maintenance, so it has certain practical significance.
The biggest disadvantage of the semi digital transformation scheme is that it does not disconnect the complex transmission chain, the transmission components still rely on the change gear to distribute power from the main transmission, and it does not solve many problems such as the complex structure of the machine tool, the difficulty in design, the inconvenience in maintenance and so on. Therefore, this scheme can only be used as a transitional solution, and can not realize the full digital control of spiral gear machining.
Digital control of gear shaping
The whole number controlled machining of spiral gear means that the complex transmission chain in the traditional machine tool is cancelled, each end actuator has its own driving device, and each movement in the gear shaping machining is uniformly scheduled by computer program, and finally the processing of spiral gear is completed.
The key to the principle of total controlled machining is to realize the relative motion relationship between the tool and the workpiece. The current realization of CNC slotting of spiral gear only uses CNC program to simulate the movement form of the original mechanical slotting machine tool, that is, only uses the additional pulse encoder to detect the up and down linear displacement of the slotting cutter in real time, and controls the additional rotation of the slotting cutter by corresponding algorithm according to the relevant parameters of the workpiece gear. This method only uses the numerical control program to replace the spiral guide rail, and the advantage of the numerical control machine tool is far from being exerted. Therefore, in order to realize the full digital control of spiral gear shaping, we must jump out of the case of “additional rotation”, and think about this problem from a new perspective. This paper uses the non differential method as the theoretical basis to realize the full digital control of spiral gear shaping.