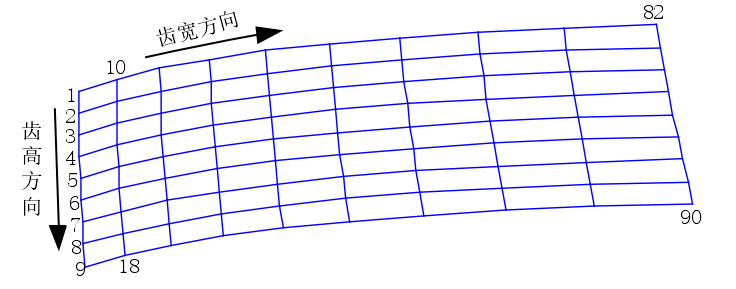
90 points are selected to reflect the overall error of the tooth surface. 9 points are evenly distributed in the tooth height direction and 10 points are distributed in the tooth width direction. The 90 points are connected in turn to form a grid of 9 10. The specific grid division method and grid point distribution are shown in the figure
Firstly, the normal vectors of all grid points are obtained. According to the disturbance of the machine tool in the process of machining, different machining parameters are given to analyze their sensitivity to tooth surface error. Here, the variation range of displacement parameters is + 0 ~ 1 mm, the variation range of angle parameters is + 0 ~ 1 ° and the disturbance of rake angle and offset angle is + 0 ~ 5 °.
The detailed steps to solve the tooth surface error sensitivity are as follows:
The first step is to divide the mesh evenly according to the rotation projection, and map it to the space tooth surface. The position vector of the selected point is the coordinate of the tooth surface point, and the normal vector of the point can be obtained according to the cross product of the position difference of the adjacent points;
The second step: according to the variation range of different machining parameters, the tooth surface error of each tooth surface mesh point for different machining parameters is calculated;
The third step: draw the error curve of all mesh points on the tooth surface with each machining parameter, and fit all discrete results within the parameter disturbance range into quadratic polynomial by least square method, and analyze the sensitivity of tooth surface error to each machining parameter by polynomial coefficient.