Before ring rolling, the formed spiral bevel gear blank has to go through four steps: pier roughening, pre punching, punching and shape correction. Because the above forming technology has been very mature in the actual production operation, this paper will not carry out simulation analysis.
This paper mainly analyzes and explains the numerical simulation process of ring rolling process. Through the post processor of DEFORM-3D simulation software, it summarizes the geometric dimensions and stress-strain distribution of formed rings in the ring rolling process. Three groups of ring blanks with different sizes are selected to form spiral bevel gear blanks with high quality and precision by changing the size of ring blanks, so as to achieve the purpose of process optimization. The simulation results of ring rolling forming are only used as the basis of qualitative analysis, because some objective factors often exist in the actual production can not be considered by the simulation software, so the specific data of the simulation results can not be used as the relevant results of real production.
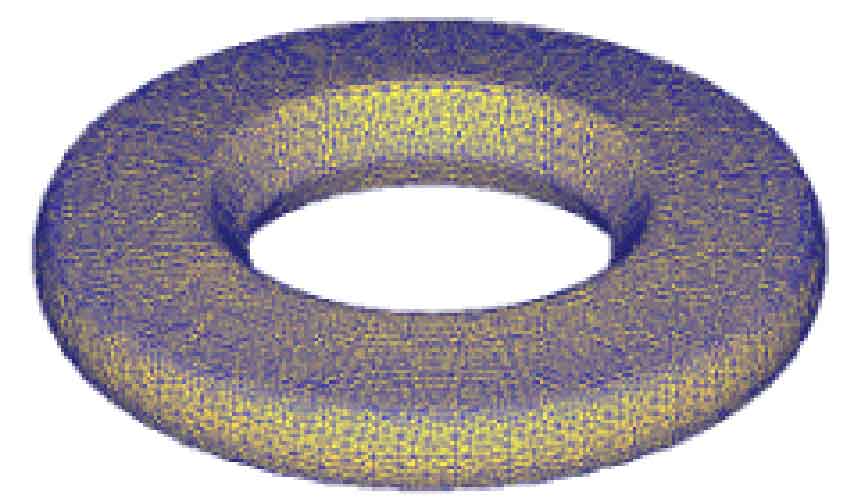
In ring rolling forming, while the simulation results are calculated accurately, the operation efficiency should be ensured. Therefore, the mesh of spiral bevel gear blank can not be divided too much or too little. The mesh of annular blank is divided at about 100000, and the division effect is shown in the figure. Due to the heat conduction between the spiral bevel gear blank and the die, the die also needs grid division. The grid division of the driving roll is about 100000 and the grid division of the core roll is about 50000.
The simulation boundary conditions of ring rolling mainly set the movement direction of the spiral bevel gear blank. In the process of ring rolling, the spiral bevel gear blank will shake and twist in the y-axis direction when rotating. In order to avoid this phenomenon, the speed of the spiral bevel gear blank in the y-axis direction is set to 0. At the same time, the spiral bevel gear blank, drive roll and core roll are set with heat exchange boundary conditions.