Grinding is the final and critical step in the manufacturing of spiral bevel gears, which are widely used in heavy-duty vehicle transmissions due to their high torque capacity and smooth meshing. The surface topography generated during grinding directly impacts wear resistance, fatigue life, and noise performance. This study establishes a comprehensive model to simulate the grinding surface morphology of spiral bevel gears by analyzing abrasive grain trajectories and wheel topography characteristics. Experimental validation further investigates the effects of key grinding parameters on surface quality.
1. Kinematic Analysis of Abrasive Grain Trajectories
In conventional surface grinding, the motion trajectory of a single abrasive grain is governed by the rotational speed of the grinding wheel and the translational velocity of the workpiece. For spiral bevel gears, the kinematic relationship becomes more complex due to the curved tooth surfaces and the cup wheel’s enveloping motion. The trajectory equation for an abrasive grain in spiral bevel gear grinding is derived as:
$$
\begin{aligned}
x’_G &= x_G + \frac{v_w}{n_s} \left( \frac{30\phi}{\pi} \right)(i-1) \\
z’_G &= z_G + B_0 + B_1x_G + B_2x_G^2
\end{aligned}
$$
where \( v_w \) represents the generating speed, \( n_s \) is the wheel rotational speed, and \( B_0 \), \( B_1 \), \( B_2 \) are polynomial coefficients describing the spiral tooth curvature.
2. Grinding Wheel Topography Modeling
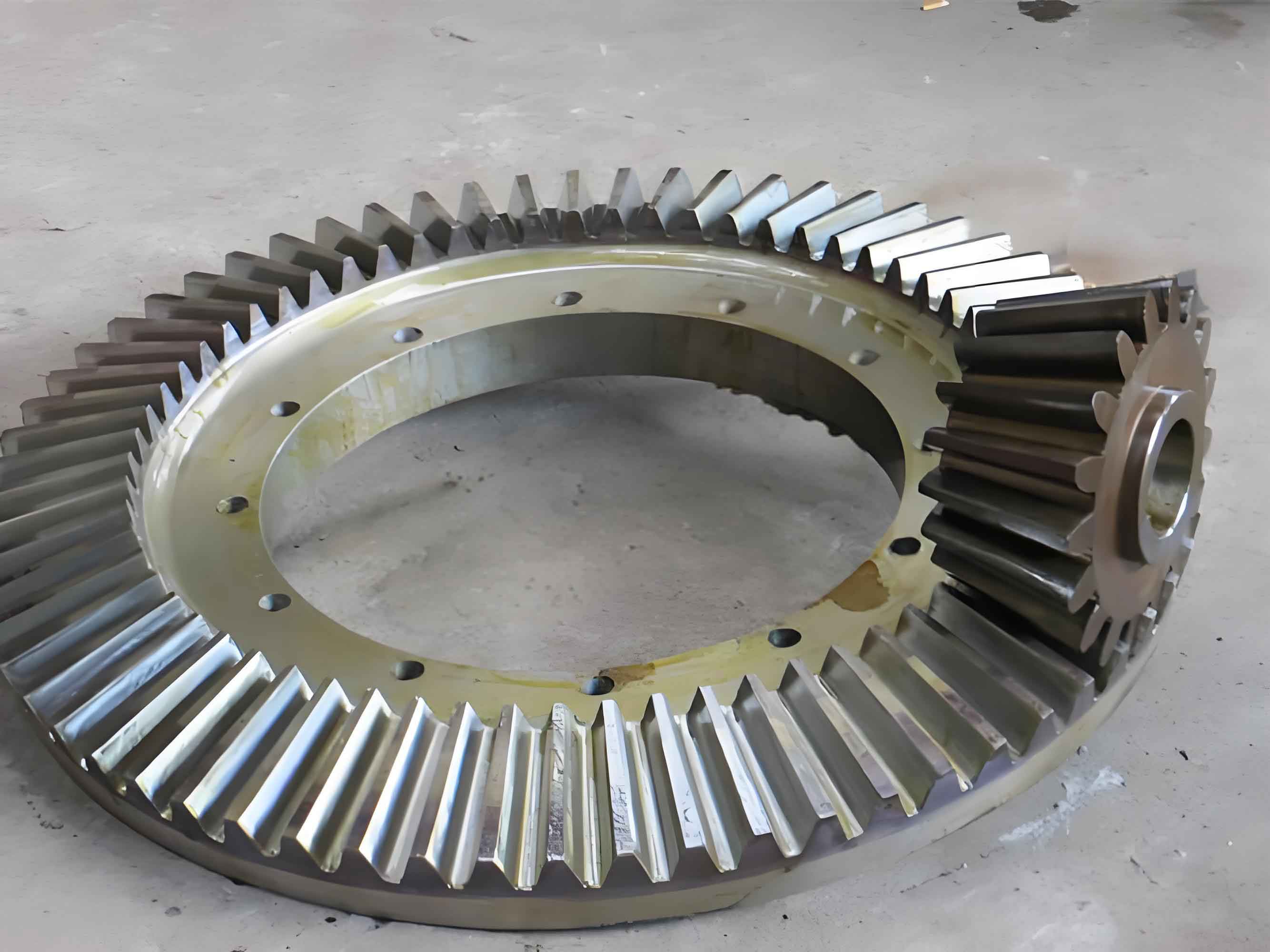
The wheel topography significantly influences surface generation. Key parameters include:
Parameter | Expression |
---|---|
Maximum grain diameter | $$ d_{gmax} = 1.52M^{-1} $$ |
Average grain diameter | $$ d_{gavg} = 68M^{-1.4} $$ |
Grain height distribution | $$ f(h_i) = \frac{1}{\sigma\sqrt{2\pi}} \exp\left(-\frac{(h_i-\mu)^2}{2\sigma^2}\right) $$ |
where \( M \) denotes abrasive grit size, \( \mu = d_{gavg} \), and \( \sigma = (d_{gmax}-d_{gavg})/3 \).
3. Surface Generation Mechanism
The final surface topography results from the superposition of individual grain trajectories. For spiral bevel gears, the residual height at any point \( (m,n) \) on the tooth surface is determined by:
$$
g(m,n) = \min\left[z’_G(i,j)\right]
$$
where \( z’_G(i,j) \) represents the minimum z-coordinate from all overlapping grain paths at location \( (m,n) \).
4. Experimental Validation
Grinding tests were conducted on a Gleason-600G machine using SG cup wheels. Key process parameters included:
Parameter | Range |
---|---|
Wheel speed (\( v_s \)) | 10-25 m/s |
Generating speed (\( \omega \)) | 6-14°/s |
Depth of cut (\( a_p \)) | 0.01-0.09 mm |
Surface roughness measurements revealed:
$$
R_a = 0.12 \left(\frac{v_s^{0.3}}{a_p^{0.5}\omega^{0.2}}\right)
$$
showing that increasing wheel speed and generating speed improves surface finish, while larger depths of cut degrade it.
5. Parametric Effects on Bevel Gear Surface Quality
The interaction between grinding parameters and surface topography was analyzed through both simulation and experimentation:
Parameter | Effect Mechanism |
---|---|
Wheel speed (\( v_s \)) | Higher speeds increase active grains/mm², reducing residual height |
Generating speed (\( \omega \)) | Faster generating motion decreases overlap ratio, creating shallower grooves |
Grit size (\( M \)) | Finer grits (higher M values) produce more uniform grain distribution |
For spiral bevel gears, the non-linear motion trajectory creates varying interference patterns along the tooth profile, requiring adaptive parameter optimization.
6. Conclusion
The established model effectively predicts spiral bevel gear grinding surface topography by considering both kinematic trajectories and stochastic wheel topography. Experimental validation confirms that:
- Surface roughness decreases by 32% when increasing wheel speed from 15 to 25 m/s
- Optimal generating speed ranges between 10-12°/s for typical aerospace-grade bevel gears
- Using 180-grit wheels reduces \( R_a \) by 45% compared to 46-grit wheels
This methodology provides critical insights for optimizing spiral bevel gear grinding processes in heavy-duty transmission applications.