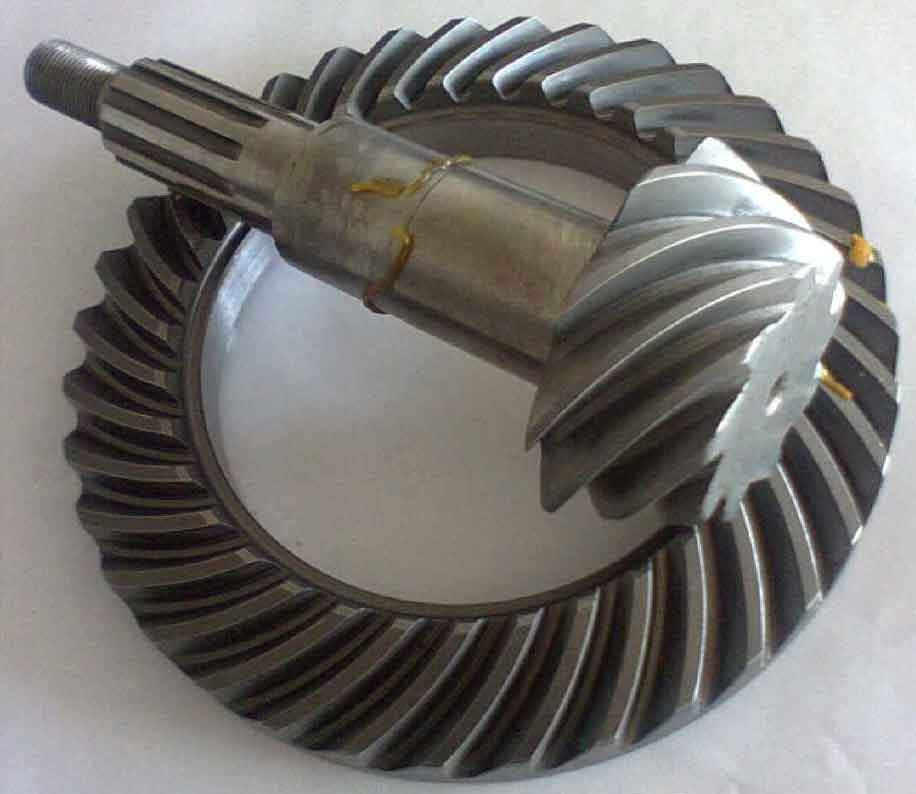
Taking the forging process of driving and driven spiral bevel gears as the research object, the forging process of gear blanks is numerically simulated with the help of the finite element numerical simulation software from-3d. The main work and conclusions are as follows:
- Multi-step analysis method for numerical simulation of gear blank forging process is proposed. The finite element software from-3d is used to analyze the upsetting process and die forging process of driven spiral bevel gear blank, and the drawing process and die forging process of driving spiral bevel gear blank. The metal flow law, the equivalent stress, strain and temperature distribution, the stroke load curve and stroke energy consumption curve of the forging process were obtained. The results show that the equivalent stress and strain of forgings at some steps are larger and the temperature is higher, indicating that it is difficult for metal to flow at these steps. The numerical simulation results are compared with the real object to verify the correctness of the numerical simulation.
- According to the distribution of equivalent stress, strain and temperature obtained by numerical simulation, the die structure is improved where there will be large stress, strain and high temperature. After the improvement of the die, the forging process was simulated again, and the numerical simulation results after the improvement of the die were obtained and compared with the numerical simulation results before the improvement. The results show that the metal flow is improved after the improvement of the die. The numerical simulation results can provide a basis for the design and improvement of the die.
- The forging process of driving and driven spiral bevel gear blanks is numerically simulated when the initial forging temperature is 1000 ° C, 1050 ° C and 1100 ° C and the friction coefficient is 0.3 and 0.7 respectively, so as to study the influence of different initial forging temperature and friction coefficient on the forging process. The equivalent stress-strain values, stroke load curves and energy consumption curves of the forging process were compared under different initial forging temperatures and different friction coefficients of the driving and driven wheels. The results show that when the friction coefficient is the same, the higher the initial forging temperature is, the smaller the stress-strain value is, the lower the forming load and forging energy consumption are, and the better the forming effect is. When the initial forging temperature is the same, the smaller the friction coefficient is, the smaller the stress-strain value is, the lower the forming load and forging energy consumption are, and the better the forming effect is. Therefore, it is necessary to add lubricant in the forging process, and aqueous graphite can be selected as the lubricant.
- The original free forging process in the forging process of the driving spiral bevel gear blank will lead to the bending of the final forging. The extrusion forming method is proposed to replace the original free forging process to draw the long bar. The extrusion process is numerically simulated by using the finite element software defram-3d. The blank shape, stress, strain and temperature distribution after extrusion are obtained. Combined with the die forging process of the driving wheel, the multi-step analysis is carried out. The extrusion method solves the problem of forging bending, but the extrusion method has the problems of low production efficiency and high energy consumption. The spinning method is also proposed. A spinning device is designed for spinning forming. The geometric model of the spinning device is established by using the Software Solidworks, and the spinning process is numerically simulated by using the finite element software ABAQUS. The blank shape, stress nephogram and strain nephogram after spinning are obtained, The feasibility of using spinning forming method instead of cutting block free forging process was verified. The energy consumption of spinning forming is compared with that of extrusion forming. Spinning forming saves energy than extrusion forming. The design of the spinning device has submitted a patent application.
- The relationship between initial forging temperature and forging energy consumption is studied. The numerical simulation results show that there is little difference in forging energy consumption when the initial forging temperature is in the range of 1000-1100 ° C. The difference of forging energy consumption at different initial forging temperatures is much smaller than the difference of heat required for heating to different initial forging temperatures. Therefore, in the range of 1000-1100 ° C, the higher the initial forging temperature, although it is more conducive to forming, the greater the total energy consumption required for forging.