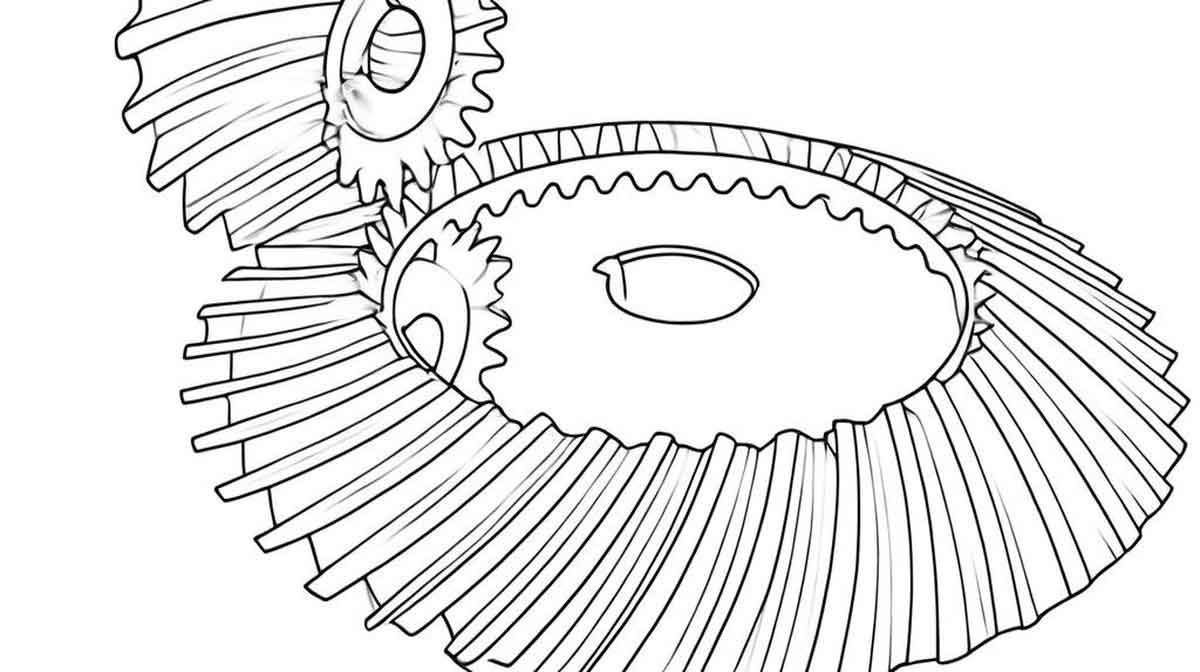
1. Introduction
1.1 Research Background and Significance
Spiral bevel gears are widely used in various mechanical equipment due to their high load-bearing capacity and smooth transmission. The quenching process is an essential step in the manufacturing of spiral bevel gears, which significantly affects the mechanical properties and service life of the gears. However, the traditional quenching process design often adopts a trial-and-error method, which is time-consuming and costly. Therefore, it is necessary to develop an efficient and accurate numerical simulation method for the quenching process to optimize the quenching process parameters and improve the quality of spiral bevel gears.
1.2 Current research status at China and abroad
1.2.1 Quenching Cooling Process Numerical Simulation Research Status
The numerical simulation of the quenching process has been developed since the 1970s. Many scholars have proposed various simulation models and methods, such as the temperature-organization coupling model, the stress model, and the phase transformation dynamics model. These models have been continuously improved and applied to the simulation of various quenching processes. However, most of these methods rely on the heat transfer coefficient, which is affected by many factors and difficult to accurately determine.
1.2.2 Research Status of the Influence of Quenching Medium on the Quenching Cooling Process
The quenching medium has a significant impact on the quenching process. Scholars have studied the flow field of the quenching medium, the heat transfer coefficient, and the cooling characteristics of different quenching media. They have also proposed methods to improve the flow field of the quenching medium and optimize the quenching process.
1.2.3 Research Status of the Heat Treatment of Spiral Bevel Gears
The heat treatment of spiral bevel gears is a complex process that involves many factors such as the material, the geometry of the gears, and the quenching process parameters. Scholars have studied the heat treatment process of spiral bevel gears, including the quenching process, the tempering process, and the surface treatment process. They have also proposed methods to optimize the heat treatment process and improve the quality of spiral bevel gears.
1.3 Research Methods and Contents of This Article
This article proposes a thermo-fluid-solid coupling numerical simulation method for the quenching process. The method couples the fluid domain of the quenching medium and the solid domain of the quenched workpiece and replaces the role of the heat transfer coefficient in the simulation. The article also conducts experimental studies to verify the accuracy of the simulation method. The main research contents include: (1) Research on the numerical simulation method of thermo-fluid-solid coupling during the quenching process; (2) Numerical simulation and experimental study of thermo-fluid-solid coupling during the quenching process; (3) Study on the effect of quenching medium flow parameters on the quenching process; (4) Numerical simulation study of thermo-fluid-solid coupling during the quenching of spiral bevel gears.
2. Numerical Simulation Method of Thermo-Fluid-Solid Coupling during the Quenching Process
2.1 Introduction
The thermo-fluid-solid coupling numerical simulation method for the quenching process couples the fluid domain of the quenching medium and the solid domain of the quenched workpiece. The method uses the finite volume method for the fluid domain and the finite element method for the solid domain. It also uses the wall function and Gaussian integral interpolation method to replace the role of the heat transfer coefficient in the simulation.
2.2 Finite Element-Finite Volume Coupling Heat Transfer Mathematical Model
2.2.1 Flow-Solid Coupling Heat Transfer Model
The flow-solid coupling heat transfer model describes the heat transfer between the fluid and the solid at the interface. The model assumes that the temperature field of the fluid and the solid are coupled and that the heat transfer rate is proportional to the temperature difference and the heat transfer coefficient.
2.2.2 Finite Element-Finite Volume Coupling Calculation Method
The finite element-finite volume coupling calculation method couples the fluid domain and the solid domain. The method uses the finite element method to discretize the solid domain and the finite volume method to discretize the fluid domain. It then uses the interpolation method to couple the two domains and solve the coupled equations.
2.3 Solid Temperature-Stress-Organization Coupling Model
2.3.1 Heat Transfer Model during the Quenching Process
The heat transfer model during the quenching process describes the heat transfer in the solid during the quenching process. The model assumes that the heat transfer in the solid is mainly due to conduction and that the heat source is due to the phase transformation and the latent heat release.
2.3.2 Phase Transformation Model during the Quenching Process
The phase transformation model during the quenching process describes the phase transformation in the solid during the quenching process. The model assumes that the phase transformation is mainly due to the cooling rate and the temperature and that the phase transformation kinetics can be described by the Avrami equation.
2.3.3 Strain Model during the Quenching Process
The strain model during the quenching process describes the strain in the solid during the quenching process. The model assumes that the strain is mainly due to the thermal expansion and the phase transformation and that the strain can be described by the Hooke’s law and the phase transformation plasticity equation.
2.4 Fluid Flow and Heat Transfer Model
2.4.1 Basic Assumptions of Two-Phase Flow
The two-phase flow model assumes that the fluid consists of two phases: a liquid phase and a gas phase. The model assumes that the two phases are in equilibrium and that the volume fraction of each phase can be calculated based on the pressure and the temperature.
2.4.2 Euler Two-Phase Flow Model
The Euler two-phase flow model describes the flow of the two-phase fluid. The model assumes that the two phases are continuous and that the flow of each phase can be described by the Navier-Stokes equations.
2.4.3 Momentum Transfer Source Term between Two Phases
The momentum transfer source term between two phases describes the momentum transfer between the two phases. The term includes the drag force, the lift force, the wall lubrication force, and the virtual mass force.
2.4.4 Mass Transfer Source Term between Two Phases
The mass transfer source term between two phases describes the mass transfer between the two phases. The term includes the evaporation rate and the condensation rate.
2.4.5 Wall Boiling Heat Transfer Model
The wall boiling heat transfer model describes the heat transfer at the wall when the fluid boils. The model assumes that the heat transfer at the wall is due to the convection and the boiling and that the heat transfer coefficient can be calculated based on the boiling curve.
2.5 Numerical Simulation Method of Quenching Process Based on Thermo-Fluid-Solid Coupling Model
The numerical simulation method of the quenching process based on the thermo-fluid-solid coupling model couples the fluid domain of the quenching medium and the solid domain of the quenched workpiece. The method uses the wall function and Gaussian integral interpolation method to replace the role of the heat transfer coefficient in the simulation. The method then solves the coupled equations to obtain the temperature field, the stress field, and the organization field in the solid during the quenching process.
3. Numerical Simulation and Experimental Study of Thermo-Fluid-Solid Coupling during the Quenching Process
3.1 Introduction
This section conducts numerical simulation and experimental studies of thermo-fluid-solid coupling during the quenching process. The numerical simulation uses the finite element-finite volume coupling method to solve the coupled equations. The experimental study uses a 45 steel cylinder as the experimental object to conduct a water quenching experiment. The results of the numerical simulation and the experimental study are compared and analyzed to verify the accuracy of the simulation method.
3.2 Establishment of Numerical Simulation Platform for Quenching Process of Thermo-Fluid-Solid Coupling
3.2.1 Establishment of Solid Domain Model
The solid domain model is established using the finite element method. The model includes the temperature field, the stress field, and the organization field in the solid during the quenching process. The model also includes the phase transformation kinetics and the latent heat release.
3.2.2 Establishment of Fluid Domain Model
The fluid domain model is established using the finite volume method. The model includes the flow field and the temperature field in the fluid during the quenching process. The model also includes the boiling curve and the heat transfer coefficient.
3.2.3 Coupling Model of Solid Domain and Fluid Domain
The coupling model of the solid domain and the fluid domain couples the two domains using the interpolation method. The model also includes the heat transfer coefficient and the boiling curve.
3.3 Results and Analysis of Numerical Simulation of Quenching Process of Thermo-Fluid-Solid Coupling
3.3.1 Water Quenching Experiment and Verification Method
The water quenching experiment uses a 45 steel cylinder as the experimental object. The experiment measures the temperature field, the stress field, and the organization field in the solid during the quenching process. The experiment also measures the hardness and the residual stress of the quenched workpiece. The results of the experiment are compared with the results of the numerical simulation to verify the accuracy of the simulation method.
3.3.2 Verification of Quenching Organization and Comparison of Hardness
The verification of the quenching organization compares the microstructure of the quenched workpiece with the predicted microstructure of the numerical simulation. The comparison of the hardness compares the hardness of the quenched workpiece with the predicted hardness of the numerical simulation. The results show that the microstructure and the hardness of the quenched workpiece are consistent with the predicted results of the numerical simulation.
3.3.3 Comparison of Temperature and Stress
The comparison of the temperature compares the temperature field in the solid during the quenching process with the predicted temperature field of the numerical simulation. The comparison of the stress compares the stress field in the solid during the quenching process with the predicted stress field of the numerical simulation. The results show that the temperature field and the stress field in the solid during the quenching process are consistent with the predicted results of the numerical simulation.
4. Study on the Effect of Quenching Medium Flow Parameters on the Quenching Process
4.1 Introduction
This section studies the effect of quenching medium flow parameters on the quenching process. The study uses a quenching tank structure to change the flow state of the quenching medium. The study then uses the numerical simulation method of thermo-fluid-solid coupling to analyze the effect of the change in the quenching medium flow parameters on the quenching process.
4.2 Design of Quenching Tank Structure and Its Impact on Quenching Cooling
4.2.1 Adding Stirring Device to Promote Water Flow
The adding of a stirring device to promote water flow can improve the heat transfer efficiency between the quenching medium and the workpiece. The study uses a spiral propeller as the stirring device and analyzes the effect of the stirring device on the flow field and the heat transfer coefficient of the quenching medium.
4.2.2 Adding Guide Device to Improve Quenching Medium Flow
The adding of a guide device to improve quenching medium flow can improve the uniformity of the flow field of the quenching medium. The study uses a guide device to improve the flow field of the quenching medium and analyzes the effect of the guide device on the flow field and the heat transfer coefficient of the quenching medium.
4.2.3 Impact of Quenching Medium Flow on Quenching Cooling Process
The impact of quenching medium flow on the quenching cooling process can affect the temperature distribution and the stress distribution in the workpiece. The study uses the numerical simulation method of thermo-fluid-solid coupling to analyze the effect of the quenching medium flow on the quenching cooling process.
4.3 Impact of Quenching Medium Temperature on Quenching Cooling Characteristics of 45 Steel
4.3.1 Impact of Quenching Medium Temperature on Evolution of Workpiece Temperature Field
The impact of quenching medium temperature on the evolution of the workpiece temperature field can affect the phase transformation and the stress distribution in the workpiece. The study uses the numerical simulation method of thermo-fluid-solid coupling to analyze the effect of the quenching medium temperature on the evolution of the workpiece temperature field.
4.3.2 Impact of Quenching Medium Temperature on Distribution and Evolution of Stress Field
The impact of quenching medium temperature on the distribution and evolution of the stress field can affect the residual stress and the hardness of the workpiece. The study uses the numerical simulation method of thermo-fluid-solid coupling to analyze the effect of the quenching medium temperature on the distribution and evolution of the stress field.
5. Numerical Simulation Study of Thermo-Fluid-Solid Coupling during the Quenching of Spiral Bevel Gears
5.1 Introduction
This section conducts a numerical simulation study of thermo-fluid-solid coupling during the quenching of spiral bevel gears. The study uses the numerical simulation method of thermo-fluid-solid coupling to analyze the quenching process of spiral bevel gears. The study also compares the results of the numerical simulation with the results of the experimental study to verify the accuracy of the simulation method.
5.2 Simulation and Analysis of Quenching Temperature Field of Spiral Bevel Gears
5.2.1 Establishment of Three-Dimensional Finite Element Model of Spiral Bevel Gears
The establishment of a three-dimensional finite element model of spiral bevel gears uses the finite element method. The model includes the geometry, the temperature field, the stress field, and the organization field of the spiral bevel gears. The model also includes the phase transformation kinetics and the latent heat release.
5.2.2 Evolution Law of Temperature during the Quenching of Spiral Bevel Gears
The evolution law of temperature during the quenching of spiral bevel gears describes the change in the temperature field of the spiral bevel gears during the quenching process. The law shows that the temperature field of the spiral bevel gears changes significantly during the quenching process and that the temperature distribution is uneven.
5.2.3 Measurement of Cooling Curves at Different Positions
The measurement of cooling curves at different positions measures the temperature field of the spiral bevel gears at different positions during the quenching process. The measurement shows that the temperature field of the spiral bevel gears at different positions changes differently during the quenching process and that the temperature distribution is uneven.
5.2.4 Analysis and Comparison of Cooling Conditions at Characteristic Positions
The analysis and comparison of cooling conditions at characteristic positions compares the temperature field of the spiral bevel gears at characteristic positions during the quenching process. The comparison shows that the temperature field of the spiral bevel gears at characteristic positions changes differently during the quenching process and that the temperature distribution is uneven.
5.3 Comparison of Differences in Different Numerical Simulation Methods under Quenching Medium Flow
5.3.1 Differences in Speeds at Different Positions of Spiral Bevel Gears
The differences in speeds at different positions of spiral bevel gears show that the flow field of the quenching medium is uneven and that the speed of the quenching medium at different positions of the spiral bevel gears is different. The study uses the numerical simulation method of thermo-fluid-solid coupling to analyze the differences in speeds at different positions of the spiral bevel gears.
5.3.2 Differences in Heat Transfer Coefficient Curves under Different Flow Rates of Quenching Oil
The differences in heat transfer coefficient curves under different flow rates of quenching oil show that the heat transfer coefficient of the quenching oil changes with the flow rate. The study uses the numerical simulation method of thermo-fluid-solid coupling to analyze the differences in heat transfer coefficient curves under different flow rates of quenching oil.
5.3.3 Differences in Simulation Results of Different Numerical Simulation Methods under Quenching Medium Flow
The differences in simulation results of different numerical simulation methods under quenching medium flow show that the simulation results of different numerical simulation methods are different. The study uses the numerical simulation method of thermo-fluid-solid coupling to analyze the differences in simulation results of different numerical simulation methods under quenching medium flow.
5.3.4 Analysis and Comparison of Quenching Hardness and Stress under Different Flow Rates of Quenching Oil
The analysis and comparison of quenching hardness and stress under different flow rates of quenching oil show that the quenching hardness and the stress of the spiral bevel gears change with the flow rate. The study uses the numerical simulation method of thermo-fluid-solid coupling to analyze the analysis and comparison of quenching hardness and stress under different flow rates of quenching oil.
6. Conclusions
This article proposes a thermo-fluid-solid coupling numerical simulation method for the quenching process. The method couples the fluid domain of the quenching medium and the solid domain of the quenched workpiece and replaces the role of the heat transfer coefficient in the simulation. The article also conducts experimental studies to verify the accuracy of the simulation method. The main research results include: (1) The numerical simulation method of thermo-fluid-solid coupling during the quenching process can accurately predict the temperature field, the stress field, and the organization field in the solid during the quenching process; (2) The numerical simulation and experimental study of thermo-fluid-solid coupling during the quenching process show that the microstructure and the hardness of the quenched workpiece are consistent with the predicted results of the numerical simulation; (3) The study on the effect of quenching medium flow parameters on the quenching process shows that the quenching medium flow parameters can affect the temperature distribution and the stress distribution in the workpiece; (4) The numerical simulation study of thermo-fluid-solid coupling during the quenching of spiral bevel gears shows that the numerical simulation method can accurately predict the temperature field, the stress revealing the quenching process of spiral bevel gears, which is of great significance for optimizing the quenching process parameters and improving the quality of spiral bevel gears.