Spiral bevel gear play a pivotal role in the automotive industry, particularly in power transmission systems such as differentials, where they facilitate the smooth and efficient transfer of power from the engine to the wheels. Their unique characteristics not only contribute to the performance, efficiency, and durability of automotive drivetrains but also significantly enhance the driving experience. This performance analysis of spiral bevel gear within the automotive context will cover aspects such as noise and vibration reduction, efficiency and power loss, durability and maintenance needs, and their impact on vehicle performance.
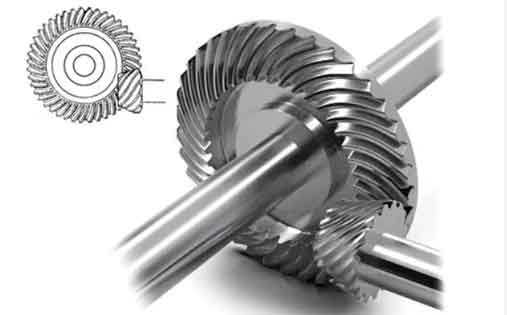
Noise and Vibration Reduction
One of the primary advantages of spiral bevel gear in automotive applications is their contribution to noise reduction. The spiral teeth design allows for a more gradual engagement between gears compared to straight-cut gears, significantly reducing noise and vibration. This smoother engagement is crucial for passenger comfort and vehicle refinement, particularly at high speeds or under heavy loads. Automotive engineers favor spiral bevel gear in the drivetrain to enhance the quality and comfort of the ride.
Efficiency and Power Loss
Efficiency is a critical factor in automotive applications, where maximizing the power output from the engine to the wheels is essential. Spiral bevel gear are known for their high efficiency, typically ranging between 95% to 99%. The efficiency of spiral bevel gear ensures minimal power loss during transmission, contributing to better fuel economy and higher performance. Their design ensures that a larger contact area is available, distributing the load more evenly and reducing peak stresses on spiral bevel gear teeth. This efficient power transmission is particularly beneficial in high-performance and racing applications where every bit of power counts.
Durability and Maintenance Needs
The durability of spiral bevel gear is another factor contributing to their widespread use in the automotive industry. The materials used, such as hardened steel alloys, combined with precision manufacturing techniques, result in spiral bevel gear that can withstand high stress and torque applications over extended periods. Additionally, the spiral bevel gear design inherently offers better load distribution, which reduces wear and extends spiral bevel gear life. However, proper maintenance, including regular inspection and lubrication, is essential to ensure their longevity and performance. The automotive industry benefits from the reduced need for frequent replacements or repairs, contributing to lower maintenance costs and improved vehicle reliability.
Impact on Vehicle Performance
The integration of spiral bevel gear in automotive drivetrains directly impacts vehicle performance. Their ability to transmit power efficiently and smoothly enhances acceleration and handling characteristics, providing a more responsive driving experience. Furthermore, their reduced noise and vibration levels contribute to a quieter cabin, improving the overall comfort for passengers. In high-performance vehicles, such as sports cars and racing applications, the advantages of spiral bevel gear—such as their high load capacity and efficient power transmission—are crucial for achieving superior performance and speed.
Conclusion
Spiral bevel gear offer significant advantages in automotive applications, contributing to enhanced vehicle performance, efficiency, and comfort. Their design and material properties allow for smooth, quiet operation, high durability, and minimal power loss, making them an ideal choice for automotive power transmission systems. As the automotive industry continues to evolve, with increasing demands for efficiency and performance, the role of spiral bevel gear is likely to remain critical. Future advancements in materials science and manufacturing technologies promise even greater improvements in spiral bevel gear performance, further solidifying the position of spiral bevel gear in the automotive sector.