1. Introduction

Spiral bevel gears are crucial transmission elements widely used in various equipment such as vehicles, aircraft, and ships. During power transmission, the deformation of the transmission system under load can cause a shift in the meshing state of spiral bevel gear pair, affecting the transmission performance of the gear pair. Accurate analysis of the meshing misalignment of the spiral bevel gear transmission system under load is essential for optimizing the gear tooth profile.
1.1 Research Background
Many scholars have studied the analysis methods of the meshing misalignment amount of gear transmission systems. However, when analyzing the deformation of the transmission shaft, most of them simplify the transmission shaft into a beam element model. When the transmission shaft structure is complex, this simplification may lead to large errors in the deformation analysis results, resulting in inaccurate calculation of the meshing misalignment amount of spiral bevel gear transmission system and affecting the optimization design effect of the tooth surface.
1.2 Research Purpose
This paper aims to propose a meshing misalignment analysis method for the step-by-step spiral bevel gear transmission system based on the solid finite element method to improve the accuracy of meshing misalignment analysis and calculation efficiency.
2. Gear Pair Meshing Misalignment Amount Calculation
2.1 Definition of Meshing Misalignment Amount
The gear transmission system includes components such as shafts, bearings, and gears, and has a complex structure. When the system works, the meshing force of spiral bevel gear pair is transmitted to the shafts and bearings, causing the system to deform and the relative installation positions of spiral bevel gears to shift. The offset amount of the gear pair’s installation position under load is the meshing misalignment amount of the gear pair.
The meshing misalignment amount can be calculated in the initial gear coordinate system. For example, if the offset vector of the shaft intersection point is R’=ROA-ROB, then the meshing misalignment amount can be calculated as follows:
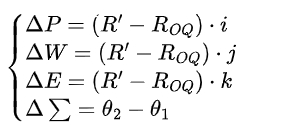
where ΔP and ΔW are the relative displacement amounts of spiral bevel gear pair along the small wheel axial direction; ΔE is the relative displacement amount along the large wheel axial direction; Δ∑ is the relative change amount along the shaft angle direction; i,j,k are the unit vectors of the coordinate axes in the initial coordinate system; θ1 and θ2 are the shaft angles before and after deformation.
2.2 Calculation Method of Meshing Misalignment Amount
The calculation principle of the meshing misalignment amount of spiral bevel gear pair is as follows. First, establish the initial coordinate system ∑q=O;x,y,z and the moment coordinate system ∑q=O;x’,y’,z’. Then, consider the projection points P and G of the midpoints of the small and large gear widths on the gear axis before and after deformation. Calculate the distances δp and δw between the points before and after deformation, and the direction vectors s1 and s2 of the tangents at the points P* and G. Calculate the normal vector n=s1 X s2.
Next, calculate the distance IE and angle θs between the vectors s1 and s2, and establish equations related to the distances IP2 and IW2 on the equivalent axes of the small and large wheels. Finally, superimpose the parameters before and after system deformation to obtain the meshing misalignment amount of spiral bevel gear pair:
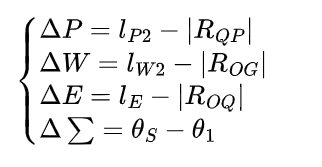
3. Comparison of Transmission Shaft Deformation Analysis of Different Calculation Models
3.1 Beam Element Model
The transmission shaft is mostly simplified into a beam element model. The deformation analysis principle is to divide the transmission shaft according to its cross-section, represent each shaft section with two nodes and one beam unit, and then calculate the total stiffness matrix of the entire transmission shaft by superimposing the stiffness matrices of each beam unit. According to the relationship between force and deformation, the force balance equation of the beam is constructed to calculate the deformation amount of the beam unit at each node.
3.2 Comparison Example
Taking a complex transmission shaft as an example, a beam unit model and a solid finite element model are established with the same material, force, and boundary conditions. The deformation results of the two models are compared. The results show that the deformation amount of the transmission shaft calculated by the beam unit model has certain errors in each direction compared with the solid finite element model. The error in the radial direction (Xb,Yb) is about 13%-16%, and the error in the axial direction (Zb) is even larger, about 30%. Therefore, when the transmission shaft structure is complex, the beam unit model cannot be used to replace the solid finite element model to analyze its loaded deformation situation.
4. Calculation Example
4.1 Meshing Misalignment Amount Calculation Comparison
Taking a certain bus drive axle as an example for gear pair meshing misalignment analysis. The basic parameters of the spiral bevel gear are shown in Table 1.
Basic Parameters | Pinion | Gear |
---|---|---|
Number of Teeth | 7 | 43 |
Module (mm) | 10.512 | |
Shaft Angle (°) | 90 | |
Offset Distance (mm) | 46 | |
Pressure Angle (°) | 22.5 | |
Tooth Face Width (mm) | 81.61 | 74.00 |
Outer Cone Distance (mm) | 238.77 | 230.58 |
Helix Angle (°) | 48.083 | 34.345 |
Pitch Cone Angle (°) | 11.100 | 78.583 |
The rated working torque of spiral bevel gear pair is . The calculated results of the meshing force and moment are shown in Table 2.
Shaft System | Tangential Force (N) | Axial Force (N) | Radial Force (N) | Moment (N – m) |
---|---|---|---|---|
Input Shaft | 81310 | 28990 | 530 | 2383 |
Output Shaft | 91750 | 28990 | 45870 | 5460 |
The stiffness matrix of the bearings in the transmission system is calculated, and the values on the main diagonal elements of each bearing stiffness matrix are shown in Table 3.
Stiffness | Bearing 1 | Bearing 2 | Bearing 3 | Bearing 4 | Bearing 5 |
---|---|---|---|---|---|
(F/D)/(N/mm) | 14.715 | 13.95 | 53.42 | 17.60 | |
(F/D)/(N/mm) | 69.15 | 53.03 | 16.84 | 10.16 | 38.48 |
(F/D)/(N/mm) | 11.33 | 52.24 | 71.99 | 55.32 | 26.22 |
(M/A)/(N – mm/rad) | 34.91 | 18.39 | 17.51 | 24.83 | 84.81 |
(M/A)/(N – mm/rad) | 22.09 | 19.18 | 40.18 | 24.02 | 57.80 |
The transmission shaft coupling analysis finite element model is established, and the deformation amount of the transmission shaft and the meshing misalignment amount of spiral bevel gear pair are calculated. At the same time, a full finite element model of the transmission system is established for comparison. The deformation amounts of the transmission shaft nodes of the three models are extracted. The average error of the beam unit model compared with the full finite element model is about 12.4% for the input shaft and about 10.2% for the output shaft. The average error of the solid finite element transmission shaft coupling analysis model compared with the full finite element model is about 1.9% for the input shaft and about 1.2% for the output shaft. The meshing misalignment amounts of the two models are shown in Table 4.
Meshing Misalignment | Transmission Shaft Coupling Analysis Model | Full Finite Element Model |
---|---|---|
ΔP(mm) | 0.0938 | 0.0952 |
ΔW(mm) | -0.0354 | -0.0362 |
ΔY(°) | 0.0331 | 0.0337 |
ΔE(mm) | -0.152 | -0.156 |
It can be seen that the error of the meshing misalignment amount between the transmission shaft coupling analysis model and the full finite element model is within 2.5%.
4.2 Loading Mark and Transmission Error Comparison
The stress at the contact position of the tooth surface at each meshing instant is superimposed on the tooth surface to obtain the loading contact mark of the tooth surface. The loading mark calculated by the method described in this paper, and the loading mark calculated by the full finite element model.
The loading mark obtained by the step-by-step spiral bevel gear transmission system meshing misalignment analysis method is consistent with the position and shape of the loading mark calculated by the full finite element model, with only slight differences in the tooth width direction. The curve shapes of their loading transmission errors match, and the amplitude deviation is about 1.3%.
The grid numbers of the step-by-step spiral bevel gear transmission system meshing misalignment analysis method are about 185,000 for the transmission shaft coupling deformation analysis model part and about 804,000 for spiral bevel gear tooth loading contact analysis model considering meshing misalignment (the grid size of the tooth surface contact part is ). The grid number of the full finite element model is about 3080,000 (the grid size of the tooth surface contact part is ). The analysis times of the two analysis models are shown in Table 5.
Two Models | Transmission Shaft Coupling Analysis Model and Gear Tooth Contact Analysis Model | Full Finite Element Model |
---|---|---|
Analysis Time (h) | 6.1 | 26.2 |
It can be seen that the analysis time of the step-by-step spiral bevel gear transmission system meshing misalignment analysis method is significantly reduced compared with the full finite element model. If the tooth surface grid of the full finite element model is divided into , the analysis time will be further increased.
5. Conclusion
5.1 Main Findings
(1) When the transmission shaft model structure is complex, there is a large error between the loaded deformation of the shaft calculated by the beam unit model and the calculation result of the solid finite element model. This is because the beam unit model simplifies the shaft’s structure and ignores some factors that affect deformation, such as the complex geometry and material properties of the actual shaft. As a result, the calculated deformation may not accurately represent the real situation, leading to errors in subsequent analyses related to gear meshing misalignment.
(2) The proposed transmission shaft deformation coupling analysis model based on the solid finite element model comprehensively considers spiral bevel gear meshing force action and the coupling situation of the transmission shaft structure flexibility and the bearing support flexibility. It takes into account the actual physical properties and interactions of these components. For example, the model accurately represents the bearing stiffness and its effect on the shaft’s deformation. This allows for a more accurate analysis of the loaded deformation situation of the transmission shaft of the spiral bevel gear transmission system, providing a more reliable basis for calculating gear meshing misalignment.
(3) The proposed step-by-step spiral bevel gear transmission system meshing misalignment analysis method based on the solid finite element method can accurately analyze the loading mark and transmission error of spiral bevel gear pair. It first calculates the meshing misalignment amount accurately through the transmission shaft coupling analysis model and then uses this information to construct a loading contact analysis model of spiral bevel gear teeth. This enables a detailed study of the gear pair’s behavior during meshing. The method also significantly improves the calculation efficiency. Compared to the full finite element model, it requires less computational resources and time, making it more practical for engineering applications.
5.2 Future Research Directions
In the future, research could focus on several aspects to further improve and expand the application of this method.
Improving the Accuracy of Equivalent Meshing Force Calculation
- Currently, the equivalent meshing force calculation is based on certain assumptions and formulas. Future research could explore more accurate ways to calculate this force. This might involve considering more detailed gear geometry and material properties, as well as the actual contact conditions during meshing. For example, more precise models could be developed to account for the effects of tooth surface roughness and lubrication on the meshing force.
- Another area of improvement could be in the treatment of axial and radial forces. The current method may have some limitations in accurately representing these forces, especially when dealing with complex gear geometries and loading conditions. Research could aim to develop more sophisticated algorithms to handle these forces more accurately.
Reducing the Grid Number of the Finite Element Model without Sacrificing Accuracy
- The finite element model used in the current method requires a certain number of grids to achieve accurate results. However, a large number of grids can lead to increased computational costs and longer analysis times. Future research could focus on developing techniques to reduce the grid number while maintaining accuracy. This might involve advanced mesh generation algorithms that can adaptively adjust the grid density based on the stress and deformation gradients in the model.
- Another approach could be to use alternative numerical methods or approximations that can provide accurate results with fewer grids. For example, model reduction techniques could be explored to simplify the complex finite element model without losing essential information about spiral bevel gear system’s behavior.
Extending the Method to Other Types of Gear Transmission Systems
In addition to adapting the method to different gear types, research could also focus on validating the extended method through experimental studies. This would involve conducting tests on actual gear transmission systems of different types and comparing the results obtained from the extended method with experimental data. This would help to ensure the reliability and accuracy of the extended method for a wider range of applications.
The current method is specifically designed for spiral bevel gear transmission systems. Future research could aim to extend this method to other types of gear transmission systems, such as worm gears, helical gears, and planetary gears. This would require adapting the model and analysis procedures to the unique characteristics of each gear type. For example, the meshing principles and force distributions are different for different gear types, and these need to be accurately represented in the extended method.