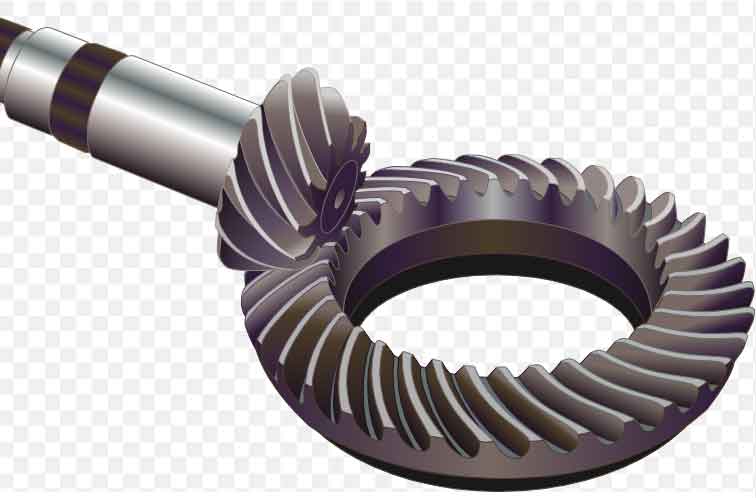
Spiral bevel gears play a crucial role in robotics, enabling precision motion control and efficient power transmission in various robotic systems. Advancements in automation technology have led to significant improvements in the design and application of spiral bevel gears in robotics. Let’s explore some of the key advancements:
1. Miniaturization:
With the trend toward smaller and more compact robots, there has been a need for miniaturized spiral bevel gears. Advancements in manufacturing techniques and materials have allowed for the production of smaller, yet still robust and efficient, spiral bevel gears suitable for micro and nano-robotics applications.
2. High-Precision Manufacturing:
Advances in manufacturing processes, such as CNC machining, gear hobbing, and gear grinding, have enabled the production of spiral bevel gears with exceptional precision. This precision ensures smooth and accurate gear meshing, reducing noise and vibration in robotic systems.
3. Customization and Integration:
Robotics applications often require gear designs tailored to specific requirements. Advancements in computer-aided design (CAD) and simulation software have made it easier to customize spiral bevel gears for specific robotic tasks and integrate them seamlessly into complex robotic systems.
4. Multi-Axis Robots:
Many modern robots operate in multiple axes, requiring specialized gear designs to transmit motion across different planes. Spiral bevel gears with the capability to handle non-parallel shafts and transmit motion at various angles are essential for such multi-axis robots.
5. High Torque Applications:
Some robotic tasks involve handling heavy loads or performing tasks requiring high torque. Advancements in gear materials and heat treatment processes have led to the development of spiral bevel gears with enhanced torque capacity, enabling robots to handle more substantial payloads efficiently.
6. Gearbox Efficiency:
In robotics, compact and efficient gearboxes are vital for reducing weight and maximizing power transfer. Improved design and material selection for spiral bevel gears have contributed to more efficient gearboxes that minimize power loss and improve overall robot performance.
7. Collaborative Robots (Cobots):
Collaborative robots, or cobots, are designed to work safely alongside humans in industrial environments. The use of spiral bevel gears in cobots allows for smoother and quieter operation, contributing to a safer and more user-friendly robotic experience.
8. Maintenance and Lubrication:
Advances in lubrication technologies and maintenance practices have led to improved gear lifespan and reduced downtime for robotic systems.
Overall, the advancements in automation technology have driven the development of more sophisticated and efficient robotic systems, with spiral bevel gears playing a critical role in achieving precise motion control and reliable power transmission. As robotics continue to evolve, further innovations in gear design, materials, and manufacturing are expected, leading to even more capable and versatile robotic systems in various industries.