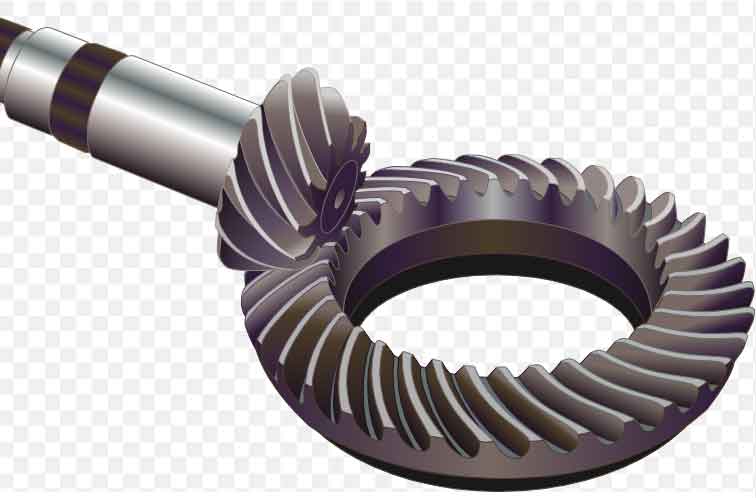
Spiral bevel gears play a crucial role in robotics, where precision motion control is essential for accurate and reliable robotic movements. Their unique design characteristics make them well-suited for robotic applications that require smooth and precise motion. Here’s how spiral bevel gears enable precision motion control in robotics:
1. Smooth and Precise Tooth Engagement:
- Spiral bevel gears have helical teeth that engage gradually and smoothly, resulting in a continuous meshing action. This smooth tooth engagement reduces gear vibration and noise, providing precise and predictable motion control for the robotic system.
2. Improved Load Distribution:
- The helical tooth design allows for multiple teeth to be in contact at any given time. This distributes the load over a larger contact area, reducing localized stresses and ensuring uniform power transmission throughout the gear meshing.
3. High Efficiency:
- Spiral bevel gears have high gear efficiency due to their smooth tooth engagement and optimized tooth contact pattern. This efficiency is crucial in robotic applications where energy conservation is essential, allowing the robot to perform more tasks on a single charge.
4. Reduced Backlash:
- Backlash, which refers to the clearance between gear teeth, can introduce inaccuracies in motion control. Spiral bevel gears typically have lower backlash compared to other gear types, ensuring more precise positioning and repeatability in robotic movements.
5. Compact and Lightweight Design:
- Spiral bevel gears are known for their compact and lightweight design, making them suitable for integration into small and lightweight robotic systems. Their compactness allows for efficient space utilization within the robot’s structure.
6. Robustness and Durability:
- Spiral bevel gears are engineered to handle high loads and transmit torque efficiently. This robustness and durability ensure reliable performance in demanding robotic applications, even under continuous operation.
7. Multi-Axis Motion Control:
- Spiral bevel gears are well-suited for multi-axis motion control in robotics. They can transmit power between intersecting shafts at different angles, enabling complex and precise movements in robotic arms and manipulators.
8. Low Noise and Vibration:
- The helical tooth engagement in spiral bevel gears results in reduced noise and vibration compared to other gear types. This is crucial in robotic applications where noise reduction is necessary for a quieter and more comfortable operation.
9. Back-Drivability:
- In some robotic systems, back-drivability is essential to allow for manual manipulation or collision avoidance. Spiral bevel gears can be designed with appropriate characteristics to facilitate back-drivability when required.
10. Application Diversity:
- Spiral bevel gears find application in various robotic systems, including industrial robots, collaborative robots (cobots), medical robots, and space exploration robots. Their versatility and precision make them suitable for a wide range of robotic tasks.
Spiral bevel gears are a key enabler of precision motion control in robotics. Their smooth tooth engagement, improved load distribution, high efficiency, and low noise make them ideal for precise robotic movements. Whether in industrial settings, medical applications, or space exploration, spiral bevel gears contribute to the accuracy and reliability of robotic systems, making them essential components in the advancement of robotics technology.