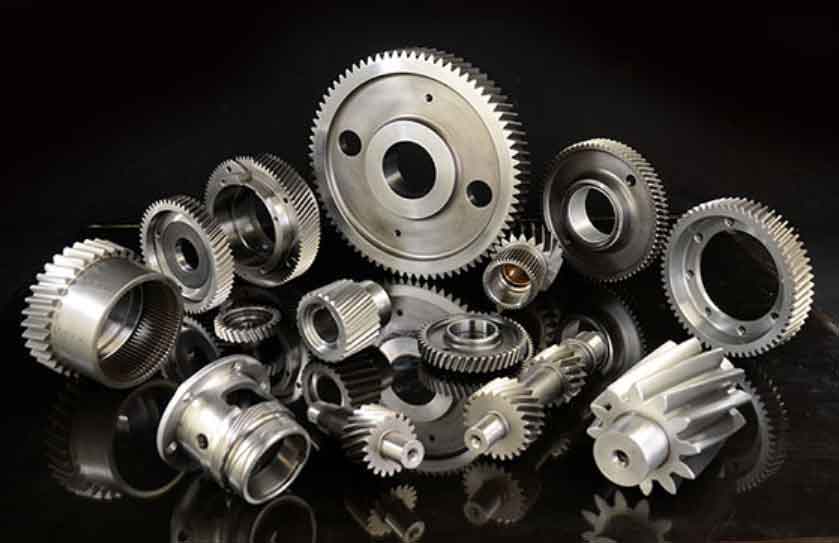
Spiral bevel gears and straight bevel gears are both types of bevel gears used to transmit power between intersecting shafts. While they share some similarities, they have distinct design characteristics and performance attributes that make them suitable for different applications. Here’s a comparative analysis of spiral bevel gears vs. straight bevel gears:
1. Tooth Profile:
- Spiral Bevel Gears: Spiral bevel gears have a curved tooth profile that gradually engages and disengages as the gears rotate. This continuous engagement results in smoother meshing, reducing noise and vibration during operation.
- Straight Bevel Gears: Straight bevel gears have a straight-line tooth profile with no helix angle. Their engagement is instantaneous, leading to more impact and noise during gear meshing.
2. Efficiency:
- Spiral Bevel Gears: Due to their curved tooth profile and gradual engagement, spiral bevel gears offer higher efficiency compared to straight bevel gears. This leads to reduced friction and power losses during gear operation.
- Straight Bevel Gears: Straight bevel gears are generally less efficient than spiral bevel gears due to their instantaneous engagement, which can result in higher sliding friction.
3. Noise and Vibration:
- Spiral Bevel Gears: The gradual tooth engagement and curved tooth profile of spiral bevel gears contribute to smoother operation, reducing noise and vibration levels. They are commonly used in applications where noise reduction is important.
- Straight Bevel Gears: Straight bevel gears produce more noise and vibration during gear meshing compared to spiral bevel gears. Their design is better suited for applications where noise considerations are not critical.
4. Load Capacity:
- Spiral Bevel Gears: Spiral bevel gears have larger contact areas and can handle higher loads and torque compared to straight bevel gears. They are suitable for heavy-duty applications where high load-carrying capacity is essential.
- Straight Bevel Gears: While capable of handling moderate loads, straight bevel gears may not be as robust as spiral bevel gears when it comes to heavy-duty applications.
5. Applications:
- Spiral Bevel Gears: Due to their efficiency, smooth operation, and high load capacity, spiral bevel gears are commonly used in applications that require precision motion control, such as automotive transmissions, aerospace systems, and robotics.
- Straight Bevel Gears: Straight bevel gears are often found in applications where precision motion control is not a primary concern, such as power tools, hand drills, and some low-speed gearboxes.
6. Manufacturing Complexity:
- Spiral Bevel Gears: The manufacturing process of spiral bevel gears is more complex and requires specialized gear cutting techniques to achieve the curved tooth profile.
- Straight Bevel Gears: Straight bevel gears are relatively simpler to manufacture compared to spiral bevel gears.
In summary, both spiral bevel gears and straight bevel gears have their unique advantages and are suitable for different engineering applications. Spiral bevel gears offer smoother operation, higher efficiency, and greater load capacity, making them ideal for precision applications. On the other hand, straight bevel gears are simpler to manufacture and find use in less demanding applications where noise considerations may not be critical. The choice between the two types of gears depends on the specific requirements and performance characteristics needed for the application at hand.