Spiral bevel gears and straight bevel gears are both types of bevel gears used in various industrial applications. While they have similarities in their basic functions, they have distinct design features and performance characteristics. Let’s conduct a comparative analysis of spiral bevel gears and straight bevel gears:
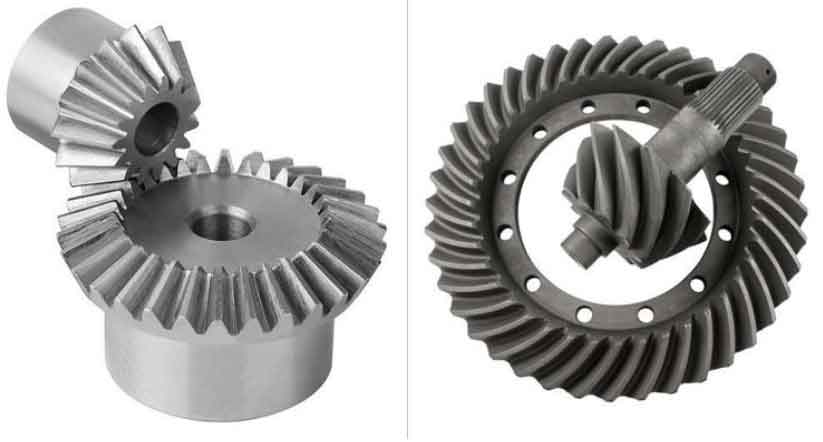
1. Tooth Profile:
- Spiral Bevel Gears: The teeth of spiral bevel gears have a curved shape, resulting in a helical angle. This helix angle allows for gradual tooth engagement, which results in smoother and quieter operation. The helix angle also helps in reducing axial thrust loads.
- Straight Bevel Gears: The teeth of straight bevel gears have a straight-line profile and do not feature a helical angle. As a result, the tooth engagement is sudden and causes more impact and noise during operation.
2. Efficiency:
- Spiral Bevel Gears: Due to their helical tooth profile, spiral bevel gears provide higher efficiency compared to straight bevel gears. The gradual tooth engagement reduces friction and noise, resulting in more efficient power transmission.
- Straight Bevel Gears: Straight bevel gears have slightly lower efficiency due to the abrupt tooth engagement and increased friction during operation.
3. Load Capacity:
- Spiral Bevel Gears: The helical tooth profile of spiral bevel gears distributes the load over multiple teeth, enhancing their load-carrying capacity. They can handle higher torque and axial loads.
- Straight Bevel Gears: Straight bevel gears have a lower load-carrying capacity compared to spiral bevel gears due to the concentrated load on fewer teeth.
4. Noise and Vibration:
- Spiral Bevel Gears: The helical tooth profile and gradual tooth engagement of spiral bevel gears result in significantly reduced noise and vibration levels during operation.
- Straight Bevel Gears: Straight bevel gears generate more noise and vibration due to the sudden tooth engagement.
5. Axial Thrust:
- Spiral Bevel Gears: Spiral bevel gears are designed to minimize axial thrust, making them suitable for applications where axial loads need to be controlled or minimized.
- Straight Bevel Gears: Straight bevel gears can generate higher axial thrust, which may require additional thrust bearings or other mechanisms to handle the axial loads.
6. Manufacturing Complexity:
- Spiral Bevel Gears: Manufacturing spiral bevel gears is more complex and requires specialized equipment, resulting in higher production costs.
- Straight Bevel Gears: Straight bevel gears are relatively simpler to manufacture, making them more cost-effective.
7. Applications:
- Spiral Bevel Gears: Spiral bevel gears are commonly used in applications where smooth operation, high efficiency, and low noise levels are essential, such as automotive differentials, aircraft transmissions, and industrial gearboxes.
- Straight Bevel Gears: Straight bevel gears are suitable for applications where noise levels and manufacturing costs are not primary concerns, such as in some automotive transmissions and agricultural equipment.
In summary, spiral bevel gears offer superior performance in terms of efficiency, load capacity, and noise reduction, making them preferable for many applications that demand smooth operation and high torque handling. However, straight bevel gears still find use in specific applications where cost and simplicity are the primary considerations. The choice between the two types depends on the specific requirements of the application and the trade-offs between efficiency, load capacity, manufacturing complexity, and cost.