Spiral bevel gears and straight bevel gears are two types of bevel gears used in various applications. While both are designed to transmit power and motion between intersecting shafts, they have distinct characteristics that make them suitable for different scenarios. Here’s a comparative analysis of spiral bevel gears vs. straight bevel gears:
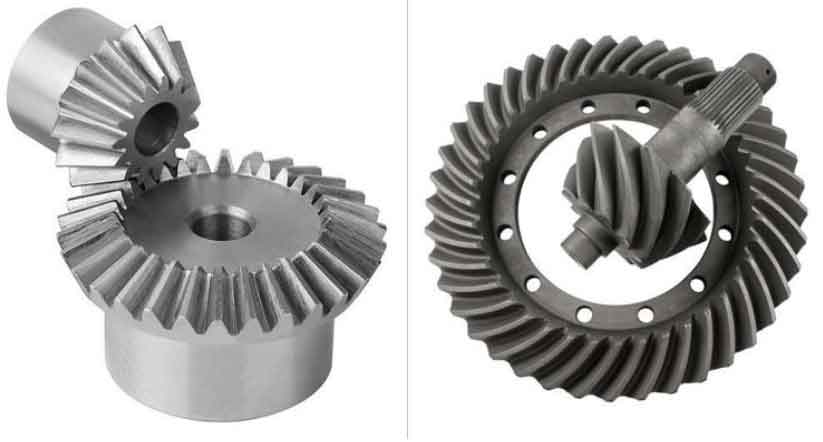
1. Tooth Design:
- Spiral Bevel Gears: Spiral bevel gears have helical teeth that are cut at an angle to the gear axis, forming a spiral pattern around the gear. This helical tooth form provides smooth and gradual tooth engagement during meshing, reducing impact and noise.
- Straight Bevel Gears: Straight bevel gears have straight-cut teeth that are cut at a right angle to the gear axis. Their tooth engagement is more abrupt, resulting in more significant impact and noise during meshing compared to spiral bevel gears.
2. Noise and Vibration:
- Spiral Bevel Gears: The helical tooth form of spiral bevel gears contributes to reduced noise and vibration during operation. Their smooth tooth engagement results in quieter gear meshing compared to straight bevel gears.
- Straight Bevel Gears: Straight bevel gears produce more noise and vibration during meshing due to their abrupt tooth engagement. They are generally noisier than spiral bevel gears, which can be a consideration in noise-sensitive applications.
3. Efficiency:
- Spiral Bevel Gears: The gradual tooth engagement of spiral bevel gears leads to reduced friction and better power transmission efficiency compared to straight bevel gears.
- Straight Bevel Gears: Straight bevel gears are less efficient than spiral bevel gears due to higher friction and impact losses during meshing.
4. Load Distribution:
- Spiral Bevel Gears: Spiral bevel gears distribute the transmitted load over multiple gear teeth, resulting in a more even load distribution. This enhances their load-carrying capacity and minimizes stress concentrations.
- Straight Bevel Gears: Straight bevel gears distribute the load over fewer gear teeth, potentially leading to higher stress concentrations on individual teeth.
5. Applications:
- Spiral Bevel Gears: Spiral bevel gears are commonly used in applications where smooth and quiet operation is essential, such as automotive differentials, high-speed machinery, and precision industrial equipment.
- Straight Bevel Gears: Straight bevel gears are often used in applications where noise is not a significant concern, and they are suitable for various industrial machinery, including mining equipment and construction machinery.
6. Complexity and Manufacturing:
- Spiral Bevel Gears: The manufacturing of spiral bevel gears involves specialized cutting methods, such as Gleason or Klingelnberg gear cutting machines, making them more complex to produce compared to straight bevel gears.
- Straight Bevel Gears: Straight bevel gears are relatively easier to manufacture and may require less specialized equipment.
Both types of bevel gears have their strengths and applications. The choice between spiral bevel gears and straight bevel gears depends on the specific requirements of the application, including considerations of noise, efficiency, load capacity, and manufacturing complexity.