Abstract
Spur gear, as one of the most fundamental components in mechanical transmission systems, are widely utilized in industries ranging from automotive to heavy machinery due to their simplicity, high efficiency, and absence of axial thrust. However, under high-speed or heavy-load conditions, spur gear pairs often experience significant dynamic forces, leading to accelerated wear, vibration, and noise. This study leverages ADAMS (Automatic Dynamic Analysis of Mechanical Systems) to establish a virtual prototype of a spur gear system, conducts dynamic simulations, and evaluates critical performance metrics such as transmission ratio stability, meshing force fluctuations, and dynamic responses of individual teeth. The findings provide theoretical insights for optimizing spur gear design, enhancing operational reliability, and mitigating vibration-related issues.
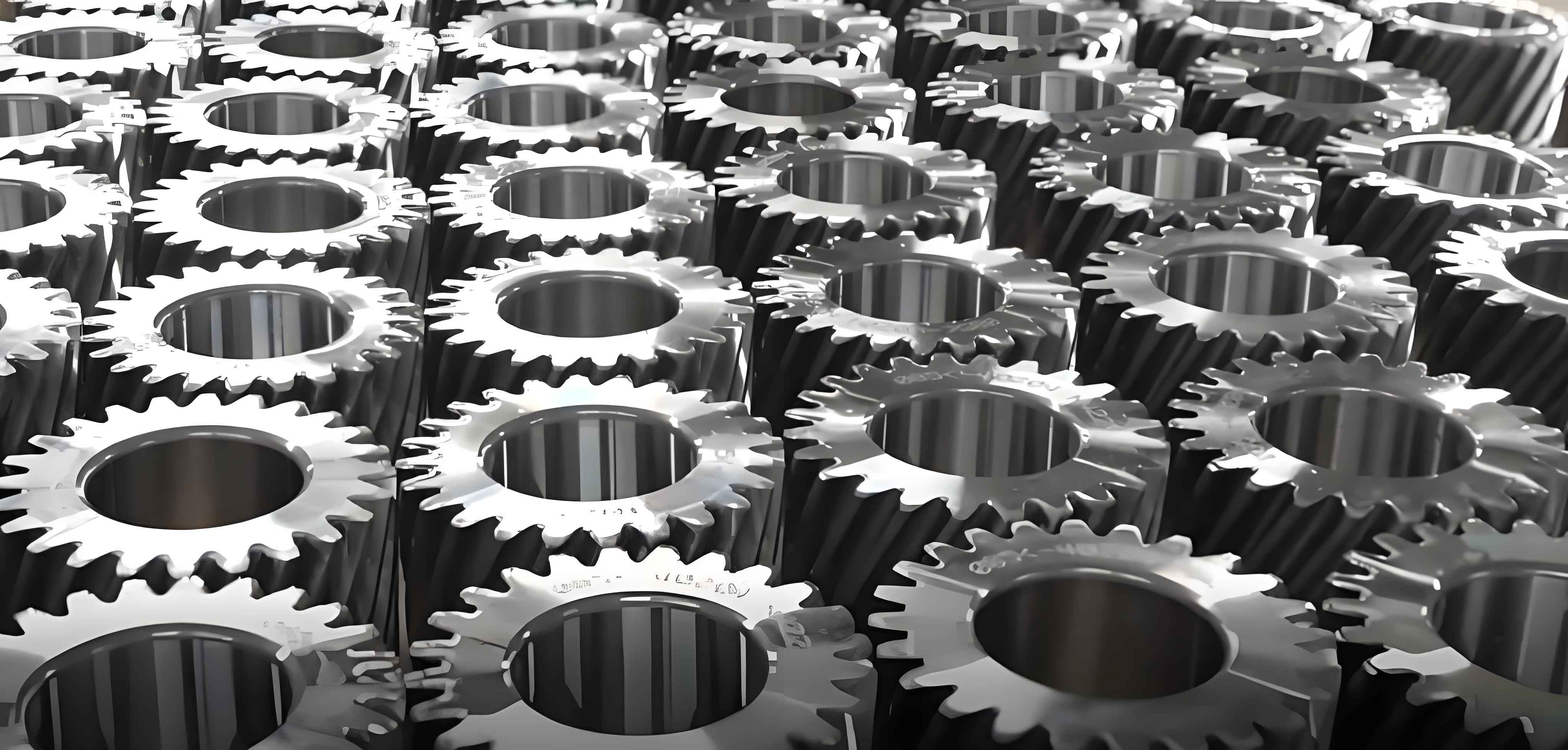
1. Introduction
Spur gear remain indispensable in power transmission systems due to their straightforward geometry, ease of manufacturing, and predictable performance. However, dynamic interactions between meshing teeth—such as fluctuating loads, misalignment, and contact stress variations—can significantly impact their longevity and efficiency. Traditional experimental approaches for analyzing spur gear dynamics are time-consuming, costly, and limited by measurement accuracy. In contrast, virtual prototyping using ADAMS offers a cost-effective, flexible, and precise alternative for simulating complex gear behaviors under diverse operating conditions.
This study focuses on a spur gear pair within a reduction gearbox, where a smaller driving gear (17 teeth) meshes with a larger driven gear (25 teeth). Key parameters, including module, pressure angle, and face width, are summarized in Table 1.
Table 1: Spur Gear Pair Design Parameters
Component | Number of Teeth | Module (mm) | Pressure Angle (°) | Face Width (mm) |
---|---|---|---|---|
Driving Gear | 17 | 10 | 20 | 100 |
Driven Gear | 25 | 10 | 20 | 100 |
2. Virtual Prototyping of Spur Gear
2.1 3D Modeling and Assembly
The spur gear pair was modeled in SolidWorks using the parameters from Table 1. The involute tooth profile was generated based on the following gear geometry equations:
- Pitch Diameter:D=m⋅ND=m⋅Nwhere mm = module, NN = number of teeth.
- Base Circle Diameter:Db=D⋅cos(α)Db=D⋅cos(α)where αα = pressure angle.
The assembled model (Figure 1) ensured proper meshing alignment and minimized initial interference.
2.2 ADAMS Virtual Prototype Setup
The SolidWorks model was exported to ADAMS in Parasolid format. Key steps included:
- Material Assignment: Steel (Density: 7,850 kg/m³, Young’s Modulus: 210 GPa).
- Constraints: Revolute joints for rotational freedom at gear centers.
- Contact Definition: A penalty-based contact algorithm modeled tooth interactions.
- Load Application: A torque of 450 kN·m was applied to the driving gear from 0–1 s, followed by a constant load from 1–5 s.
Table 2: ADAMS Simulation Parameters
Parameter | Value |
---|---|
Solver Type | GSTIFF (Stiff Solver) |
Simulation Time | 5 s |
Step Size | 0.001 s |
Contact Stiffness | 1e5 N/mm |
Damping Coefficient | 1e3 N·s/mm |
3. Dynamic Simulation Results
3.1 Transmission Ratio Stability
The theoretical transmission ratio ii is given by:i=N2N1=2517≈1.47i=N1N2=1725≈1.47
Simulation results (Figure 2) confirmed that the actual ratio fluctuated within ±0.5% of the theoretical value, demonstrating high stability under transient loads.
Table 3: Transmission Ratio Deviation Analysis
Time (s) | Theoretical Ratio | Simulated Ratio | Deviation (%) |
---|---|---|---|
1.0 | 1.47 | 1.462 | -0.54 |
3.0 | 1.47 | 1.475 | +0.34 |
5.0 | 1.47 | 1.469 | -0.07 |
3.2 Meshing Force Analysis
The meshing force FmFm between spur gear teeth was calculated using Hertzian contact theory:Fm=43⋅E⋅Re⋅δ3/2Fm=34⋅E⋅Re⋅δ3/2
where ReRe = equivalent radius of curvature, δδ = contact deformation.
Simulation data (Table 4) revealed peak forces during the initial load application (0–1 s), stabilizing thereafter.
Table 4: Meshing Force Peaks Under Load
Time Interval (s) | Average Force (kN) | Peak Force (kN) |
---|---|---|
0–1 | 320 | 450 |
1–5 | 290 | 310 |
3.3 Dynamic Response of Teeth
Stress distribution across tooth surfaces was analyzed using ADAMS/View post-processing tools. Critical stress zones were identified near the root and pitch line (Figure 3), aligning with theoretical fatigue failure points in spur gear.
Table 5: Maximum Von Mises Stress at Critical Zones
Tooth Position | Stress (MPa) |
---|---|
Root | 580 |
Pitch Line | 420 |
4. Discussion
The ADAMS-based simulation successfully captured dynamic behaviors of the spur gear pair, including transient vibrations, load-sharing variations, and stress concentrations. Key findings include:
- Transmission Ratio Stability: Minimal deviation (<1%) validates the robustness of spur gear design under dynamic loads.
- Meshing Force Fluctuations: Sudden load applications induce transient force spikes, emphasizing the need for shock-absorbing mechanisms.
- Stress Localization: High root stresses suggest potential for tooth bending fatigue, necessitating material or geometric optimizations.
5. Conclusion
This study demonstrates the efficacy of ADAMS in simulating spur gear dynamics, providing critical insights into transmission stability, meshing force patterns, and stress distribution. Future work could incorporate thermal effects, lubrication models, and nonlinear material properties to enhance simulation accuracy. By optimizing spur gear design through virtual prototyping, industries can achieve longer service life, reduced maintenance costs, and improved operational efficiency.