The automotive industry has witnessed remarkable advancements over the years, and one of the crucial components that play a significant role in the performance and efficiency of vehicles is the spur gear. This article delves deep into the world of spur gears in automotive transmission systems, exploring their evolution, significance, and the continuous efforts to enhance their performance to meet the ever-growing demands of modern transportation.
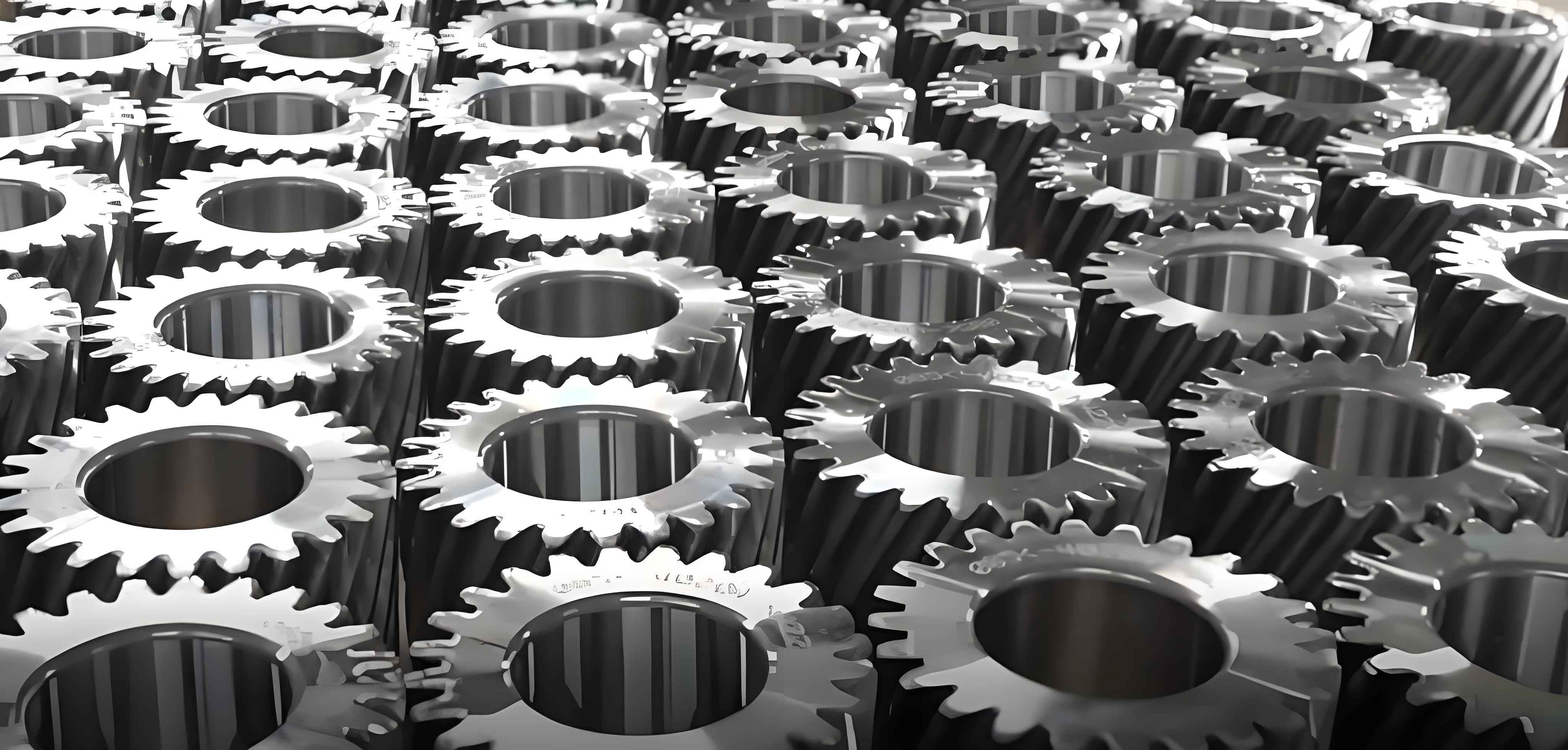
I. Introduction
Spur gears are fundamental mechanical components found in automotive transmission systems. They consist of cylindrical gears with straight teeth that mesh together to transfer power and rotational motion. The simplicity and reliability of spur gears make them widely used in various automotive applications, from manual transmissions to automatic ones.
II. The Function of Spur Gears in Automotive Transmissions
Spur gears are responsible for transmitting torque and speed between different components within the transmission system. They enable the engine’s power to be efficiently distributed to the wheels, allowing for smooth acceleration, deceleration, and gear shifting. The precise meshing of spur gears ensures minimal power loss and maximum mechanical efficiency.
III. Evolution of Spur Gears in Automotive History
- Early Automotive Applications
In the early days of automobiles, spur gears were relatively simple and crude. They were made of basic materials and lacked the sophistication and precision seen in modern designs. - Technological Advancements
As automotive engineering progressed, spur gears underwent significant improvements. Materials such as alloy steels and heat-treated metals were introduced to enhance strength and durability. Manufacturing processes like precision machining and gear grinding became more refined, resulting in gears with better tooth profiles and reduced noise and vibration. - Modern Developments
Today, spur gears are designed using advanced computer-aided design (CAD) and simulation software. This enables engineers to optimize gear geometries for improved performance, reduced weight, and enhanced fuel efficiency.
IV. Key Factors Affecting Spur Gear Performance
- Tooth Profile and Geometry
The shape and dimensions of the gear teeth have a profound impact on the performance of spur gears. Different tooth profiles, such as involute and modified involute, offer varying degrees of smoothness, noise reduction, and load-carrying capacity. - Material Selection
The choice of materials for spur gears is crucial. High-strength alloys, composites, and special steels are used to withstand the high loads and stresses encountered in automotive transmissions. - Heat Treatment and Surface Finish
Proper heat treatment processes and surface finishes improve the hardness, wear resistance, and fatigue life of spur gears. - Lubrication
Adequate lubrication is essential to minimize friction and heat generation between the meshing gears, ensuring long-term reliability and performance.
V. Challenges and Limitations of Spur Gears
- Noise and Vibration
Despite advancements, spur gears can still generate noise and vibration, especially at high speeds and under heavy loads. This can affect the driving comfort and overall vehicle NVH (Noise, Vibration, and Harshness) characteristics. - Limited Torque Capacity
Spur gears have certain limitations in terms of torque transmission. In high-performance applications, alternative gear types or combinations may be necessary to handle extreme power outputs. - Weight and Space Constraints
In modern automotive designs, where weight reduction and space optimization are critical, spur gears need to be designed to be compact and lightweight without sacrificing performance.
VI. Advances in Spur Gear Manufacturing Technologies
- CNC Machining
Computer Numerical Control (CNC) machining has revolutionized the manufacturing of spur gears, allowing for precise and complex geometries to be achieved with high repeatability. - Additive Manufacturing
Emerging additive manufacturing techniques, such as 3D printing, offer new possibilities for creating custom-designed spur gears with unique properties and complex internal structures. - Gear Hobbing and Shaping
Traditional gear manufacturing methods like hobbing and shaping continue to be refined and improved to meet the demanding requirements of modern spur gears.
VII. Spur Gears in Electric and Hybrid Vehicles
With the rise of electric and hybrid vehicles, spur gears face new challenges and opportunities. The different torque characteristics of electric motors require specific gear designs and ratios to optimize performance and energy efficiency.
VIII. Future Trends and Outlook for Spur Gears in Automotive Transmissions
- Materials Innovation
Research is ongoing to develop new materials with superior mechanical properties, lightweight characteristics, and enhanced heat dissipation capabilities for spur gears. - Intelligent Design and Optimization
The integration of artificial intelligence and machine learning in gear design will enable more accurate predictions and optimizations based on real-time operating conditions and usage patterns. - Multi-Speed Transmissions
The trend towards multi-speed transmissions will require more complex spur gear arrangements and control strategies to achieve seamless shifting and improved fuel economy.
IX. Conclusion
Spur gears have come a long way in automotive transmission systems, evolving to meet the ever-increasing demands for higher performance, efficiency, and reliability. While they face challenges and limitations, ongoing technological advancements and innovations in materials, manufacturing, and design hold great promise for the future of spur gears in the automotive industry.
As vehicles continue to become more advanced and environmentally friendly, the role of spur gears will remain crucial, and their continuous development will be essential in shaping the future of transportation.