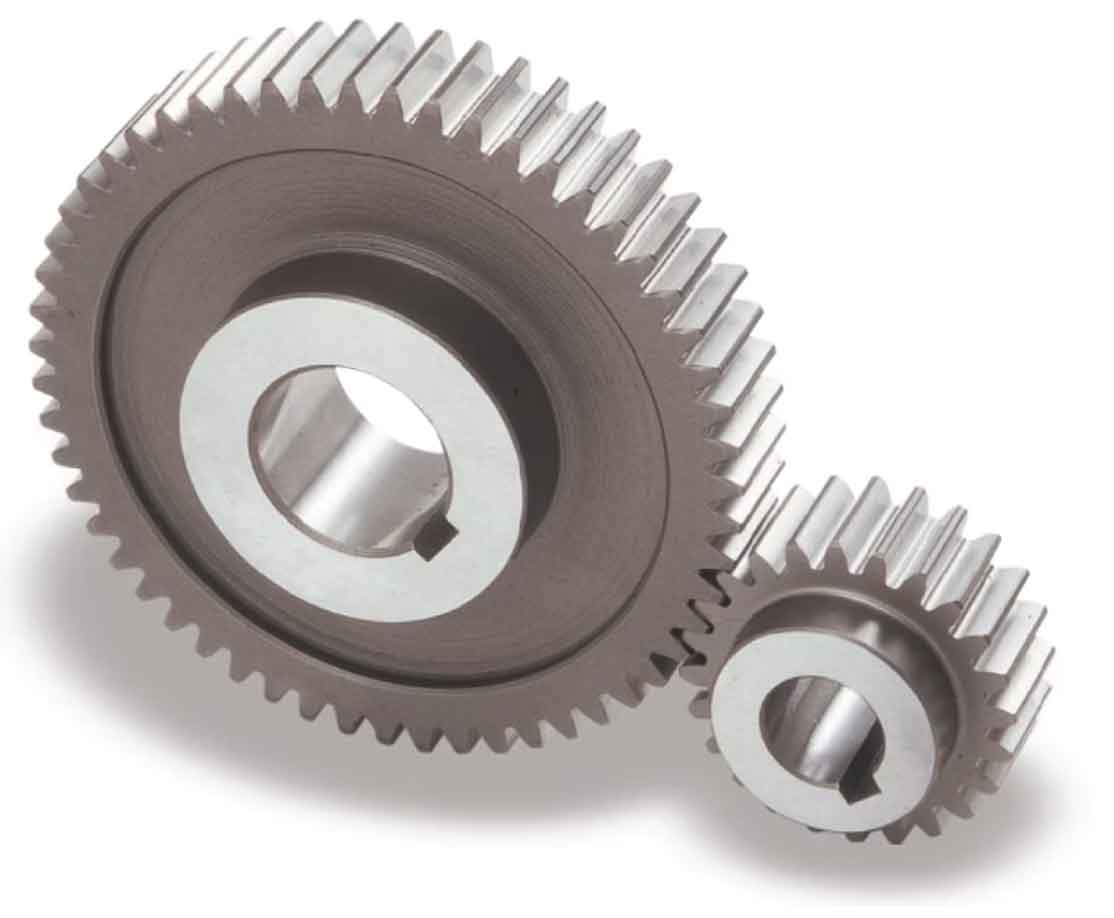
Spur gear manufacturing has witnessed significant innovations and advancements over the years, driven by technological developments and the need for more efficient and accurate production processes. These innovations have improved the quality, precision, and productivity of spur gear manufacturing. Here are some notable advancements in spur gear manufacturing:
1. CNC Machining:
Computer Numerical Control (CNC) machining has revolutionized spur gear manufacturing. CNC machines offer high precision and flexibility, allowing for the production of complex gear geometries with tight tolerances. CNC machining enables the efficient and automated production of spur gears, resulting in improved accuracy, repeatability, and productivity.
2. Gear Hobbing and Shaping:
Gear hobbing and shaping are traditional methods of manufacturing spur gears, and they have also seen advancements. Hobbing is a process where a cutting tool called a hob is used to generate gear teeth progressively. Shaping involves a reciprocating cutter called a gear shaper that cuts the teeth one at a time. Modern advancements in tooling, machine design, and control systems have enhanced the efficiency, accuracy, and speed of these processes.
3. High-Precision Grinding:
Grinding is a precision machining process used to achieve high gear accuracy and surface finish. Advancements in grinding technology, including the use of advanced abrasives, precision grinding machines, and advanced control systems, have improved the quality and dimensional accuracy of spur gears. Grinding ensures precise tooth profiles, improved gear meshing, and reduced noise and vibration levels.
4. 3D Printing and Additive Manufacturing:
Additive manufacturing, commonly known as 3D printing, has opened up new possibilities in spur gear production. 3D printing allows for the direct manufacturing of complex gear geometries, including internal and custom tooth profiles. This technology enables the production of prototypes, small batches, and customized spur gears with reduced lead times and increased design freedom.
5. Advanced Gear Inspection and Metrology:
Advancements in gear inspection and metrology equipment have significantly improved the quality control in spur gear manufacturing. Coordinate Measuring Machines (CMMs), gear analyzers, and optical scanning systems with advanced software algorithms enable accurate measurement and analysis of gear tooth profiles, dimensions, and geometrical tolerances. This ensures compliance with stringent quality standards and enables continuous process improvement.
6. Simulation and Virtual Prototyping:
Simulation and virtual prototyping tools have played a significant role in optimizing spur gear manufacturing processes. Computer-aided design (CAD) software, along with finite element analysis (FEA) and computational fluid dynamics (CFD) simulations, allows for virtual testing and optimization of gear designs, material selection, heat treatment processes, and performance characteristics. This reduces the time and cost involved in physical prototyping and ensures better manufacturing outcomes.
7. Automation and Robotics:
Automation and robotics have been employed to enhance the efficiency and productivity of spur gear manufacturing. Automated systems for material handling, loading/unloading, and in-process inspection streamline the production process and reduce human error. Robotic systems can handle complex gear machining operations, improving process consistency and reducing cycle times.
These innovations and advancements in spur gear manufacturing have resulted in improved quality, increased productivity, enhanced precision, and greater design flexibility. Manufacturers can now produce spur gears with tighter tolerances, complex geometries, and improved performance characteristics. The integration of advanced technologies and processes has led to more efficient and cost-effective spur gear production, meeting the evolving demands of industries such as automotive, aerospace, industrial machinery, and more.