Spur gear transmission is widely used in the fields of machinery, electronics, textile, metallurgy, mining, automobile, aviation, aerospace and shipbuilding. As an essential important mechanical component to transmit motion and power, with the rapid development of Chinese industry, the rotating speed of rotating machinery is increasing, and its performance is also improving, which makes this subject become the focus of research. When the machine is running, the transmission system often vibrates, and the vibration will bring noise, which will reduce the work efficiency, seriously damage the components and destabilize the rotor, resulting in major safety accidents. On ships, high-speed diesel engines, steam turbines, gas turbines, etc. are widely used as main propulsion devices. When they do not match the speed of the engine propeller, they need to be equipped with a spur gear reduction unit to achieve the best speed of the propeller, so as to improve the propulsion efficiency of the rotor and reduce the occurrence of cavitation effect.
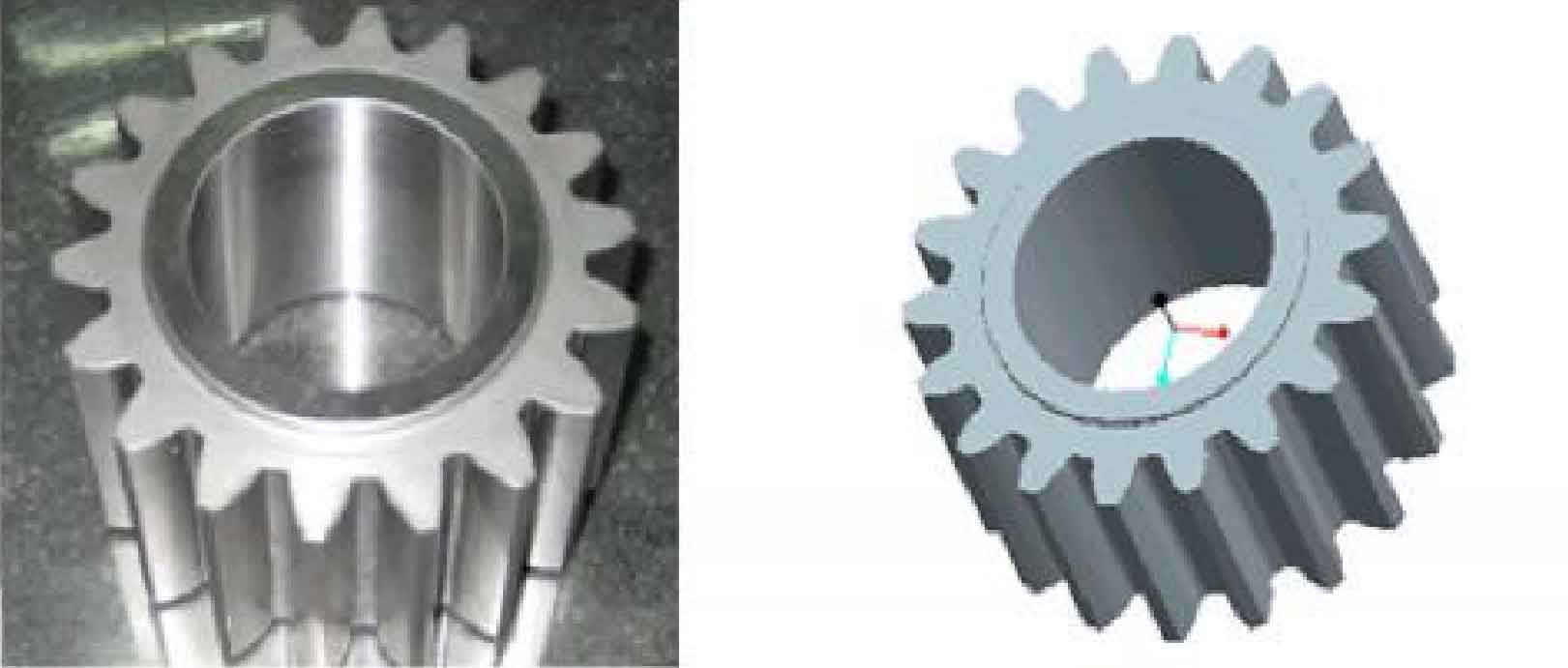
With the rapid development of metallurgy, machinery, building materials and transportation industries, high-speed and heavy-duty spur gears are widely used in high-speed trains and aeroengines. Due to the constant power transmission characteristics of spur gear transmission, spur gear transmission is widely used in these industries, and the power and speed transmitted by high-speed and heavy-duty spur gear transmission are moving towards a higher goal. Generally speaking, spur gears with speed higher than 3000r/min or linear speed greater than 25m/s are called high-speed spur gears. When the load coefficient of the tooth surface is greater than 2MPa, it is called heavy duty spur gear. The power transmitted by spur gears in foreign countries can reach more than 100000kw, the speed has also exceeded 100000r/min, the circumferential speed has also exceeded 300m/s, and the tooth surface load factor is also greater than 3Mpa. However, the data of China in the late 1990s show that the maximum transmission power transmitted by spur gears in China was only 36000 kW, the maximum linear speed was 150m/s, and the load factor was only 2.5MPa. This technical index is far behind developed countries.
Although this backward situation has changed with the research and development in the past 10 years, due to the rapid development of China’s energy, chemical, machinery, metallurgy and other industries, a large number of high-performance spur gears are urgently needed, so China has to spend a lot of foreign exchange every year to buy foreign spur gear equipment. Therefore, the technical problem of improving the dynamic performance of spur gears to adapt to the development of the industry has been put in front of the spur gear industry.
Because the linear speed of high-speed and heavy-duty spur gears is large, it also brings greater vibration and noise, and the deformation of gear teeth and the stress at the root of gear teeth become larger. Due to more traditional static design methods and less introduction of dynamic design, it is a prominent problem in the research and design methods of spur gears in China at present. Only the design accuracy of a single spur gear is considered without analysis in combination with the actual working conditions, and the dynamic model mostly adopts linear model, which makes the design deficiency more obvious. At the same time, China’s research on high-speed and heavy-duty spur gears is still in the traditional design methods of design, manufacturing and maintenance. Although some characteristics of spur gears are taken into account in the design process, technologies in the fields of nonlinear dynamics, engineering materials and tribology are not widely used in the field of spur gear research, and the performance in all aspects can not meet the needs of the rapid development of the industry.