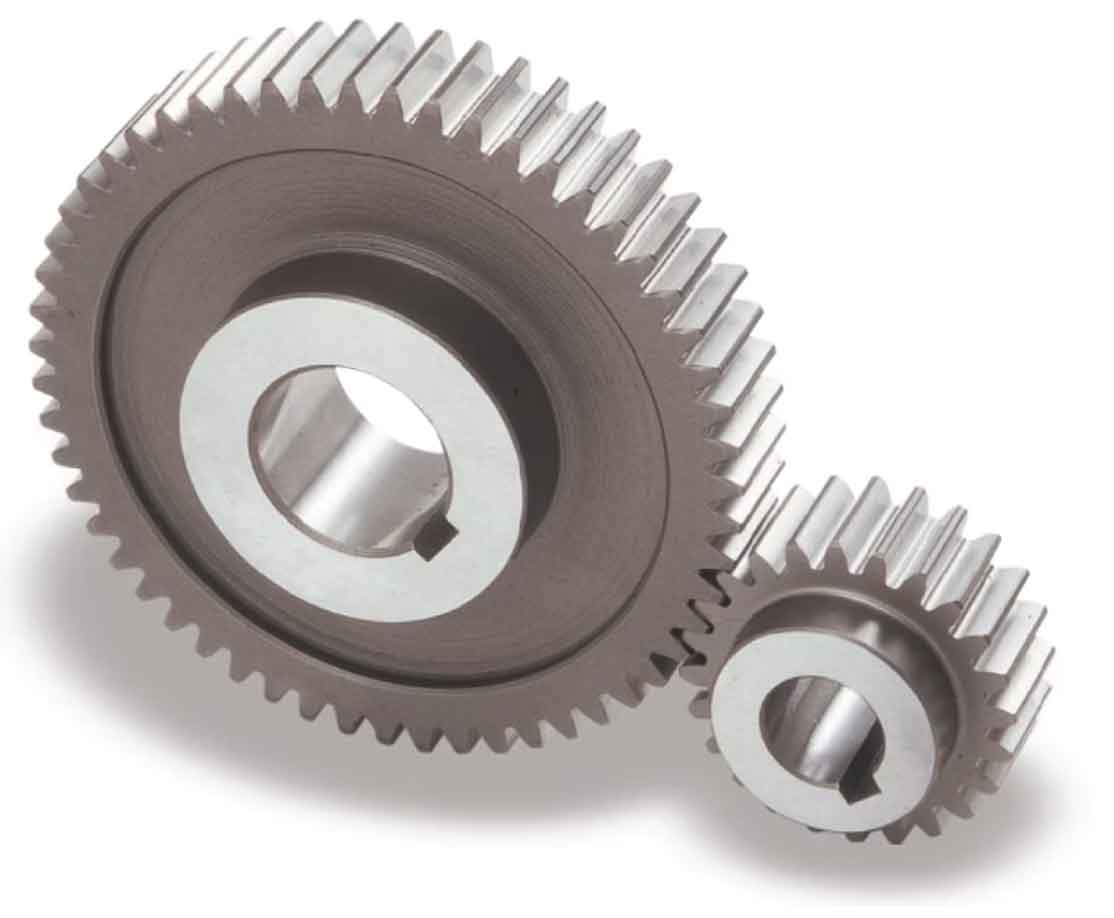
When selecting the right gear type for your specific needs, it’s important to consider the advantages, limitations, and application requirements of each gear type. Let’s compare spur gears with other commonly used gear types to help you make an informed decision:
Spur Gears:
Advantages:
- Simple and cost-effective design.
- Precise speed control and motion transfer.
- High efficiency in power transmission.
- Wide availability and compatibility with standard components.
Limitations:
- Generates noise and vibration, especially at high speeds.
- Limited load-carrying capacity compared to other gear types.
- Cannot transmit motion between non-parallel shafts.
- Backlash may affect positioning accuracy in some applications.
Applications:
Spur gears are suitable for applications that require simplicity, precise speed control, and efficient power transmission. They find use in gearboxes, conveyors, machine tools, and applications where parallel shafts are involved.
Helical Gears:
Advantages:
- Smoother and quieter operation compared to spur gears due to helical teeth.
- Higher load-carrying capacity and torque transmission.
- Can transmit motion between non-parallel shafts (depending on the helix angle).
- Overlapping teeth engagement reduces backlash.
Limitations:
- Slightly lower efficiency compared to spur gears due to sliding contact.
- Complex design and manufacturing process compared to spur gears.
- Requires thrust bearings to counteract axial thrust.
Applications: Helical gears are commonly used in applications that require higher torque, smooth operation, and the ability to transmit motion between non-parallel shafts. They are found in gearboxes, automotive transmissions, pumps, and heavy machinery.
Bevel Gears:
Advantages:
- Ability to transmit motion between intersecting or non-parallel shafts.
- Efficient power transmission with high torque capacity.
- Various types available, including straight, spiral, and hypoid bevel gears.
- Compact design and versatile applications.
Limitations:
- Complex design and manufacturing process.
- Requires precision alignment and bearing support.
- Spiral and hypoid bevel gears can generate axial and radial forces.
Applications:
Bevel gears are used in applications that require the transmission of motion between intersecting or non-parallel shafts. They are commonly found in automotive differentials, marine propulsion systems, and machinery with changing drive directions.
Worm Gears:
Advantages:
- High torque transmission with a compact design.
- Provides large speed reduction ratios.
- Self-locking capability prevents reverse rotation.
- Smooth and quiet operation.
Limitations:
- Relatively lower efficiency due to sliding contact and heat generation.
- Requires careful lubrication to prevent wear.
- Limited load-carrying capacity.
Applications:
Worm gears are suitable for applications that require high torque transmission, speed reduction, and self-locking characteristics. They find use in conveyors, lifts, packaging machinery, and certain automotive systems.
Choosing the right gear type depends on various factors, including the specific application requirements, load capacity, speed control needs, space limitations, and cost considerations. Consulting with a mechanical engineer or gear specialist can provide further guidance based on your specific application.