Because the stiffness excitation and error excitation only select the first harmonic, the r = 1 of SSI = 0 has 15 unknowns. After the steady-state response q is solved, f (q) is obtained by substituting it into equation (4-7). According to the value range of F (q), the gear slapping state can be judged. In Fig. 1, the curve of dimensionless relative displacement f (q) corresponding to the reducer variable speed integrated gear is given. In a time-varying instantaneous center period, the curve contains the alternation of multiple zero and negative values (q) All the values are not greater than zero, which indicates that there is a single side slap phenomenon of multiple contact disengagement re contact on the driving side. If there are only positive or negative values in the curve, the gear will not rattle; if the curve contains both positive and negative values, the gear will produce bilateral slapping. In the reducer variable speed integrated gear, the unilateral impact is a part of the vibration period, which is the difference between the gear and the circular gear.
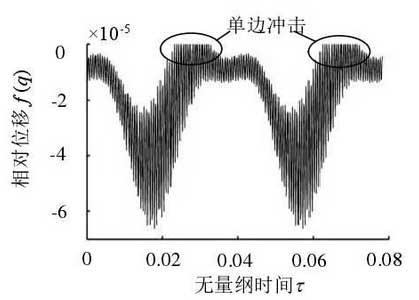
Keep the other parameters in table 4-1 unchanged, only change the input speed of the input pinion. Take the input speeds as ω 1 = 140 rad / s and ω 1 = 180 rad / s respectively, and the corresponding curves of dimensionless relative displacement f (q) are shown in Fig. 2. When the input speed ω 1 = 140 rad / s, the dimensionless relative displacement f (q) curve is shown in Fig. 2a), and the values of F (q) are all less than 0. Therefore, we can infer that the gear always keeps in contact during the whole meshing process, and the whole meshing Q (f) displacement is periodic vibration, and there is no slapping phenomenon; when the rotation speed of the pinion is ω 1 = 180 rad / s, the dimensionless relative displacement is There are positive, negative and zero values of F (q), as shown in Fig. 2b), which indicates that the gear will contact the non driving side after separation from the driving side, and in the process, a bilateral impact state occurs.
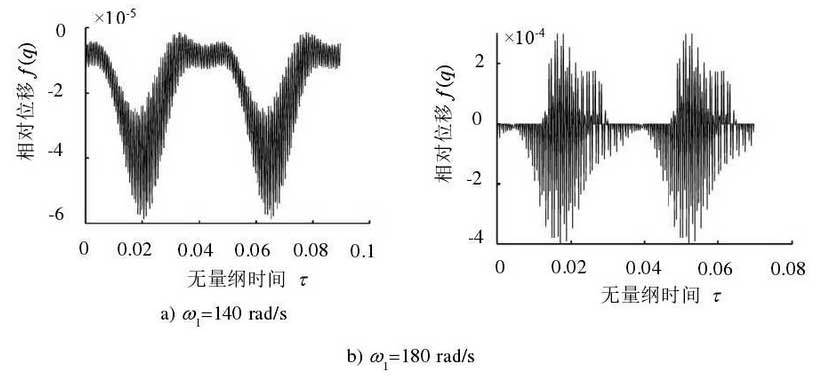
By solving the steady-state response of Q under different parameters, the influence of input speed, static transmission error, eccentricity, time-varying meshing stiffness and load torque on the vibration state of the gear is analyzed.
The tooth side clearance is the clearance between teeth which must be reserved in the process of gear design and manufacturing. The purpose is to lubricate the gear teeth and reduce friction heat generation. The meshing process of gear teeth can be divided into three situations: forward meshing, tooth shedding and reverse meshing. Different settings of system parameters may make the gear system in three completely different slapping states
(1) The teeth always keep in contact with each other, that is, non impact state;
(2) The gear teeth are separated, but only contact impact occurs on the driving side surface, that is, unilateral impact state;
(3) The teeth are separated and contact occurs at the driving side and non driving side at the same time.
In order to study the influence of system parameters on gear slapping state more conveniently, a new parameter RSV is proposed, which is set as RSV = 0, 1 and 2, which correspond to non impact state, unilateral impact state and bilateral impact state respectively. In addition, PPV is called the peak to peak value of steady-state response, which is used to reflect the severity of Gear Rattling vibration.