Straight bevel gears play a crucial role in ensuring smooth and reliable power transmission in various applications. Here are some key factors that contribute to their ability to deliver efficient and dependable power transmission:
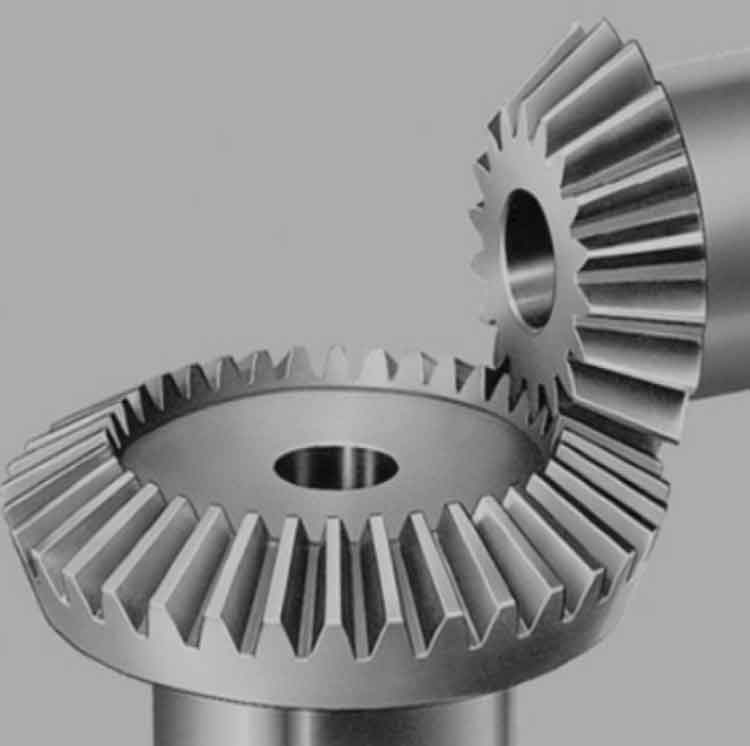
- Precision Manufacturing: Straight bevel gears are manufactured using high-precision techniques such as CNC machining, gear grinding, and quality control measures. This ensures the accurate formation of gear teeth and tight tolerances, resulting in smooth and precise gear meshing. The precise manufacturing processes contribute to minimal backlash and optimal contact patterns, reducing noise, vibration, and power losses.
- Optimized Tooth Geometry: The tooth geometry of straight bevel gears is carefully designed to achieve efficient power transmission. Factors such as tooth profile, pressure angle, and helix angle are optimized to distribute the load evenly and minimize stress concentrations. This promotes smooth engagement and disengagement of gear teeth, reducing wear and enhancing the overall reliability of the power transmission system.
- Proper Lubrication: Adequate lubrication is essential for the smooth operation and longevity of straight bevel gears. Lubricants reduce friction, dissipate heat, and prevent excessive wear between the gear teeth. Proper lubrication also helps in reducing noise and vibration by maintaining a thin film of lubricant between the mating surfaces, ensuring smooth power transmission.
- Alignment and Assembly: Accurate alignment and precise assembly of straight bevel gears are crucial for optimal performance. Proper alignment ensures that the gears mesh correctly, minimizing wear and maximizing efficiency. Skilled assembly techniques, including gear tooth meshing verification and appropriate torque application, are employed to ensure reliable power transmission and minimize the risk of gear failure.
- Material Selection: Straight bevel gears are manufactured from high-quality materials that possess excellent strength, durability, and wear resistance. Materials such as alloy steels, case-hardened steels, or specialized alloys are selected based on the specific application requirements. The right material choice ensures that the gears can withstand the transmitted forces and provide reliable power transmission over an extended period.
- Maintenance and Inspection: Regular maintenance and inspection are essential to ensure the ongoing smooth and reliable operation of straight bevel gears. Scheduled maintenance includes periodic lubricant replacement, gear inspection for wear or damage, and alignment checks. Routine inspections help identify any issues early on, allowing for timely repairs or replacements and preventing catastrophic failures.
- Load Distribution and Capacity: Straight bevel gears are designed to handle specific load capacities based on the application requirements. Proper load distribution across the gear teeth ensures that the load is shared evenly, preventing excessive stress on any individual tooth. The gear design and tooth contact pattern are optimized to accommodate the anticipated loads, resulting in reliable power transmission.
By considering these factors and implementing appropriate design, manufacturing, lubrication, alignment, and maintenance practices, straight bevel gears can ensure smooth and reliable power transmission in a wide range of applications. Their ability to deliver efficient torque transfer, minimal backlash, and reliable operation makes them a preferred choice in many industrial sectors, including automotive, aerospace, power generation, and more.